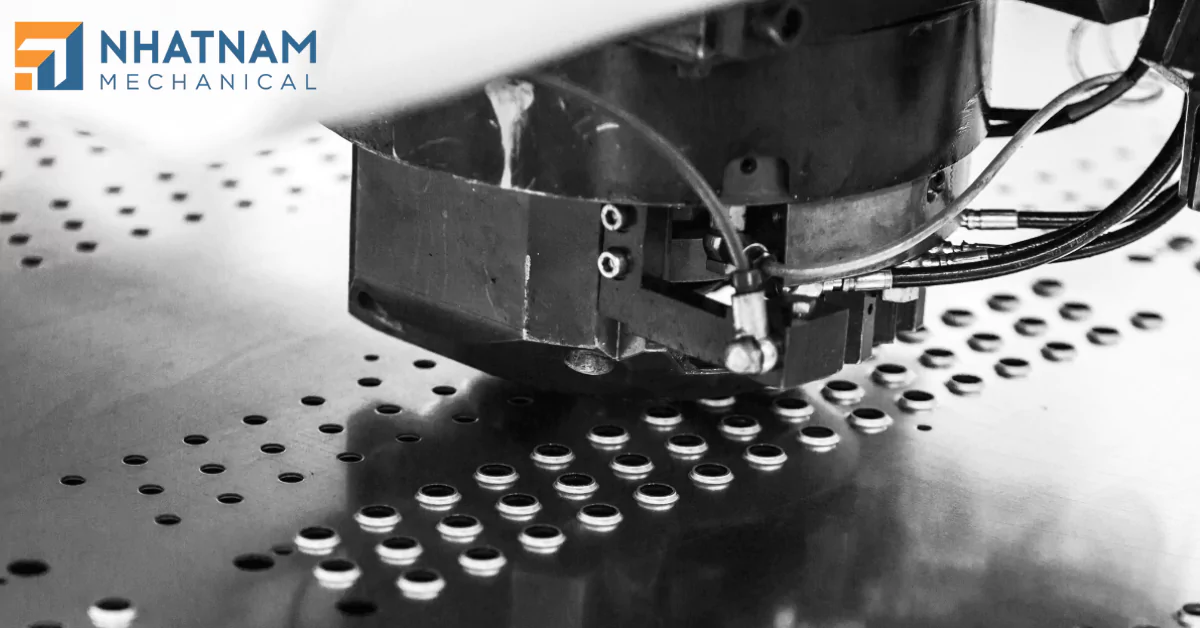
In sheet metal processing, the punching process plays an important role in creating holes, slots, or special shapes on metal materials. Although it is a classic processing method, punching still maintains an important position in industrial production thanks to its fast speed, high precision, and cost-saving ability, especially in mass production lines. The punching process uses a tool called a punch to apply force through the metal sheet, causing the material to be removed in the designed shape. This helps create holes or cut patterns with fixed sizes and shapes. In this article, we will learn in detail about the punching process, the types of holes that can be created, the advantages and limitations of this method, as well as compare it with other cutting technologies such as laser cutting and plasma cutting.
1. Basic Concepts of Punching
Punching is a mechanical process that involves the use of a tool known as a punch, which applies a significant force through a metal sheet, pushing the material into a die located beneath it. This force causes the metal to be displaced, creating holes, slots, or custom shapes with high precision and consistency. The material that is removed during the process is referred to as a chip or slug, which typically falls away or is extracted once the punching operation is completed.
This process is classified as a cold working technique, which means that the metal is not subjected to any heat before being processed. As a result, the material remains at room temperature, allowing for the preservation of its original properties. Cold working generally leads to a high degree of accuracy and surface finish, making punching an ideal method for producing a wide range of parts, from simple holes to more intricate shapes, all with minimal material waste.
2. Structure of a Punching System
To perform the punching process, the following main components are required:
Punch
A cylindrical or specially shaped tool that presses down to penetrate the material. It is made from high-strength alloy steel and can be changed depending on the desired hole shape.
