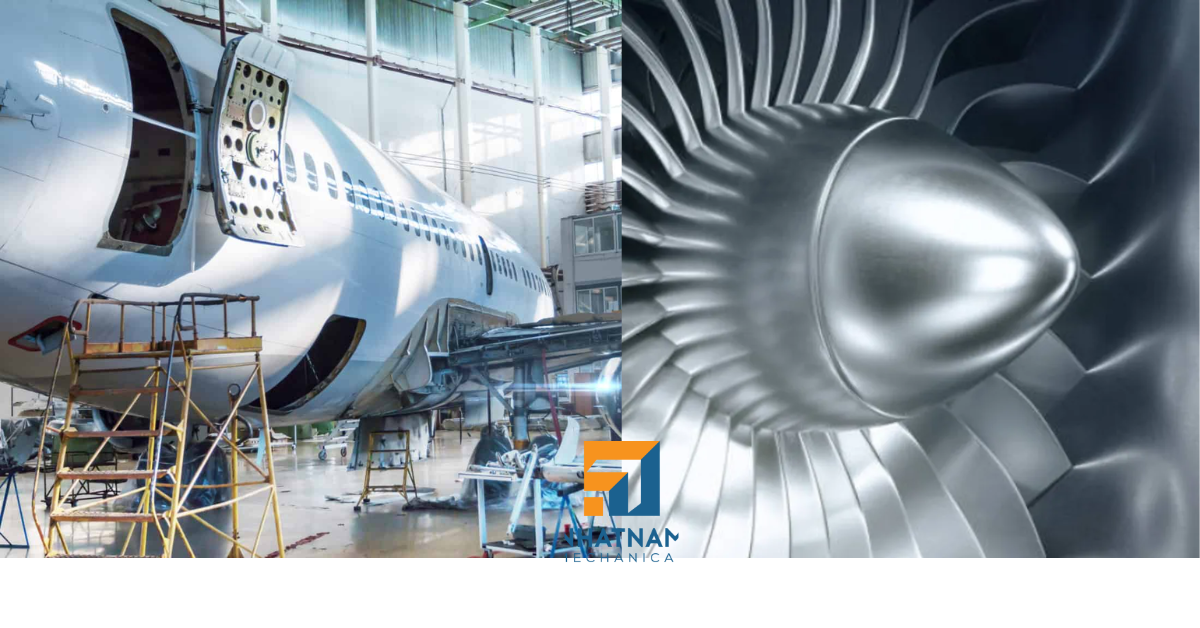
Aluminum sheet metal processing is one of the key technologies in the modern aerospace industry. With its lightweight, durable, highly corrosion-resistant, and easy-to-process properties, aluminum has become an ideal material for many critical parts in aircraft and spacecraft. This article will review the outstanding applications of aluminum sheet metal in the aerospace industry, along with the reasons for its popularity.
1. Why Choose Aluminum in the Aerospace Industry?
Low Weight, High Fuel Efficiency:
Aluminum has a density of only about 2.7 g/cm³—just one-third that of steel. Reducing weight significantly helps save fuel, a vital factor in aviation. Aluminum alloys that combine elements such as zinc, copper, and magnesium (e.g., 2 series and 7 series) can achieve tensile strengths of up to 500–700 MPa, comparable to many types of high-strength steel.High Strength and Corrosion Resistance:
Aluminum naturally forms a thin oxide layer (Al₂O₃) on its surface, which protects it from oxidation and corrosion. This makes it well-suited for environments with constantly changing humidity and pressure, such as aircraft cabins or external surfaces.Excellent Formability and Machinability:
Aluminum is well-suited for stamping, bending, punching, welding, and CNC machining. It can also be heat-treated to increase hardness while retaining good workability—ideal for manufacturing aerodynamic components.Ease of Maintenance and Repair:
In commercial aviation, the ability to quickly maintain and easily replace aluminum components helps minimize aircraft downtime. Most maintenance facilities are equipped with the tools and materials needed for aluminum alloys.High Recyclability:
Aluminum is 100% recyclable without loss of quality. Recycling aluminum saves up to 95% of the energy required to produce primary aluminum, significantly reducing CO₂ emissions and aligning with the sustainable development goals of the modern aviation industry.
2. Popular Aluminum Alloys in Aviation
2 Series (Aluminum–Copper):
- AA2024 (usually T3/T4): Commonly used in fuselage and wing skins due to its fatigue resistance and tensile strength (~470 MPa).
- AA2219, AA2014: Used for structural parts with complex shapes requiring light weight and good impact resistance.
7 Series (Aluminum–Zinc):
- AA7075-T6: Known as a “steel-hard” aluminum alloy, used in heavy load-bearing components such as wing spars and fuselage frames.
- AA7050, AA7055, AA7068, AA7055-T77:
7050: Used for wing panels and thick structural frames (76–152 mm).
7055-T77: Applied to wing spars and wheels—helping reduce weight by up to 635 kg on the Boeing 777.
7068: Currently the strongest aluminum alloy, mainly used in military applications.
6 Series (Aluminum–Magnesium–Silicon): 6061-T6 – Commonly used in light aircraft for fuselages, tubes, and frames due to its good corrosion resistance and ease of processing.
