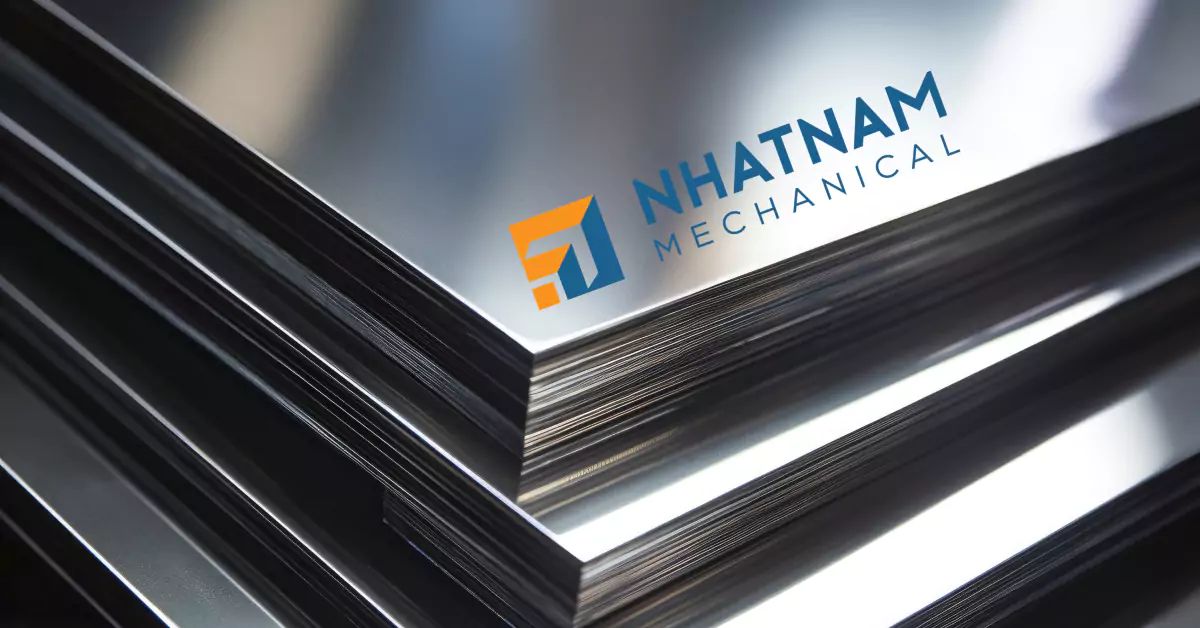
Sheet metal fabrication is a crucial process across multiple industries, from automotive to aerospace, and even architecture. The techniques used in sheet metal fabrication not only affect the quality and precision of the final products but also impact production efficiency and costs. In this article, we will delve deeper into the top 10 sheet metal fabrication techniques that are essential for professionals and enthusiasts alike.
1. Cutting
Cutting is the foundational technique in sheet metal fabrication. Various methods are employed to achieve the desired shapes and sizes, including:
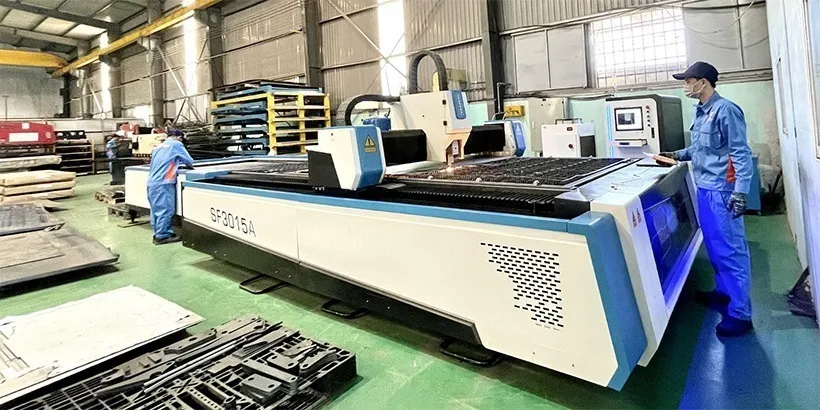
- Laser Cutting: This method uses a focused beam of light to cut through metal with exceptional precision. Laser cutting is ideal for intricate designs and allows for minimal material wastage. It’s commonly used for applications requiring high detail, such as decorative panels and custom parts.
