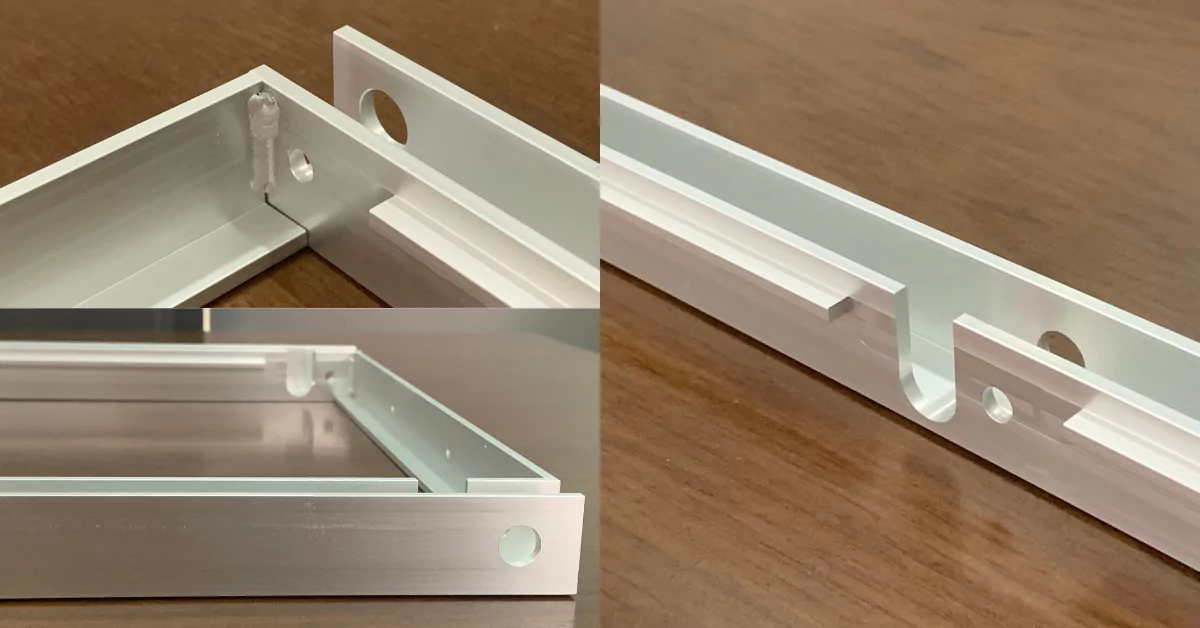
Given its widespread use, it is highly likely that you will require aluminum fabrication services to meet your project goals. If the weight of the assembly is critical to your design, aluminum is likely your best choice due to its lightweight nature and excellent strength-to-weight ratio. This makes it ideal for applications where minimizing weight without compromising durability is essential.
What is Aluminum fabrication?
Aluminum fabrication is the process of transforming aluminum from raw material into finished products through operations such as cutting, bending, stamping, welding, and surface finishing. It requires high technical expertise and the use of modern equipment to ensure the final products meet requirements for precision, durability, and aesthetic appeal. Aluminum is widely chosen across industries for its lightweight nature, corrosion resistance, making it suitable for diverse applications from automotive and electronics to construction and household goods.
How to fabrication Aluminum? The key considerations
Aluminum Extrusion Method
The extrusion method is a process of manufacturing aluminum by heating aluminum billets to a temperature range of 700 – 900 degrees Fahrenheit. The heated billets are then pushed through a steel die using high pressure to create the desired aluminum cross-sectional shapes. After extrusion and cutting to size, the aluminum profiles are aged to increase hardness and mechanical strength.
Notes on Aluminum Extrusion Processing
- Choose the Right Material: Ensure that you select the appropriate type of aluminum for the specific application. Aluminum comes in various alloys, each with its own characteristics. Identify the usage requirements to choose the correct material.
- Check Size and Accuracy: Before processing, check the size and accuracy of the aluminum billet. This ensures that the extruded product meets the desired dimensions.
- Temperature Control: The extrusion process requires precise temperature control. Ensure the correct temperature to guarantee the efficiency of the extrusion process.
- Choose the Right Extrusion Die: The extrusion die must be designed to match the shape and size of the final product. Ensure the die is strong enough to withstand the extrusion pressure.
