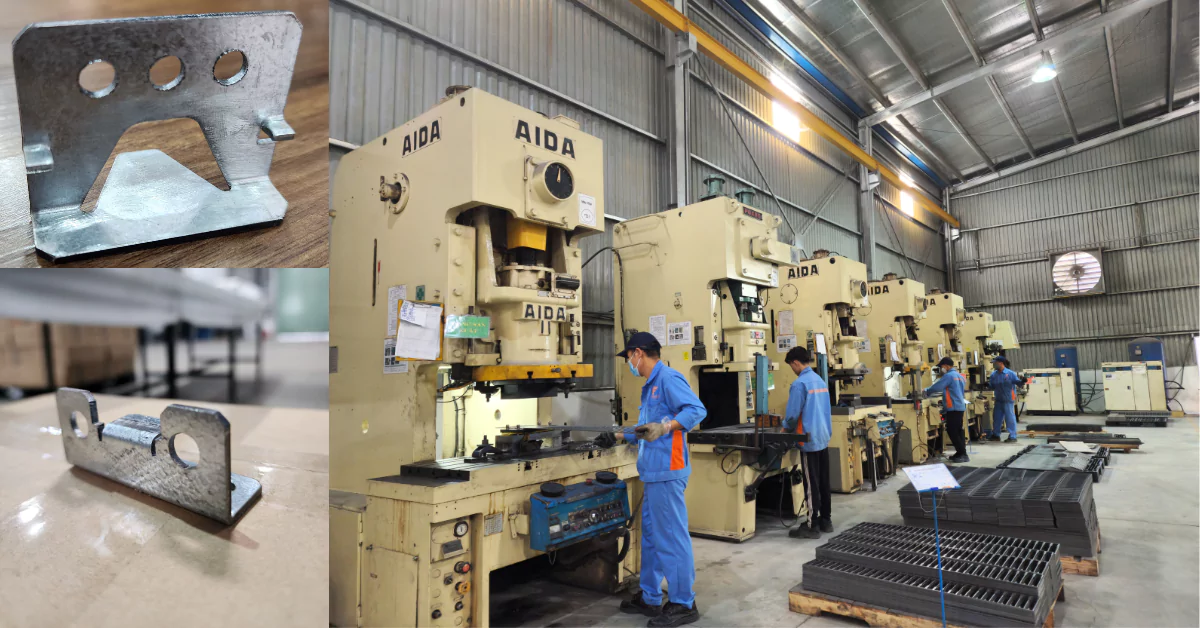
Today, custom sheet metal stamping has become an essential metalworking technique widely used across various industries. It employs mechanical force to transform flat metal sheets into desired shapes, contributing to the creation of intricate and useful metal products for our daily lives.
But what exactly is metal stamping? And who are the reputable and professional metal stamping providers?
This article delves into the world of metal stamping, providing comprehensive details to answer the question “What is metal stamping?” and helping you gain a deeper understanding of this advanced metalworking technique.
At Nhat Nam Mechanical, a leading provider of sheet metal fabrication in Vietnam, we provide a wide range of stamping/forming services with machines and technologies to tailored to your project requirements.
What is metal stamping?
Metal stamping or metal forming, a crucial process in the metalworking industry, utilizes force from machinery to transform flat metal sheets into desired shapes. This versatile technique offers several advantages, including high precision, material efficiency, and rapid production rates.
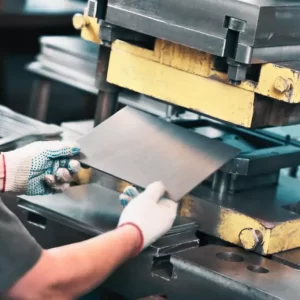
Based on the product’s shape obtained after stamping, metal stamping forming can be categorized into the following primary types:
1. Embossing: Embossing creates raised features on the metal surface.
- Advantages:
- Produces components with high rigidity and strength.
- Facilitates the creation of intricate patterns and logos.
- Minimizes material waste.
- Disadvantages:
- Requires more complex stamping dies.
- Demands higher pressing force compared to other stamping types.
- Prone to metal wrinkling or tearing if pressing force isn’t adjusted properly.
- Application: Metal can lids, soda can bodies, lamp shades, pot bodies.
2. Recessing: Recessing forms indented features on the metal surface.
- Advantages:
- Generates components with high rigidity and strength.
- Enables the creation of parts with complex shapes.
- Reduces material waste.
- Disadvantages:
- Necessitates more intricate stamping dies.
- Requires higher pressing force compared to other stamping types.
- Susceptible to metal wrinkling or tearing if pressing force isn’t adjusted properly.
- Examples: Pot bodies, pans, washing machine tubs, refrigerator housings.
3. Bending: Bending curves the metal at a specific angle. Learn more about bending
- Advantages:
- Produces components with simple curved shapes.
- Straightforward to perform.
- Minimizes material wastage.
- Disadvantages:
- Challenging to create parts with intricate curved shapes.
- Product accuracy depends on metal hardness and bending techniques.
- Examples: Motorcycle frames, brackets, support bars.
