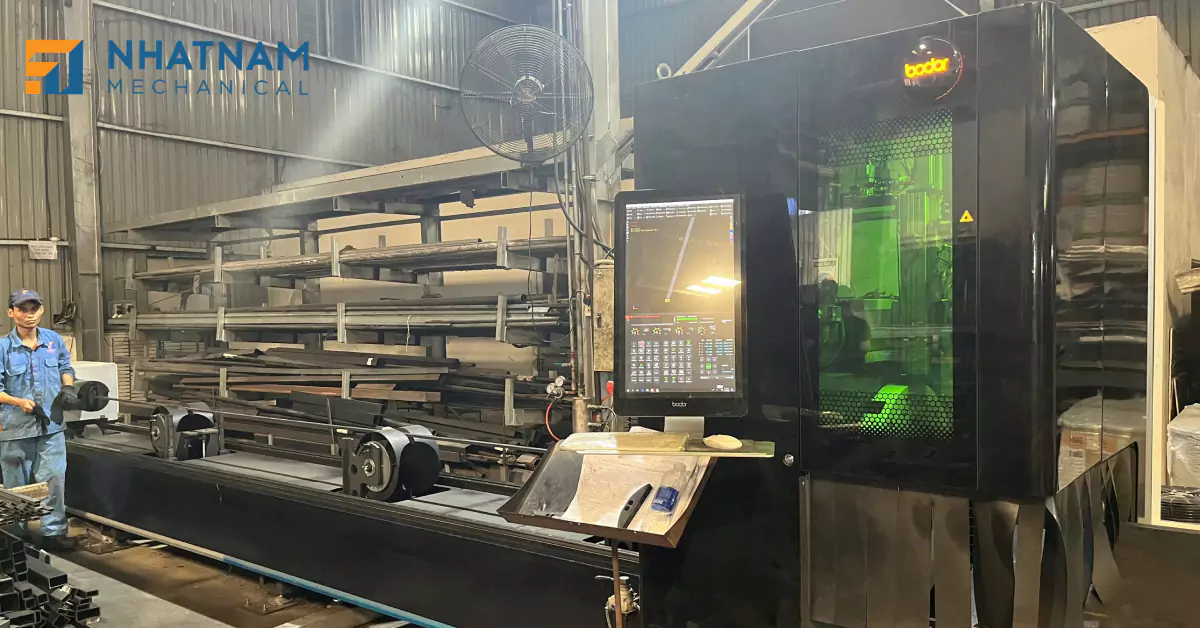
When it comes to metal fabrication, laser cutting is a revolutionary alternative to traditional cutting techniques such as sawing, milling, and mechanical cutting. In this article, we will explore the differences, advantages, and challenges of tube laser cutting compared to traditional cutting methods.
What is Traditional Cutting Methods?
Traditional cutting methods are mechanical or manual processes that have been around for decades and include techniques such as:
Saw cutting
Saw cutting uses a jigsaw, circular saw, or hacksaw to cut metal tubing. This is a cost-effective and simple process for simple cuts, but lacks the precision and speed for more complex projects.
Milling
Milling involves using a rotating cutter to remove material. This method is often used for slotting, grooving, or creating custom shapes, but can be time-consuming and inefficient for mass production.
Plasma cutting
Plasma cutting uses a jet of ionized gas to melt and cut metal. While faster than saw cutting, plasma cutting can be difficult to achieve with accuracy, especially for thin-walled tubing.
Hand Cutting
Hand cutting using tools such as grinders or torch cutters is the most basic method. This method requires highly skilled labor and has significant limitations in terms of accuracy, consistency, and speed.
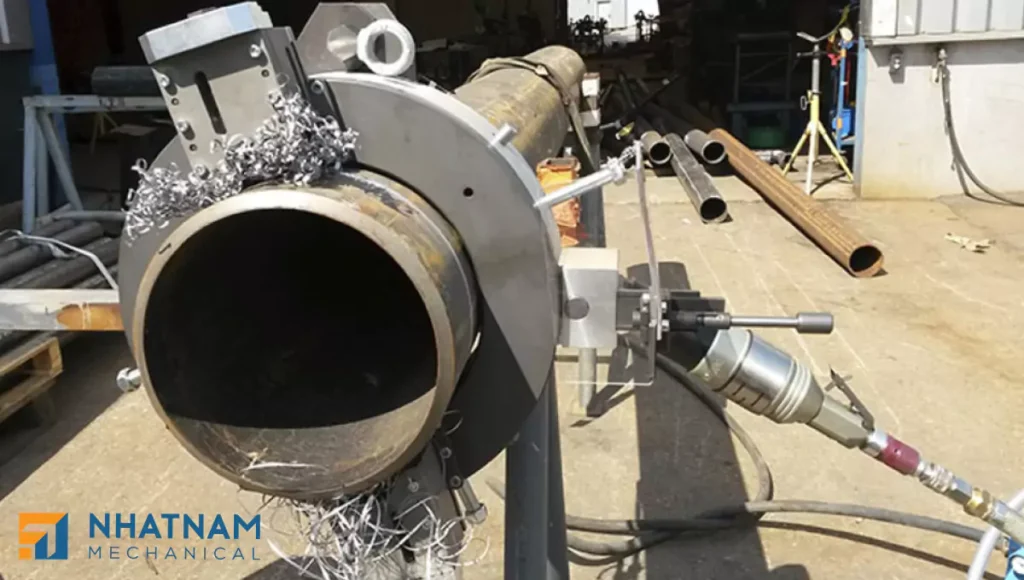
What is Tube Laser Cutting?