Die
Located beneath the metal sheet, the die has a shape corresponding to the punch. It helps position the hole and supports the material as the punch penetrates.
Punch Press
A device that applies force to the punch. It can be:
Mechanical press (eccentric) – uses a rotating mechanism to generate pressure
Hydraulic press – uses oil pressure to drive the punch
CNC punching machine – automatically controls the punch based on CAD/CAM drawings
3. How Does the Punching Process Work?
The punching process typically includes the following steps:
- Prepare the metal sheet (pre-cut to size)
- Position and clamp the sheet onto the machine table
- The punch moves down, penetrating the metal sheet into the die
- The chips fall away or are collected for disposal
- The machine moves to the next position and repeats the process
In modern factories, this process is fully automated and can punch hundreds to thousands of times per minute.
4. Types of Holes Created by Punching
Round holes – the most common type (used for screws, bolts)
Square and rectangular holes – often used for frames or ventilation
Oval (elliptical) holes – used to reduce stress or allow for movement
Custom shapes (e.g. stars, logos) – require specially designed punch and die sets
5. Advantages of the Punching Process
- Extremely fast processing speed – ideal for mass production
- High precision – consistently accurate hole placement
- Low production cost when dies are reused over many products
- Suitable for thin to medium-thickness sheets (0.5 – 6 mm)
- Easily integrated into automated or robotic production lines
6. Limitations to Consider
- High initial cost for punch and die sets, especially for complex designs
- Not suitable for free-form shapes or soft curves (laser cutting is more appropriate)
- May produce burrs (sharp edges) – often requires post-processing (e.g., deburring)
- Limited design flexibility – constrained by punch and die shapes
7. Comparison Between Punching and Other Methods
Criteria | Punching | Laser Cutting | Plasma Cutting |
---|---|---|---|
Speed | Fastest | Slower | Average |
Investment Cost | Moderate | High | Low to Moderate |
Shape Flexibility | Limited | Very Flexible | Less Flexible |
Suitable Material Thickness | Thin – Medium | Thin – Thick | Medium – Thick |
Automation Compatibility | High | High | Moderate |
8. Practical Applications of Punching
Punching is widely used in industries such as:
Automotive – punching car frames, brackets, engine mounts
Electronics & Appliances – holes in control boxes, PCB holders
Construction – drainage panels, metal framing
Metal Furniture – lockers, shelves, modular steel tables
Home Appliances – washing machine bodies, vacuum casings, air conditioner panels
9. When to Choose Punching?
You should choose punching when:
The product requires simple, repetitive hole patterns
You are producing in high volumes and need to reduce cost per unit
The metal sheets have moderate thickness
Complex or free-form cutting is not required
10. Conclusion
Punching is an optimal solution in sheet metal processing when the goal is to create fast, accurate, and cost-effective holes. Although it has limitations in terms of geometric flexibility compared to laser cutting, it remains the top choice for high-output production with consistent hole shapes.
If you’re a manufacturer of furniture, electrical enclosures, construction hardware, or steel frames – investing in punching technology can significantly reduce production time and improve operational efficiency.
Nhat Nam Mechanical is a leading manufacturer and processor of steel components in Vietnam. With many years of experience in the industry, we specialize in providing high-quality mechanical solutions for industries such as automotive, electronics, construction, and interiors. Nhat Nam Mechanical focuses on applying modern technology and precise production processes, ensuring that we meet all of our customers’ strict requirements for quality and delivery time. We are committed to delivering sheet metal products and mechanical components that are machined with precision, helping to optimize the production process and improve work efficiency.
NHAT NAM MECHANICAL CO., LTD contact information: House No. 36, Garland – Phuoc Dien, 72 Duong Dinh Hoi, Phuoc Long B Ward, District 9, Ho Chi Minh City, Vietnam.
Contact Japan
Email: tranquy@cokhinhatnam.vn
Tel: +84 938 771 508
Contact English
Email: marketing@cokhinhatnam.vn
Tel: +84 964 092 079
Contact Vietnam
Email: vinhnt@cokhinhatnam.vn
Tel: +84 964 084 479