- Check Extrusion Pressure: Adjust the extrusion pressure correctly to ensure the aluminum deforms as required. Both excessive and insufficient pressure can affect product quality.
- Check Extrusion Speed: Adjust the extrusion speed to match the type of aluminum and the size of the product. Extrusion that is too fast or too slow can lead to defects.
- Check Crystal Structure: Extrusion can affect the crystal structure of aluminum. Inspect the structure after processing to ensure quality.
Aluminum Casting Method
Casting is a process used to shape aluminum into relatively complex forms. The essence of this technique involves completely melting aluminum alloy ingots and injecting the molten metal into a mold.
The poured metal will completely fill the cavity and then solidify to take the shape of the mold. Casting can be performed using various types of molds, including die molds, permanent molds, clay molds, and sand molds.
The ability to create products with complex shapes is the main advantage of the aluminum casting method compared to other aluminum forming processes.
Common Methods of Aluminum Machining
Aluminum machining involves shaping, cutting, and carving metal products from aluminum billets using cutting tools such as lathes, milling machines, drills, saws, and grinders. This method ensures that products achieve the desired dimensions and shapes.
For optimal performance in aluminum machining, in addition to selecting the appropriate cutting materials, it is important to use suitable lubricants and coolants:
- High Lubricity: Use cutting oils with high lubricity to reduce friction and machining temperature.
- Anti-Adhesion: Choose cutting oils with anti-adhesion properties to prevent metal chips from sticking to the cutting tools.
- Anti-Oxidation: Protect the machined surface with anti-oxidation features.
CNC Laser Cutting Method
CNC laser cutting uses a powerful laser beam to cut through aluminum sheets, creating aluminum products with high precision and smooth surfaces. This technology offers flexibility and fast machining speeds.
Notes on CNC Laser Cutting of Aluminum:
- High Reflectivity Material: Aluminum has high reflectivity, causing laser energy to easily reflect off the cutting head. This can heat the protective lens and nozzle, reducing the laser equipment’s lifespan.
- Select Appropriate Aluminum Type and Size: Laser cutting of aluminum depends on the machine type, power, and specific product requirements. Common aluminum grades for laser cutting include A1050, A3003, A5052, A6061, and A7075.
Aluminum Laser Welding Method
Laser welding of aluminum is a process of joining aluminum parts using a laser beam. This process focuses high temperature on the welding area, melting the aluminum surface and combining them as the material solidifies.
Cre: Video from NHATNAM MECHANICAL
Note on Aluminum Laser Welding:
- High Heat Transfer Efficiency: The laser beam concentrates heat, creating thin and precise welds.
- Quick and Efficient Cooling: Laser welding machines are gas-cooled, improving production speed.
- Automation and Precision: Uses CNC systems for welding, maintaining clean and neat welds, and is process-friendly.
- Flexibility and Convenience: Welding can be performed both indoors and outdoors.
- Fast Speed: Laser welding is faster than MIG and TIG welding.
- High Precision: Laser welding produces precise welds with minimal distortion.
- No Consumable Electrodes: Unlike TIG and MIG, there is no need to replace electrodes.
- Suitable for Thin Metals: Particularly effective for aluminum and aluminum alloys.
Anodizing Aluminum Method
In simple terms, anodizing aluminum is the process of immersing aluminum parts in an electrolytic solution (the electrolytic solution can be sulfuric acid or chromic acid). Chemical reactions occur, creating a thin layer of aluminum oxide on the surface of the aluminum part (measured in micrometers). This oxide layer is very hard and offers excellent corrosion and wear resistance.
A unique feature of this oxide layer is its ability to absorb colors well, resulting in products with diverse colors. Therefore, anodizing technology is increasingly favored and applied in many industries such as construction, electronics, automotive manufacturing, and household appliances.
Benefits and Applications of Anodized Aluminum:
Benefits:
- Increased Durability: The oxide layer creates a protective surface, enhancing corrosion and wear resistance.
- Aesthetic Appeal: Anodizing aluminum results in a brighter and more attractive surface.
- Hardness: The surface of aluminum becomes harder after anodizing.