Tube laser cutting is a high-precision, computer-controlled process that uses a concentrated laser beam to cut through metal tubes and profiles. Unlike traditional cutting methods, which rely on physical tools like saws or blades, tube laser cutting uses thermal energy to melt or vaporize the material along a specified path.
The process is controlled by CNC (Computer Numerical Control) machines, which ensure extreme accuracy and repeatability. The laser’s intensity, speed, and focus can be adjusted to suit the type of material, thickness, and design complexity.
How Does Tube Laser Cutting Work?
Laser Beam Generation: A powerful laser beam is generated through an optical resonator.
Focus and Direction: The beam is directed and focused onto the metal tube using lenses or mirrors.
Material Removal: The intense heat melts, burns, or vaporizes the material in the cutting area.
Assist Gas: A gas such as oxygen, nitrogen, or compressed air is used to blow away molten material and ensure a clean cut.
Movement and Control: The CNC system guides the laser along precise paths, creating cuts with minimal error.
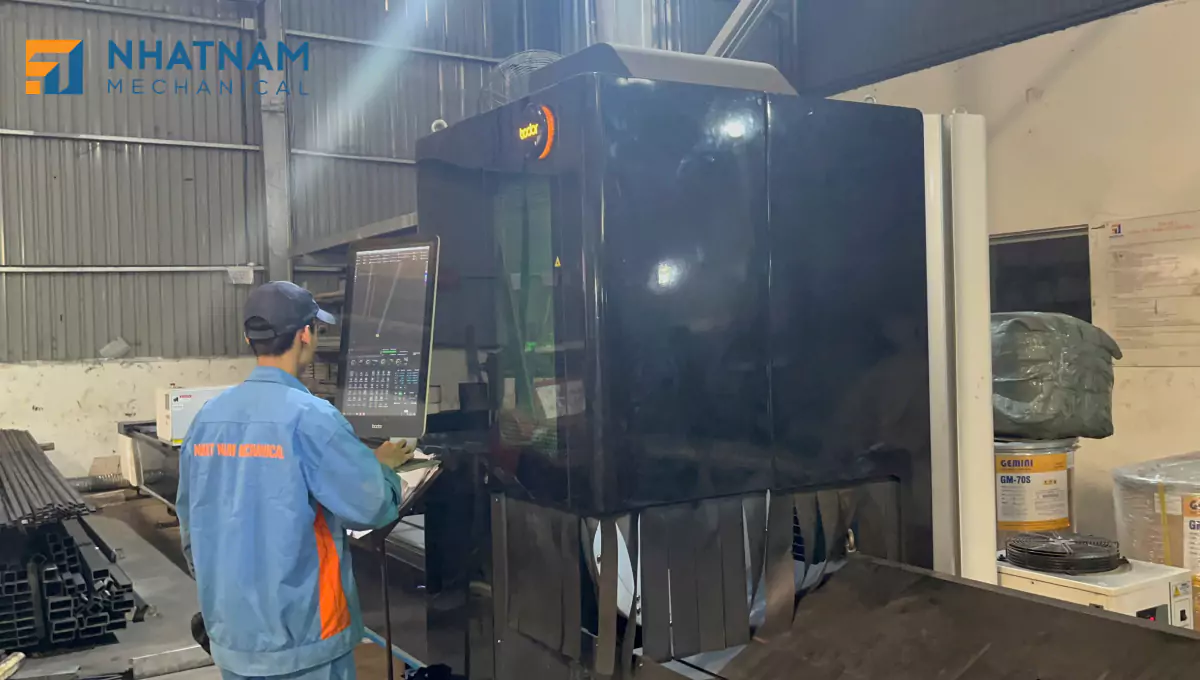
Differences Between Tube Laser Cutting and Traditional Cutting
Tube Laser Cutting | Traditional Cutting | |
Speed and Efficiency | Cuts faster than any traditional method. Complex cuts, holes, and patterns can be completed in a single pass without secondary operations | Slower, especially for complex geometries. Secondary operations like drilling or deburring are often required, adding time and cost |
Flexibility and Design Capability | Supports intricate designs, irregular shapes, and detailed patterns. It’s ideal for prototyping and custom fabrications. | Limited to basic cuts and simple designs. Creating complex shapes requires multiple tools and additional processes. |
Cost-Effectiveness | Higher initial setup costs but lower long-term costs due to reduced labor, material waste, and faster production times. | Lower upfront costs but higher operational costs due to slower speed, labor dependency, and material waste. |
Material Waste | Produces minimal waste thanks to precise cuts and efficient use of material. | Creates more waste due to inaccuracies and the need for secondary operations. |
Maintenance and Downtime | CNC machines require regular maintenance but experience less downtime overall. | Tools wear out faster, leading to frequent replacements and downtime. |
Which One Should You Choose?