Other Alloys:
- AA5052, AA6063: Suitable for fuel tanks and components that do not bear heavy loads or require complex shaping.
- Al-Li (Aluminum–Lithium): A newer lightweight alloy under research, offering excellent fatigue resistance.
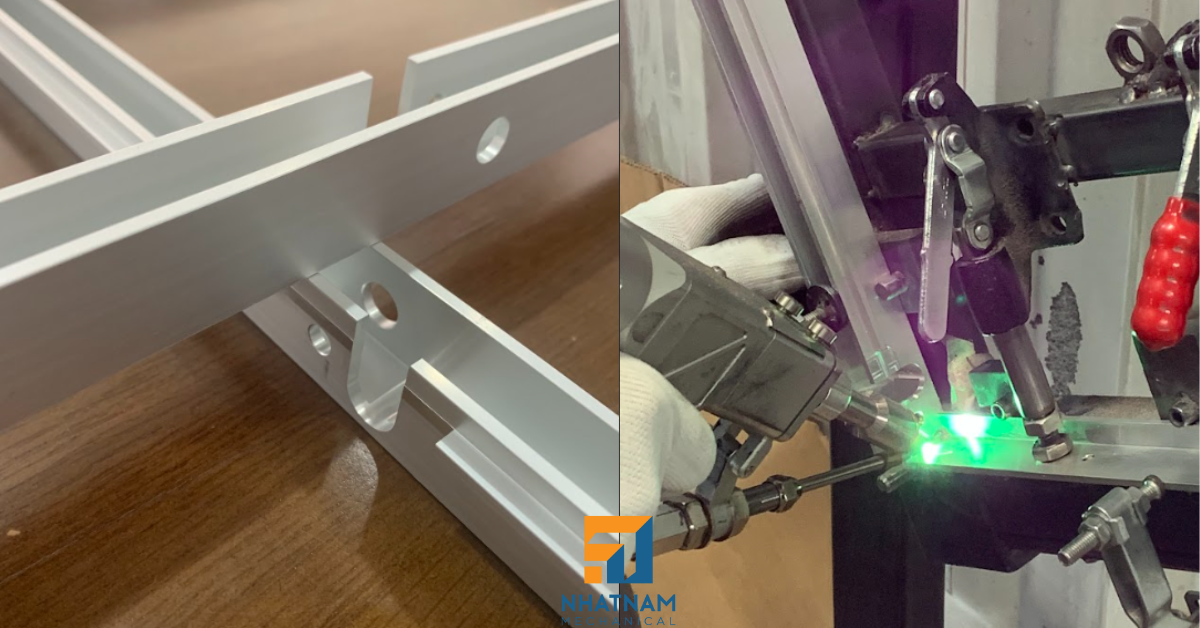
3. Practical Applications in the Aerospace Industry
Aircraft Fuselage and Wings
Aluminum sheets are machined to form the outer skin of the fuselage, wings, doors, and aerodynamic components. Alloys such as 7075 and 2024 are commonly used due to their high strength and light weight.Internal Structure
Structural components such as skeletons, braces, brackets, and various frame parts are made from aluminum sheets to ensure mechanical strength while optimizing overall weight.Spacecraft Applications
In the aerospace industry, aluminum is used for heat shields, rocket skins, reflectors, and equipment frames. These components require high precision and excellent heat resistance.Cooling and Heat Dissipation Systems
Due to its excellent thermal conductivity, aluminum is widely used in pipes, radiators, and heat-spreading plates in the thermal control systems of aircraft.Electronics and Control Components
The enclosures of aircraft electronic systems (e.g., black boxes, radars, sensors) are often made from aluminum to protect internal components from vibration, temperature fluctuations, and harsh environmental conditions.
4. Conclusion
Aluminum sheet metal processing not only plays a supporting role but is also a core factor in optimizing flight performance, reducing weight, and increasing the durability of aerospace equipment. With advancements in laser cutting, CNC punching, and automatic welding technologies, aluminum components are now manufactured with higher precision, meeting the stringent standards of the aerospace industry.
At Nhat Nam Mechanical, we specialize in high-precision aluminum sheet metal processing services tailored to various industrial and civil requirements. With a team of experienced technicians and a modern machinery system—including fiber laser cutting machines, CNC punching machines, and MIG/TIG welding machines specialized for aluminum—Nhat Nam is committed to delivering products with exceptional sophistication and quality.
If you are looking for a professional and reliable aluminum processing partner in Vietnam, Nhat Nam Mechanical is your top choice to bring your products to life—accurately, quickly, and efficiently.
NHAT NAM MECHANICAL CO., LTD contact information: House No. 36, Garland – Phuoc Dien, 72 Duong Dinh Hoi, Phuoc Long B Ward, District 9, Ho Chi Minh City, Vietnam.
Contact Japan
Email: tranquy@cokhinhatnam.vn
Tel: +84 938 771 508
Contact English
Email: marketing@cokhinhatnam.vn
Tel: +84 964 092 079
Contact Vietnam
Email: vinhnt@cokhinhatnam.vn
Tel: +84 964 084 479