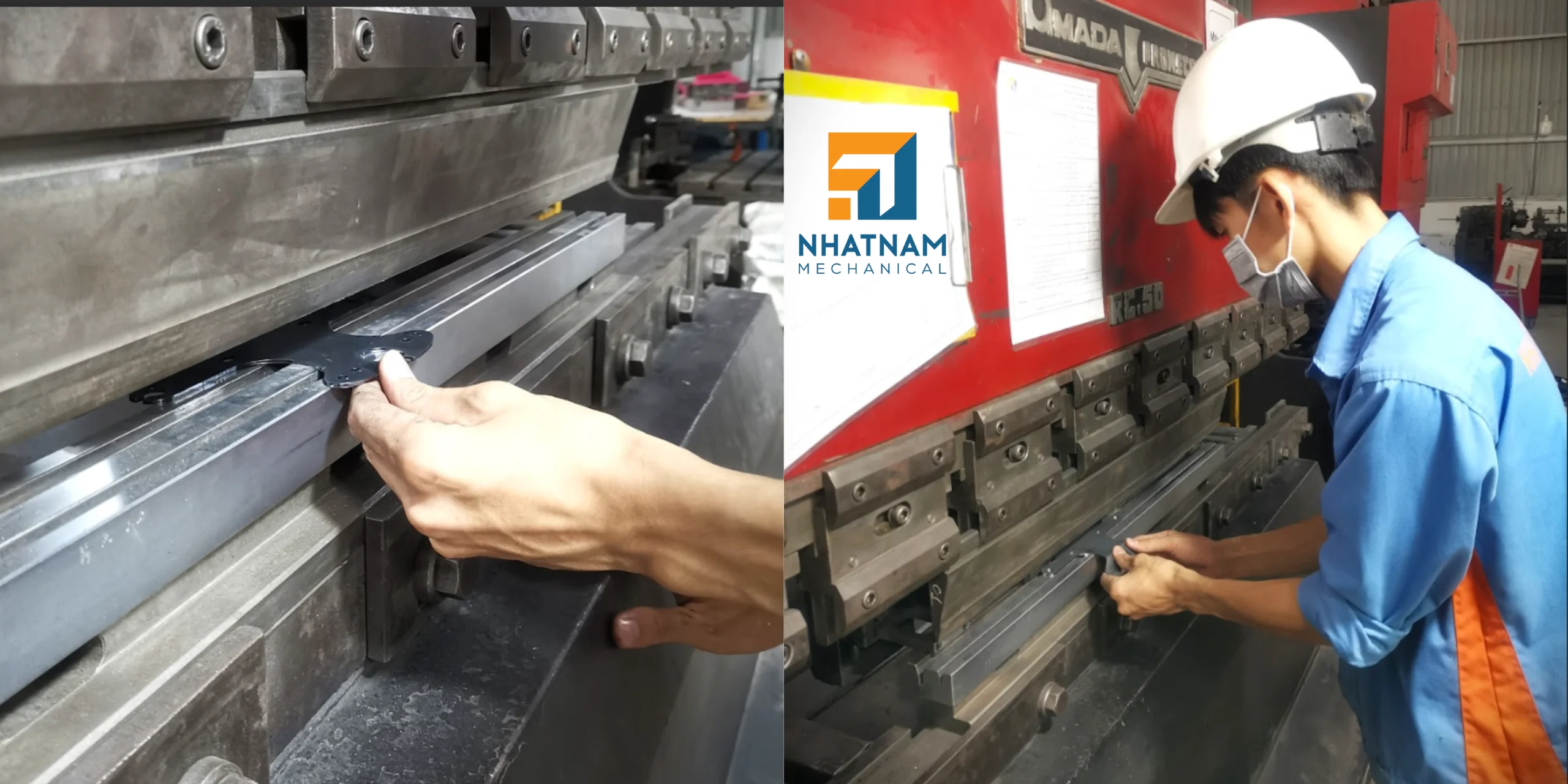
Metal bending is an important process in the field of sheet metal processing in general and metal forming in particular, used to create desired angles and shapes. Metal bending techniques play an important role in metal fabrication, especially when the requirements for precision and product quality are key factors. In this article, we will learn about the steps in metal bending and its role in creating high-quality metal products.
1. Prepare Materials and Equipment
Before starting the bending process, fully preparing materials and equipment is an important step:
- Material selection: Commonly used metal sheets include stainless steel, aluminum, carbon steel, and copper. The thickness and properties of the material will affect the bending method.
- Bending equipment: Depending on the production requirements, equipment such as manual bending machines, hydraulic bending machines, or CNC bending machines will be selected.
- Design check: Confirm the technical drawing and the parameters to be achieved after bending.
2. Measurement and Marking
- Dimensioning: Use precision measuring tools such as calipers or laser measuring devices to determine the locations that need to be bent.
- Marking the bending location: Use a pen or marking tool to ensure the bending path is accurate.
Careful measurement helps minimize errors during the bending process, especially for products that require high precision.
3. Select Bending Angle and Bending Method
Determine the bending angle: Depending on the design, the bending angle can range from 0° to 180°. For small angles, the bending force must be carefully controlled to avoid cracking or warping the metal sheet.
Bending methods:
- Press Brake: Most commonly used for sheet metal processing, utilizing an upper and lower die to form the shape.
- Roll Bending: Used to create large curves and metal tubes.
- Manual Bending: Usually applied to simple or small-quantity parts.
4. Metal Bending Procedure
- Place the metal sheet in the correct position on the bending machine.
- Check the marking lines and machine parameters.
- Apply bending force slowly so that the metal achieves the desired bending shape. For CNC machines, the parameters are pre-programmed to ensure accuracy.
Note: During the bending process, it is necessary to control the bending speed and force to avoid deformation or damage to the material.
5. Inspection and Correction
After completing the bending process, it is necessary to carry out the following inspection steps:
- Measure the bending size and angle with precision measuring tools.
- Compare with the technical drawing to ensure that the product meets the requirements.
- If deviations are detected, minor adjustments can be made or the bending can be repeated to achieve the best results.
6. Finishing the Product
Finally, the product finishing steps include:
- Smoothing the sharp edges: Removing excess parts or sharp edges after bending.
- Surface treatment: Coating, polishing, or plating to increase the durability and aesthetics of the product.
- Final inspection: Ensuring the finished product meets quality standards.
Conclusion
The metal bending process is an important step in the sheet metal processing process, helping to create products with precise shapes and sizes. By following the steps from material preparation, measurement, selecting the bending method to inspection and finishing, businesses can ensure that the product meets both technical and aesthetic requirements.
This process not only helps optimize production time but also improves product quality, meeting the increasing demands of the market.
If you are looking for high-quality metal bending services, please contact Nhat Nam Mechanical, the leading unit in the field of metal processing and manufacturing in Vietnam. With modern equipment dedicated to the bending process such as Amada RG 100, Amada SPH-60, Amada Pega 357 CNC Turret, TruBend 1150, TruBend 1060, etc., and a team of engineers and workers with many years of experience, we ensure to provide customers with the best quality metal bending products and services on the market.
NHAT NAM MECHANICAL CO., LTD contact information: House No. 36, Garland – Phuoc Dien, 72 Duong Dinh Hoi, Phuoc Long B Ward, District 9, Ho Chi Minh City, Vietnam
Contact Japan
Email: tranquy@cokhinhatnam.vn
Tel: +84 938 771 508
Contact English
Email: marketing@cokhinhatnam.vn
Tel: +84 964 092 079
Contact Viet Nam
Email: vinhnt@cokhinhatnam.vn
Tel: +84 964 084 479