The choice between tube laser cutting and traditional cutting ultimately depends on your specific needs:
- Choose Tube Laser Cutting If:
- You need high precision and clean cuts.
- You’re working with complex designs.
- Speed and efficiency are priorities.
- You want to reduce material waste and long-term costs.
- Choose Traditional Cutting If:
- You have simple, low-volume projects.
- Budget constraints are significant.
- Precision and speed are not major concerns.

Conclusion
While traditional cutting methods still have a place in the manufacturing world, tube laser cutting has proven to be superior in almost every aspect. Its precision, speed, flexibility, and long-term cost savings make it the ideal choice for modern fabrication needs.
If you’re looking to take your projects to the next level, consider investing in tube laser cutting services. It’s not just about cutting metal—it’s about cutting time, costs, and inefficiencies.
And at Nhat Nam Mechanical, we are proud to be the leading unit in the mechanical processing industry. Nhat Nam has full equipment, modern machinery and a team of experienced people. With the motto Japanese Technology – Vietnamese Hands, Nhat Nam hopes to bring you the best processed products.
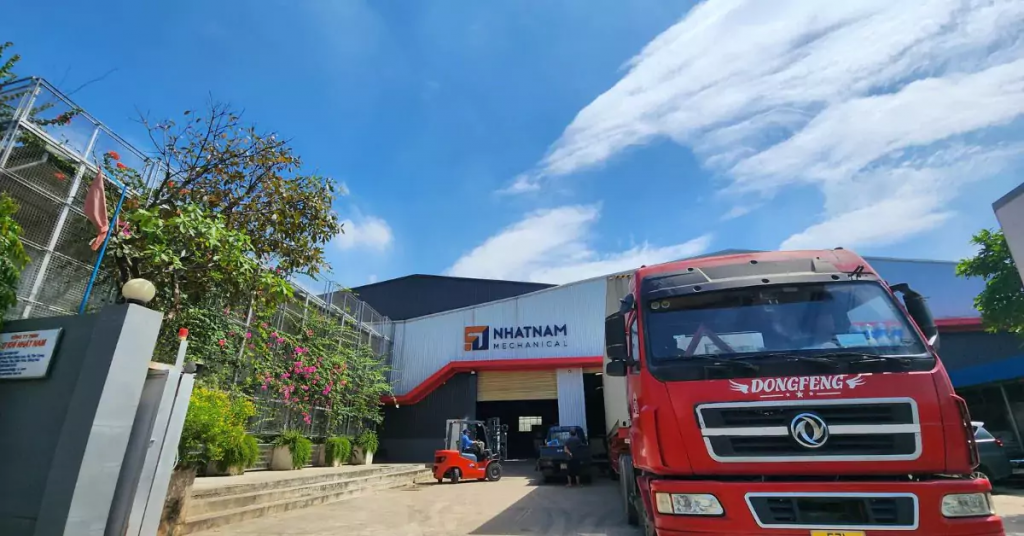
Contact Us
Ready to elevate your projects with high-quality custom steel components? Contact Nhat Nam Mechanical today to discuss your requirements and get a quote. Our dedicated team is here to provide you with exceptional service and solutions that meet your needs.
NHAT NAM MECHANICAL CO., LTD contact information: House No. 36, Garland – Phuoc Dien, 72 Duong Dinh Hoi, Phuoc Long B Ward, District 9, Ho Chi Minh City, Vietnam
Contact Japan
Email: tranquy@cokhinhatnam.vn
Tel: +84 938 771 508
Contact English
Email: marketing@cokhinhatnam.vn
Tel: +84 964 092 079
Contact Vietnam
Email: vinhnt@cokhinhatnam.vn
Tel: +84 964 084 479