- Plasma Cutting: Plasma cutting utilizes an ionized gas to cut through conductive metals. It’s particularly effective for thicker sheets and is known for its speed and versatility. Industries often rely on plasma cutting for projects involving steel and aluminum.
- Shearing: This method involves using a straight blade to cut through the metal sheet. Shearing is efficient for producing straight cuts and is best suited for sheets of uniform thickness.
2. Bending
Bending reshapes metal sheets to form angles and curves, crucial for creating parts like brackets and frames. The primary methods include:
- Air Bending: In this technique, the metal is bent using a punch and die, allowing for a variety of angles and depths. It’s versatile and can handle different materials and thicknesses.
- Bottom Bending: This process offers greater precision, as the material is pressed against the die, resulting in consistent angles and reduced springback.
- Coining: Coining is a precise bending technique that involves forcing the material into the die, ensuring tight tolerances. It’s ideal for parts that require a high degree of accuracy.
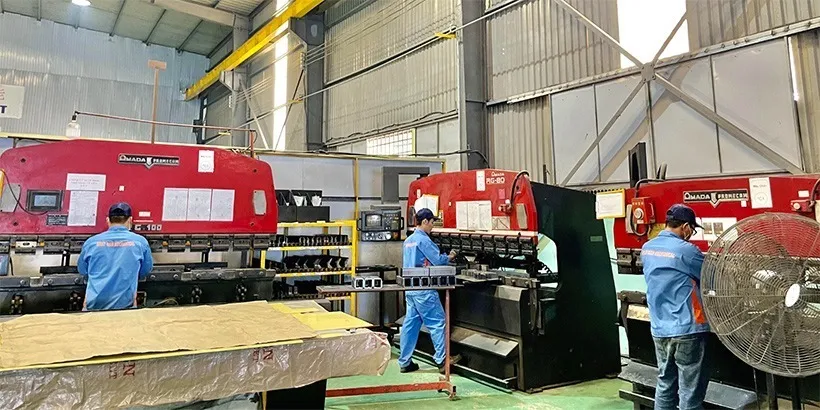
3. Forming
Forming techniques manipulate the metal into desired shapes without cutting away material. Key methods include:
- Stamping: Stamping is often used to create complex shapes and is highly efficient for mass production. This technique can produce detailed patterns and is frequently used in automotive components.
- Stretch Forming: This method stretches the metal sheet over a mold, allowing for gentle curves and complex shapes. Stretch forming is commonly used in aerospace applications where aerodynamic shapes are necessary.
4. Welding
Welding is vital for joining metal components and ensuring structural integrity. The most common welding techniques include:
- MIG Welding (Metal Inert Gas): This technique uses a continuous wire feed and inert gas to shield the weld area, making it ideal for thin materials and fast production.
- TIG Welding (Tungsten Inert Gas): Known for its precision, TIG welding is suitable for thinner metals and provides high-quality welds. It’s often used in applications where aesthetics and strength are critical.
- Spot Welding: Frequently used in automotive manufacturing, spot welding involves joining overlapping metal sheets at specific points, creating a strong bond.
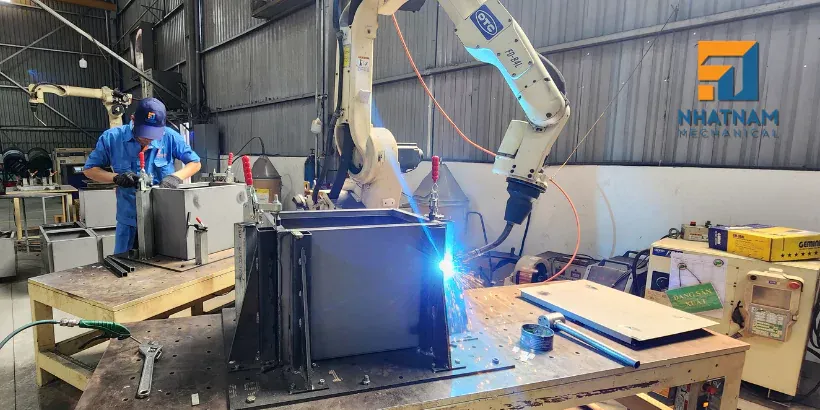
5. Punching
Punching is a technique used to create holes or shapes in metal sheets. It involves using a punch press to drive a punch through the material. This method is vital for applications such as:
- Ventilation Systems: Punching creates holes for air passage in ducts and vents.