4. Trimming: Trimming cuts the metal into desired shapes.
- Advantages:
- Generates flat-shaped components with high precision.
- Easy to perform.
- Minimizes material wastage.
- Disadvantages:
- Demands sharp cutting dies.
- Excessive cutting force can deform the metal.
- Examples: Flat gaskets, washers, rubber seals.
5. Piercing: Piercing creates holes on the metal surface.
- Advantages:
- Produces holes with high precision.
- Simple to perform.
- Minimizes material wastage.
- Disadvantages:
- Requires sharp piercing punches.
- Excessive piercing force can deform the metal around the hole.
- Examples: Ventilation holes on computer cases, screw mounting holes.
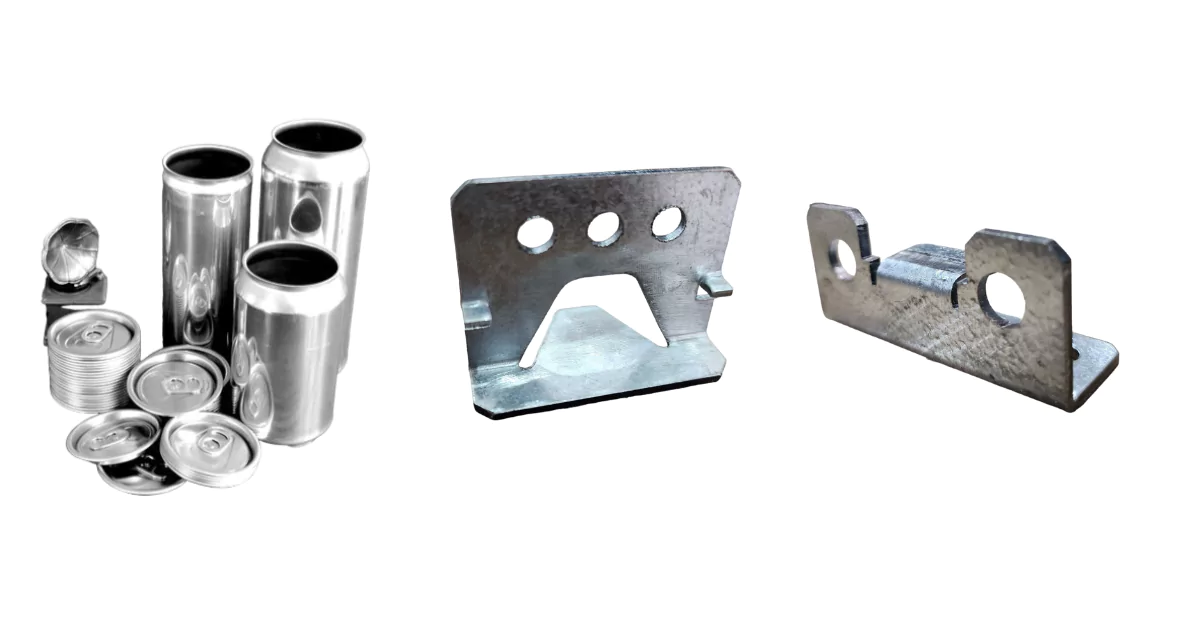
Apart from these primary types, other metal stamping forming techniques exist, including:
- Drawing: Employed to produce components with conical or cylindrical shapes. Examples: Motorcycle engine casings, gas cylinder bodies.
- Rolling: Used to manufacture products with tubular shapes. Examples: Steel pipes, aluminum tubes.
- Hydroforming: Utilizes hydraulic pressure to exert forming force. Advantages: High forming force, creates intricate shapes. Disadvantages: Complex machinery, high cost.
- Mechanical Stamping: Employs electric or internal combustion engines to generate forming force. Advantages: Easy to perform, low cost. Disadvantages: Low forming force, produces simple shapes.
The selection of the appropriate metal stamping type depends on the desired product shape, metal thickness and properties, and machine and equipment capabilities.
Factors Affecting Metal Stamping Forming Techniques
Beyond selecting the suitable metal stamping type, several factors influence the effectiveness of the forming process:
1. Metal Properties:
- Material Strength: Ductile materials like aluminum and brass are more suitable for stamping, while harder materials like steel may require annealing or preheating.
- Sheet Thickness: The metal sheet’s thickness should align with the die’s requirements to prevent excessive thinning or cracking.
- Surface Finish: A clean and smooth surface ensures proper adhesion between the metal and die, minimizing defects.
2. Stamping Die Design:
- Die Material: The die material should be sufficiently hard and durable to withstand the stamping forces.
- Die Geometry: The die’s geometry, including clearances and tolerances, must precisely match the desired product shape.
- Die Surface Treatment: Proper surface treatment, such as lubrication or coating, reduces friction and improves metal flow during stamping.