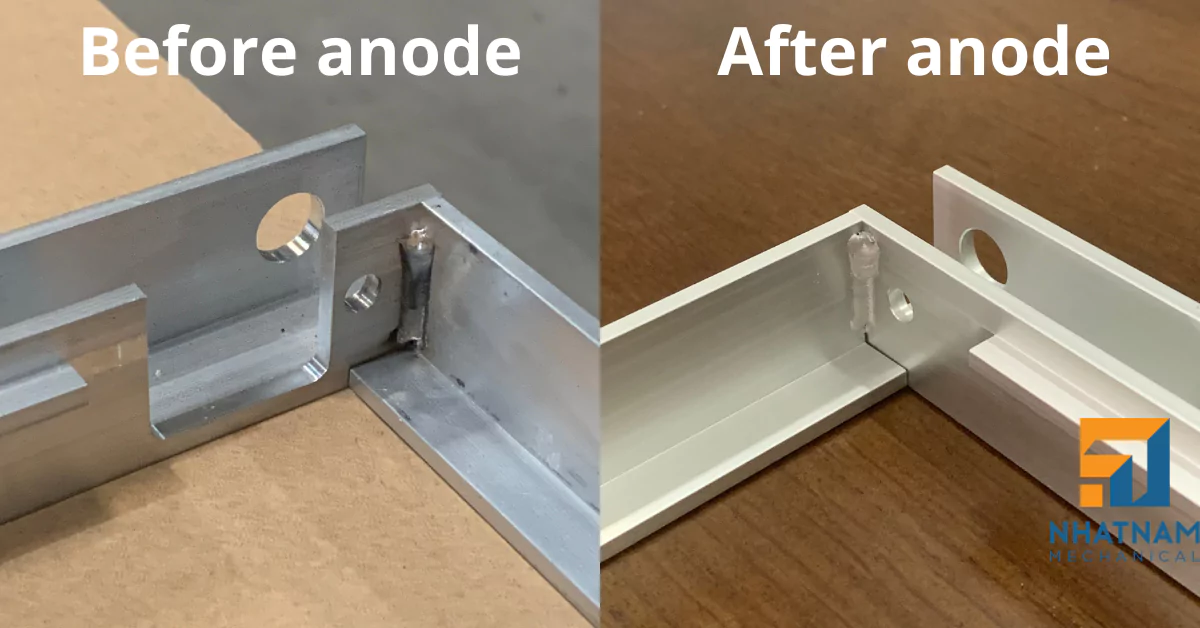
In addition to metal fabrication services, NHAT NAM MECHANICAL also meticulously inspects with testing equipment to ensure quality for your project. All products delivered to customers are carefully packaged and promptly shipped.
Regarding how Nhat Nam Mechanical’s sheet metal fabrication services can help your project involving galvanized steel, here are some ways:
- Custom Fabrication: We can work with galvanized steel sheets to fabricate custom components or structures based on your project requirements. We can cut, bend, and shape the galvanized steel to create the desired shapes and sizes.
- Welding and Joining: If your project requires the joining of galvanized steel pieces, Nhat Nam Mechanical can provide welding services to securely bond the components together. We have expertise in various welding techniques suitable for galvanized steel.
- Finishing and Surface Treatment: We can provide surface treatments for galvanized steel products, such as painting or powder coating. This can enhance the appearance, provide additional protection, or meet specific project requirements.
- Prototyping and Production: Whether you need a one-off prototype or a large production run, Nhat Nam Mechanical can assist with both. We can fabricate galvanized steel components or assemblies in the desired quantities to support your project.
It’s important to discuss your specific project requirements with Nhat Nam Mechanical to determine the extent of our capabilities and how we can best assist you with your galvanized steel fabrication needs.
NHAT NAM MECHANICAL CO., LTD contact information: House No. 36, Garland – Phuoc Dien, 72 Duong Dinh Hoi, Phuoc Long B Ward, District 9, Ho Chi Minh City, Vietnam
Contact Japan
Email: tranquy@cokhinhatnam.vn
Tel: +84 938 771 508
Contact English
Email: vananhdt@cokhinhatnam.vn
Tel: +84 964 092 079
Contact Vietnam
Email: vinhnt@cokhinhatnam.vn
Tel: +84 964 084 479