- Assembly Parts: Holes produced through punching are often used for fastening components together.
6. Laser Cutting
As previously mentioned, laser cutting stands out for its precision and ability to handle complex designs. Key benefits include:
- Minimal Material Waste: The narrow kerf produced during laser cutting results in less scrap material.
- Versatility: Laser cutting can be applied to various materials, including stainless steel, aluminum, and even non-metals like wood and acrylic.
7. Plasma Cutting
Plasma cutting is known for its speed and effectiveness in handling thicker materials. Key aspects include:
- Cost-Effectiveness: Plasma cutting equipment is generally less expensive than laser cutting systems, making it accessible for many businesses.
- Wide Application Range: It can be used on various metals, making it a flexible choice for different projects.
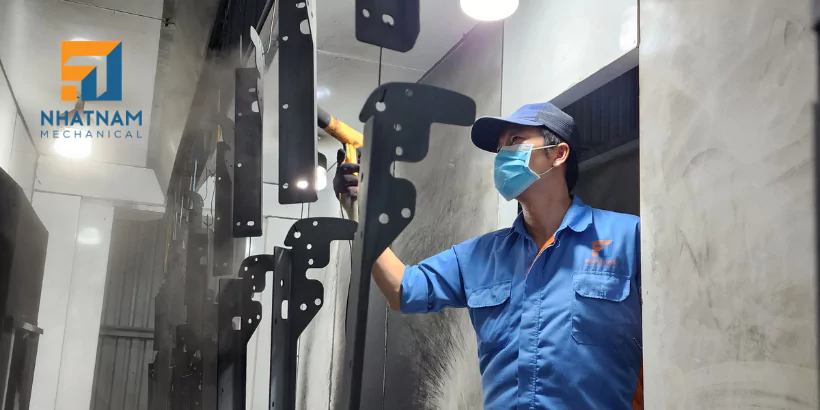
8. Finishing
Finishing techniques enhance the appearance and durability of metal products. Common methods include:
- Powder Coating: This process involves applying a dry powder that is cured under heat, providing a durable finish that resists chipping and fading.
- Anodizing: Particularly for aluminum, anodizing increases corrosion resistance and allows for a range of color options, enhancing aesthetic appeal.
9. Assembly
Once individual components are fabricated, assembly techniques come into play to create the final product. Common assembly methods include:
- Riveting: A mechanical fastening technique that involves inserting a rivet into a pre-drilled hole, providing strong connections in various applications.
- Bolting: A reliable method for joining parts that may require disassembly in the future. It’s commonly used in structural applications.
- Welding (again): As discussed, welding is often the preferred method for permanent assembly, especially in heavy-duty applications.
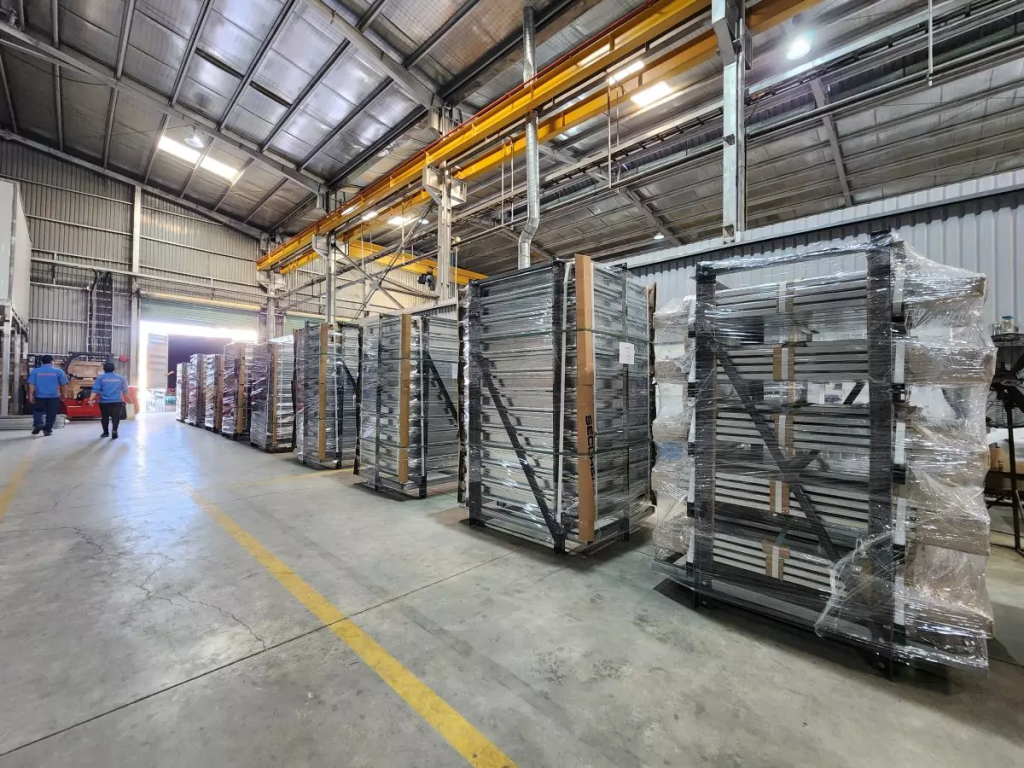
10. Quality Control
Ensuring the final product meets specifications is vital in fabrication. Quality control methods include:
- Inspection: Visual inspections and measurements help identify defects early in the process.
