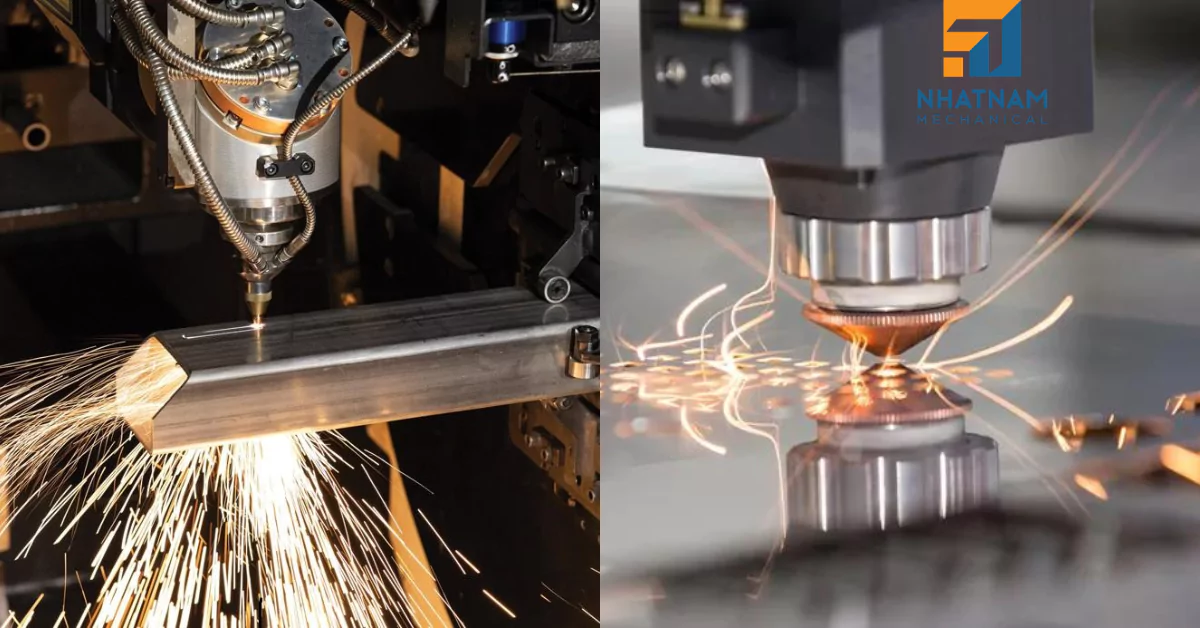
In today’s fast-paced industrial landscape, custom manufacturing has become essential for businesses seeking flexibility, precision, and efficiency. Whether it’s creating unique components for a product or optimizing designs for better performance, sheet metal fabrication plays a pivotal role in making these tailored solutions possible. Here’s why sheet metal fabrication is key to achieving customized manufacturing goals:
1. Versatility Across Industries
Sheet metal fabrication is one of the most adaptable manufacturing processes. It serves industries ranging from automotive and aerospace to electronics and construction. The ability to cut, bend, and shape sheet metal into virtually any form allows manufacturers to create components that meet highly specific design requirements. This versatility makes it the go-to solution for custom manufacturing needs, where each project may have unique demands.
2. Precision and Accuracy
One of the biggest advantages of sheet metal fabrication is the precision it offers. Advanced techniques like laser cutting, CNC machining allow for incredibly tight tolerances, ensuring that every component is manufactured to exact specifications. This level of accuracy is crucial in custom manufacturing, where even the smallest deviation can impact product performance or assembly compatibility.
3. Scalability and Flexibility
Custom manufacturing often requires the ability to scale production up or down, depending on demand. Sheet metal fabrication provides the flexibility to handle both small prototype runs and large-scale production with equal efficiency. Manufacturers can easily adjust production volumes without compromising on quality, which is vital for businesses that need to adapt to changing market conditions.
4. Cost-Effectiveness
While custom solutions are often associated with higher costs, sheet metal fabrication offers a cost-effective approach. By using standardized tools and machinery, along with automated processes, manufacturers can reduce labor costs and minimize material waste. Additionally, the durability and strength of metals such as steel, aluminum, and copper make them ideal for long-lasting components, providing excellent value over time.
5. Design Freedom and Customization
Sheet metal fabrication allows for extensive design freedom. Manufacturers can work with engineers and designers to create custom components that fit specific needs—whether it’s a unique shape, size, or function. The ability to bend, weld, and assemble sheet metal in different configurations makes it possible to develop innovative solutions that enhance product performance or aesthetic appeal.
6. Durability and Reliability
When it comes to custom manufacturing, the durability of materials is non-negotiable. Sheet metal, known for its strength and resilience, ensures that custom-fabricated parts can withstand demanding environments and heavy use. From corrosion-resistant coatings to high-strength alloys, sheet metal components offer reliable performance that meets the strict standards of industries like aerospace, defense, and medical equipment.
7. Sustainability and Efficiency
Sustainability is becoming an increasingly important factor in manufacturing. Sheet metal is not only durable but also recyclable, making it an eco-friendly choice for custom manufacturing solutions. By reducing waste through efficient fabrication methods and recycling leftover materials, manufacturers can lower their environmental impact while still producing high-quality custom components.
8. Speed and Efficiency in Prototyping
In custom manufacturing, speed is often critical. Sheet metal fabrication offers rapid prototyping capabilities, allowing manufacturers to quickly create and test designs before committing to full-scale production. This process helps identify potential design flaws early, reducing time to market and minimizing costly revisions.
At Nhat Nam, we take pride in being a leading unit in the field of metal punching with advanced technology. With a team of experienced engineers and a fully automated process, we are committed to delivering high-quality products that quickly and flexibly meet all customer requirements. Contact us to learn more about metal processing services at Nhat Nam Mechanical Company.
NHAT NAM MECHANICAL CO., LTD contact information: House No. 36, Garland – Phuoc Dien, 72 Duong Dinh Hoi, Phuoc Long B Ward, District 9, Ho Chi Minh City, Vietnam
Contact Japan
Email: tranquy@cokhinhatnam.vn
Tel: +84 938 771 508
Contact English
Email: marketing@cokhinhatnam.vn
Tel: +84 964 092 079
Contact Viet Nam
Email: vinhnt@cokhinhatnam.vn
Tel: +84 964 084 479