3. Stamping Machine Parameters:
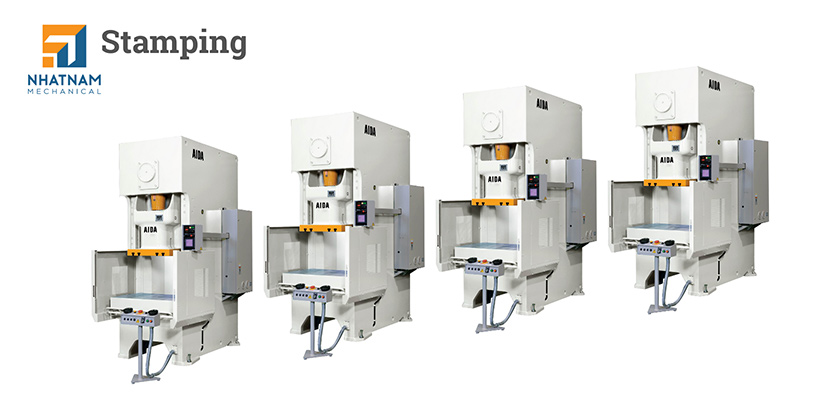
- Pressing Force: The pressing force should be adequate to form the metal without causing excessive deformation or damage.
- Stamping Speed: The stamping speed should be optimized to balance production rate and product quality.
Regarding how Nhat Nam Mechanical’s sheet metal fabrication services can help your project involving galvanized steel, here are some ways:
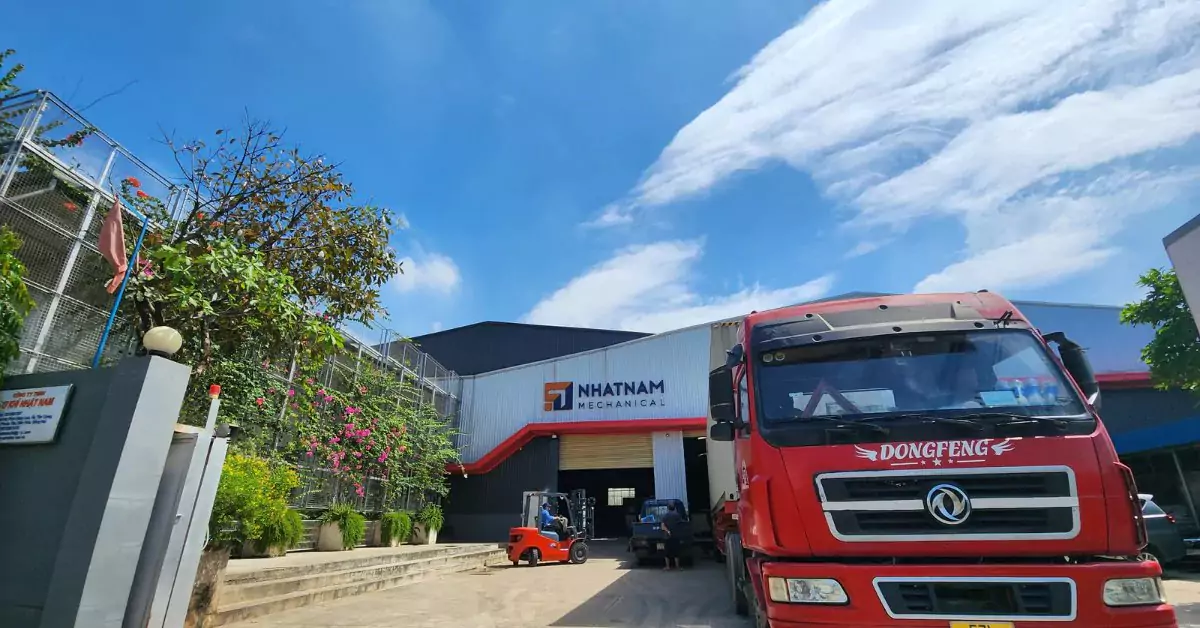
- Custom Fabrication: We can work with galvanized steel sheets to fabricate custom components or structures based on your project requirements. We can cut, bend, and shape the galvanized steel to create the desired shapes and sizes.
- Welding and Joining: If your project requires the joining of galvanized steel pieces, Nhat Nam Mechanical can provide welding services to securely bond the components together. We have expertise in various welding techniques suitable for galvanized steel.
- Finishing and Surface Treatment: We can provide surface treatments for galvanized steel products, such as painting or powder coating. This can enhance the appearance, provide additional protection, or meet specific project requirements.
- Prototyping and Production: Whether you need a one-off prototype or a large production run, Nhat Nam Mechanical can assist with both. We can fabricate galvanized steel components or assemblies in the desired quantities to support your project.
It’s important to discuss your specific project requirements with Nhat Nam Mechanical to determine the extent of our capabilities and how we can best assist you with your galvanized steel fabrication needs.
NHAT NAM MECHANICAL CO., LTD contact information: House No. 36, Garland – Phuoc Dien, 72 Duong Dinh Hoi, Phuoc Long B Ward, District 9, Ho Chi Minh City, Vietnam
Contact Japan
Email: tranquy@cokhinhatnam.vn
Tel: +84 938 771 508
Contact English
Email: sale03@cokhinhatnam.vn
Tel: +84 964 092 079
Contact Vietnam
Email: vinhnt@cokhinhatnam.vn
Tel: +84 964 084 479