- Testing: Non-destructive testing methods, such as ultrasonic and X-ray testing, ensure that the welded joints and overall integrity meet industry standards.
Conclusion
Mastering these top 10 sheet metal fabrication techniques is essential for professionals looking to enhance their production processes. By understanding the nuances of each technique, you can make informed decisions that lead to improved efficiency, reduced costs, and superior quality in your projects.
Ready to elevate your sheet metal fabrication skills? Explore our resources or contact us for expert guidance and support tailored to your specific needs. Whether you’re a beginner or a seasoned professional, we’re here to help you succeed in your fabrication endeavors!
At Nhat Nam Mechanical, we are dedicated to helping you elevate your projects with our expertise and commitment to excellence. If you’re looking to enhance your operations and ensure high-quality results, don’t hesitate to reach out to us. Let’s work together to turn your vision into reality!
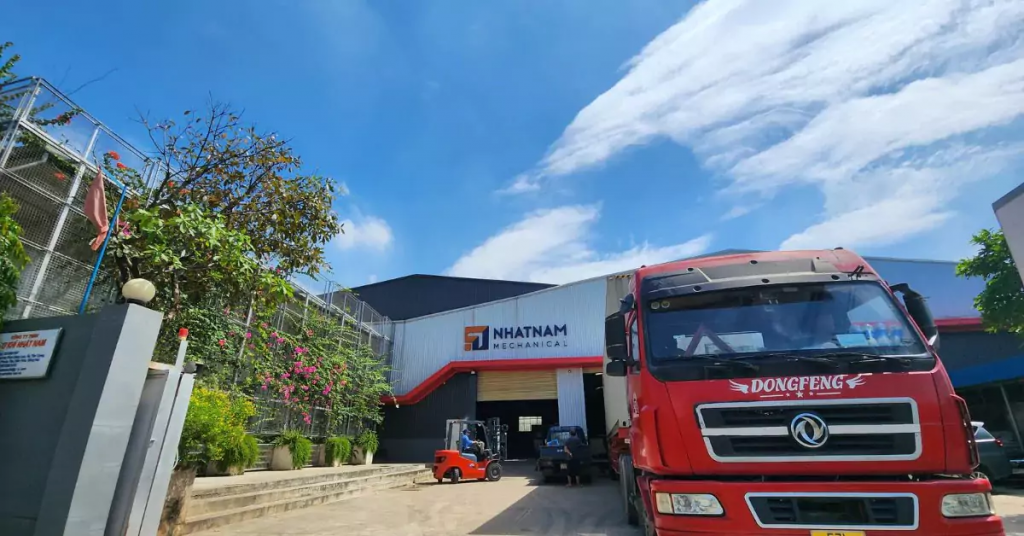
Contact us today to discover how we can support your business needs!
NHAT NAM MECHANICAL CO., LTD contact information:
House No. 36, Garland – Phuoc Dien, 72 Duong Dinh Hoi, Phuoc Long B Ward, District 9, Ho Chi Minh City, Vietnam
Contact Japan
Email: tranquy@cokhinhatnam.vn
Tel: +84 938 771 508
Contact English
Email: marketing@cokhinhatnam.vn
Tel: +84 964 092 079
Contact Vietnam
Email: vinhnt@cokhinhatnam.vn
Tel: +84 964 084 479
Please read more articles: Sheet metal fabrication process