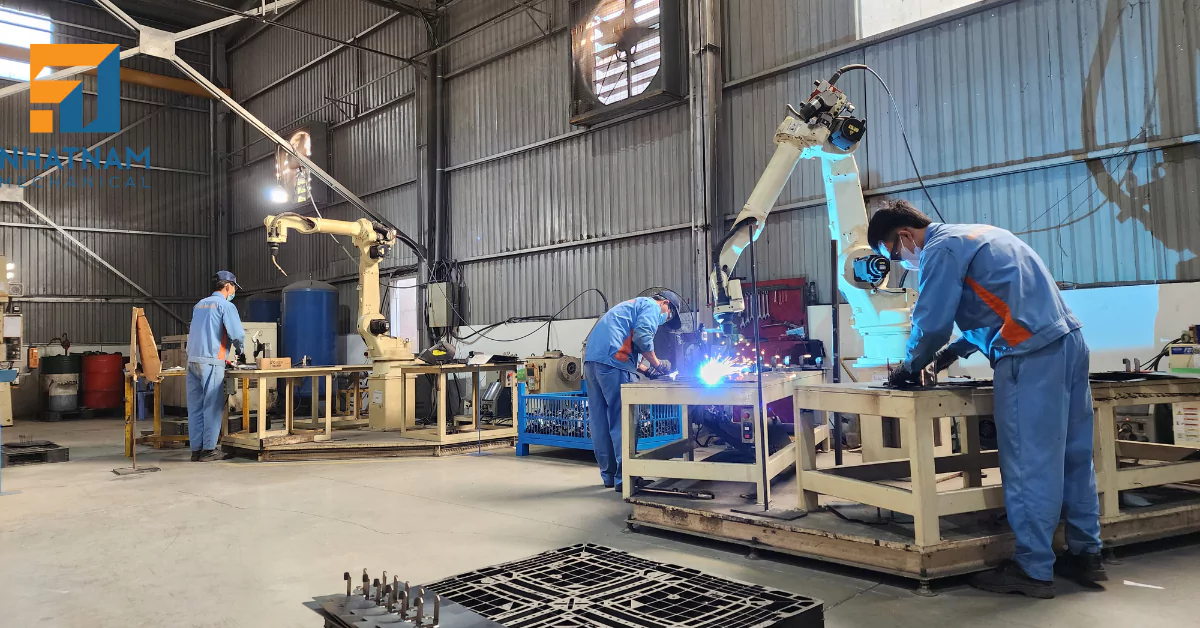
Metal fabrication plays an important role in many industries, from automotive manufacturing to construction and machinery production. Welding services are indispensable in this field to create durable and precise structures. A high-quality welding service not only ensures durability and precision but also saves costs and time. So, what makes a high-quality welding service? Let’s explore the advanced standards and techniques in this industry.
1. Metal Fabrication and Compliance with International Welding Standards
One of the most important factors in ensuring the quality of welding services is compliance with international welding standards. These standards, such as ISO 3834 (Quality Standard for Metal Welding) and AWS D1.1 (American Welding Society Standard for Welding of Steel Structures), help ensure that welds are performed correctly, are durable, and are safe.
These standards cover everything from material selection and weld quality testing to detailed welding procedures. A high-quality welding service provider will always adhere to these standards to ensure that the final product meets the strict requirements for durability and stability, especially in the metal fabrication industry.
2. Metal Fabrication and Advanced Welding Techniques
While traditional welding methods such as manual metal arc welding (MMA) or gas welding (TIG, MIG) are still widely used, advanced welding techniques are becoming increasingly popular due to their ability to improve quality and efficiency.
- Automated and Robotic Welding: Automated welding technologies use robots and automated machines to perform the welding process. This minimizes human errors, ensuring even welds and consistent quality across all products. Robotic welding also helps increase productivity and reduce production time, especially in large-scale metal fabrication projects.
- Laser Welding: This modern welding technology uses laser beams to create precise and durable welds. Laser welding is particularly effective for thin materials and requires sophisticated welds, especially in industries like electronics and automotive.
- Plasma Welding: Plasma welding technology allows for extremely high-temperature welds and precise welding capabilities, making it ideal for thick metal welding applications in the metal fabrication industry.
3. Inspection and Quality Control of Welds in Metal Fabrication
A high-quality welding service cannot be without strict quality control steps. Weld inspection is necessary to detect errors such as cracks, defects, or durability-related problems. Common testing methods include:
- Non-destructive Testing (NDT): Techniques such as ultrasonic testing, X-ray testing, or magnetic particle testing are used to examine welds without damaging the product. These methods help detect defects that are not visible to the naked eye.
- Mechanical Testing: Measures like tensile strength, hardness, and other mechanical properties of welds are used to ensure they meet technical and safety requirements.
4. Metal Fabrication and Selecting the Right Materials
The materials used in welding are a decisive factor in the quality of the weld. Choosing the right material not only affects strength but also the stability of the weld under temperature, pressure, and environmental stress. Common materials used in welding include steel, stainless steel, aluminum, and special alloys.
A high-quality welding service will always choose the right materials to meet the technical requirements of each project, ensuring that the weld has good load-bearing capacity and corrosion resistance. Especially in metal fabrication, selecting the right material helps increase the efficiency and durability of the product after fabrication.
5. Welder Experience and Skills
Finally, the welder’s experience and skills are essential to ensure the quality of the welding service. Experienced welders understand factors such as welding temperature, welding speed, and how to adjust welding parameters to produce optimal quality welds. Welders must also be trained and certified according to international standards to ensure their ability to work with advanced welding technologies.
A high-quality welding service relies not only on modern equipment but also on adherence to strict standard practices, the application of advanced techniques, rigorous quality control, and skilled welders. When all of these elements come together, the result is welds that are strong, precise, and meet the demanding requirements of the industry, especially in metal fabrication.
Nhat Nam Mechanical provides high-quality welding services, specializing in performing metal welding jobs with outstanding precision and durability. We use modern welding technologies such as TIG, MIG, and robotic welding to ensure products meet the highest technical standards. Our team of highly skilled welders is committed to providing efficient welding solutions, saving customers time and costs.
NHAT NAM MECHANICAL CO., LTD contact information: House No. 36, Garland – Phuoc Dien, 72 Duong Dinh Hoi, Phuoc Long B Ward, District 9, Ho Chi Minh City, Vietnam
Contact Japan
Email: tranquy@cokhinhatnam.vn
Tel: +84 938 771 508
Contact English
Email: marketing@cokhinhatnam.vn
Tel: +84 964 092 079
Contact Viet Nam
Email: vinhnt@cokhinhatnam.vn
Tel: +84 964 084 479