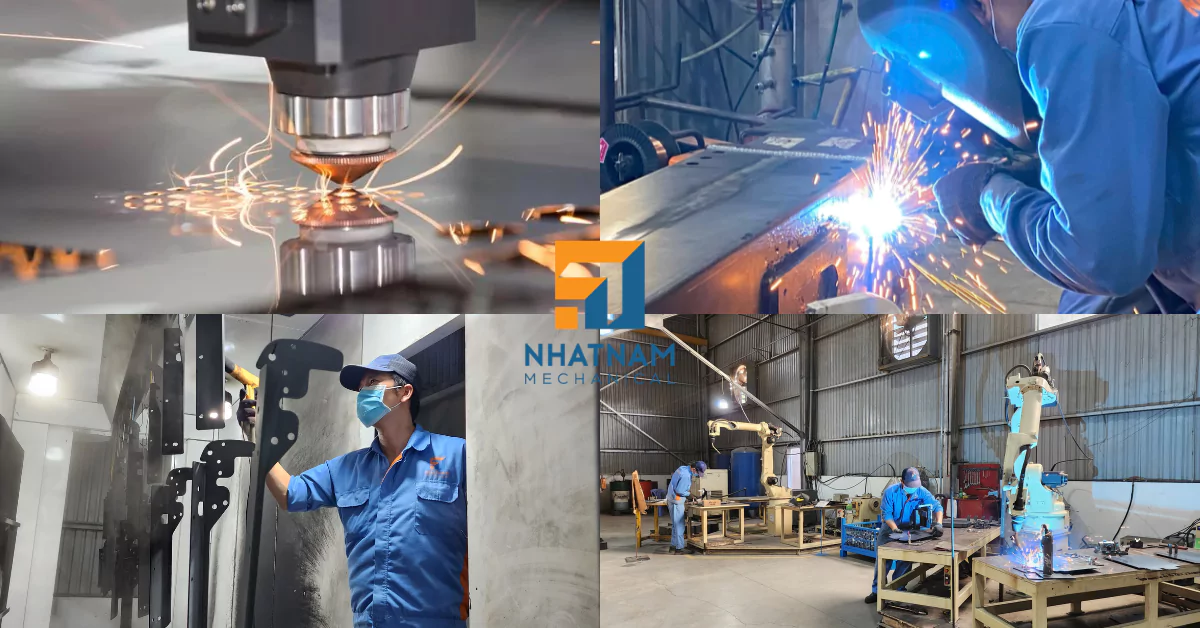
The sheet metal fabrication process is a fundamental method used in various industries to create precision metal parts and components. From design to production, mastering this process requires knowledge of advanced techniques and the right tools to ensure high-quality results. In this guide, we’ll walk you through each stage of the process, helping you understand how to achieve efficiency and precision in sheet metal fabrication.
What is Sheet Metal Fabrication?
Sheet metal fabrication is the process of turning flat metal sheets into functional parts through fabrication techniques like cutting, bending, and assembling . This process is widely used in industries such as automotive, aerospace, construction, and electronics, where custom metal parts are essential for both production and infrastructure.
The Importance of Design in Sheet Metal Fabrication
Before any metal is cut or bent, the design phase plays a crucial role in ensuring the success of the fabrication process. Designers use advanced CAD (Computer-Aided Design) software to create detailed blueprints of the part. These designs optimize the dimensions and tolerances, minimizing waste and maximizing efficiency during production.
CAD Software and Design Optimization
Using CAD software allows for intricate designs with high precision, ensuring that the final product meets exact specifications. Additionally, design optimization helps reduce material usage and improves manufacturability, making the production process faster and more cost-effective.
Key Steps in the Sheet Metal Fabrication Process
Cutting: From Traditional Methods to CNC Laser Cutting
The first step in sheet metal fabrication is cutting the metal sheets into the desired shapes. Traditional methods like shearing are still used, but modern shops now rely on CNC laser cutting and fiber laser cutting for enhanced precision and speed.
CNC machines are computer-controlled, allowing for accurate cuts with minimal waste.
Bending and Forming Techniques
After cutting, the next stage is bending or forming the metal into the required shape. CNC bending machines use programmed commands to bend the metal precisely.
This is a critical step, as errors in bending can lead to parts that don’t fit or function as intended.
Assembly and Welding
In many cases, metal parts need to be assembled into larger structures. This involves welding, which joins two or more metal pieces together.
There are various welding techniques, such as TIG and MIG welding, depending on the type of metal and the desired strength of the joint.
Finishing: Surface Treatment and Coating
Once the parts are assembled, the finishing process begins. This can include polishing, painting, or powder coating to improve the appearance and durability of the product. Finishing treatments also protect the metal from corrosion and wear, extending its lifespan.
Tools and Equipment Used in Sheet Metal Fabrication
High-quality fabrication requires the use of advanced machinery. Some of the key tools include:
- CNC Laser Cutters: For precision cutting.
- Press Brakes: Used for accurate bending.
- Welding Machines: For assembling parts through various welding techniques.
- Punch Presses: For punching holes or forming shapes in metal sheets.
Each tool plays a crucial role in ensuring the efficiency and accuracy of the fabrication process.
Common Materials in Sheet Metal Fabrication
Sheet metal fabrication typically involves a variety of metals, depending on the application:
- Stainless Steel: Known for its corrosion resistance and strength, stainless steel is widely used in industries like medical devices and kitchen appliances.
- Aluminum: Lightweight and durable, aluminum is a popular choice in the automotive and aerospace industries.
- Copper: With excellent conductivity, copper is used in electrical components and wiring.
Choosing the right material is essential for achieving the desired performance and longevity of the fabricated part.
Quality Control in Sheet Metal Fabrication
Quality control is integral to every stage of the fabrication process. From ensuring the accuracy of cuts and bends to verifying the strength of welds, every detail must be inspected. This is where inspection tools such as calipers, laser measurement systems, and testing equipment come into play. Strict quality control ensures that each part meets the required standards before it leaves the fabrication shop.
At Nhat Nam, we take pride in being a leading unit in the field of metal punching with advanced technology. With a team of experienced engineers and a fully automated process, we are committed to delivering high-quality products that quickly and flexibly meet all customer requirements. Contact us to learn more about metal processing services at Nhat Nam Mechanical Company.
NHAT NAM MECHANICAL CO., LTD contact information: House No. 36, Garland – Phuoc Dien, 72 Duong Dinh Hoi, Phuoc Long B Ward, District 9, Ho Chi Minh City, Vietnam
Contact Japan
Email: tranquy@cokhinhatnam.vn
Tel: +84 938 771 508
Contact English
Email: marketing@cokhinhatnam.vn
Tel: +84 964 092 079
Contact Viet Nam
Email: vinhnt@cokhinhatnam.vn
Tel: +84 964 084 479