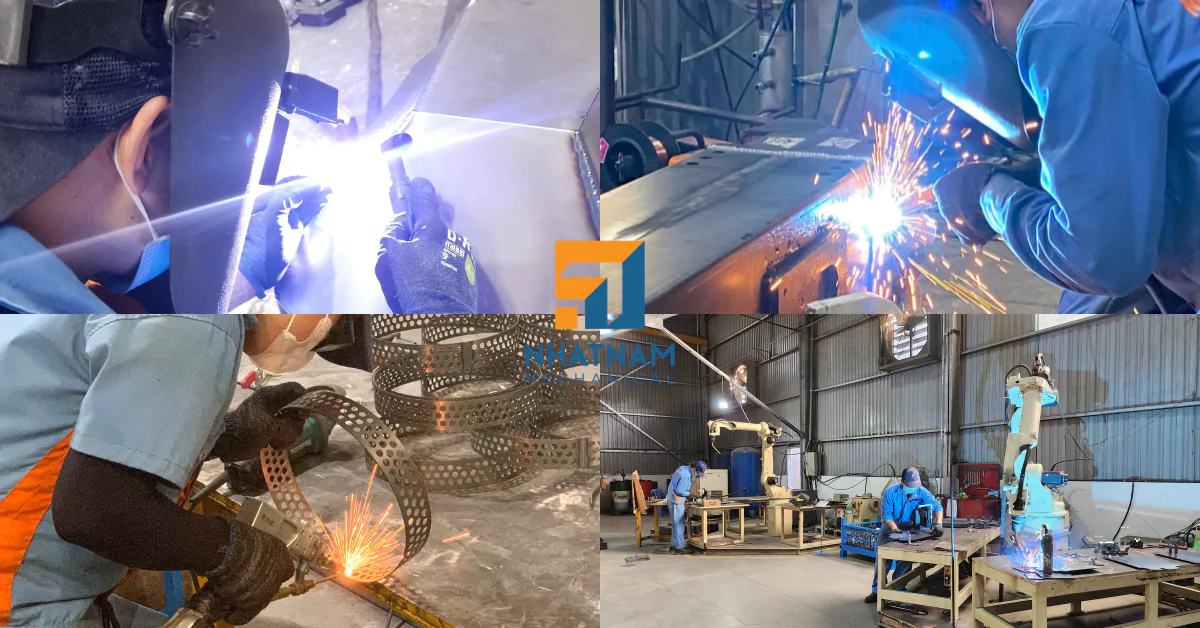
Selecting the right welding process can be challenging, especially with multiple options available. This step-by-step guide will help you determine the best welding method based on factors such as material type, thickness, application, and efficiency.
Step 1: Identify the Type of Metal
Different metals require different welding techniques. Some common materials and their suitable welding processes include:
Steel (Carbon & Stainless): MIG, TIG, Stick Welding
Aluminum: TIG, MIG (with proper shielding gas)
Cast Iron: Stick Welding, Brazing
Copper & Brass: TIG, Brazing
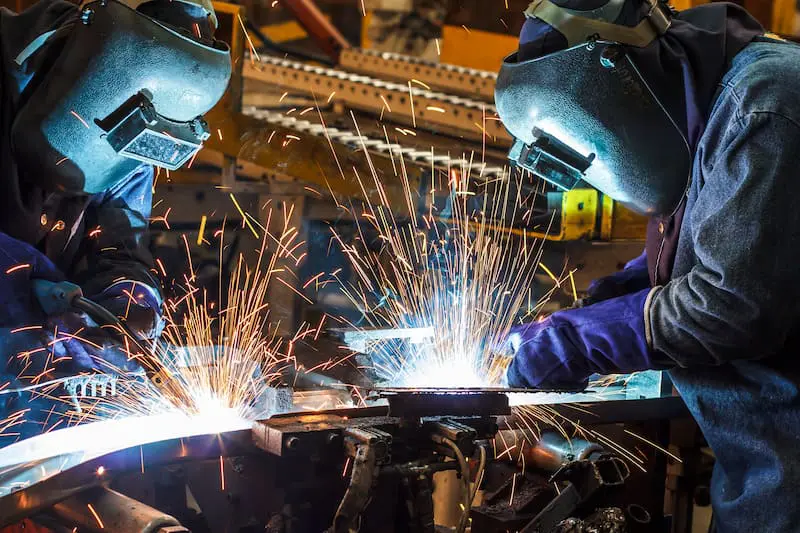
Laser Welding vs. Traditional Welding Methods: A Comparative Analysis
Step 2: Determine Metal Thickness
Thin metals (below 3mm): TIG welding is best due to its precision and low heat input.
Medium thickness (3mm – 12mm): MIG welding offers a balance between speed and strength.
Thick metals (above 12mm): Stick welding or Flux-Cored Arc Welding (FCAW) is ideal for deep penetration and strength.
Aluminum Welding Specialists With Advanced Techniques and Equipment
Step 3: Consider Welding Position
Flat and Horizontal: Most welding methods work well.
Vertical & Overhead: Stick or TIG welding is preferable due to better control and penetration.
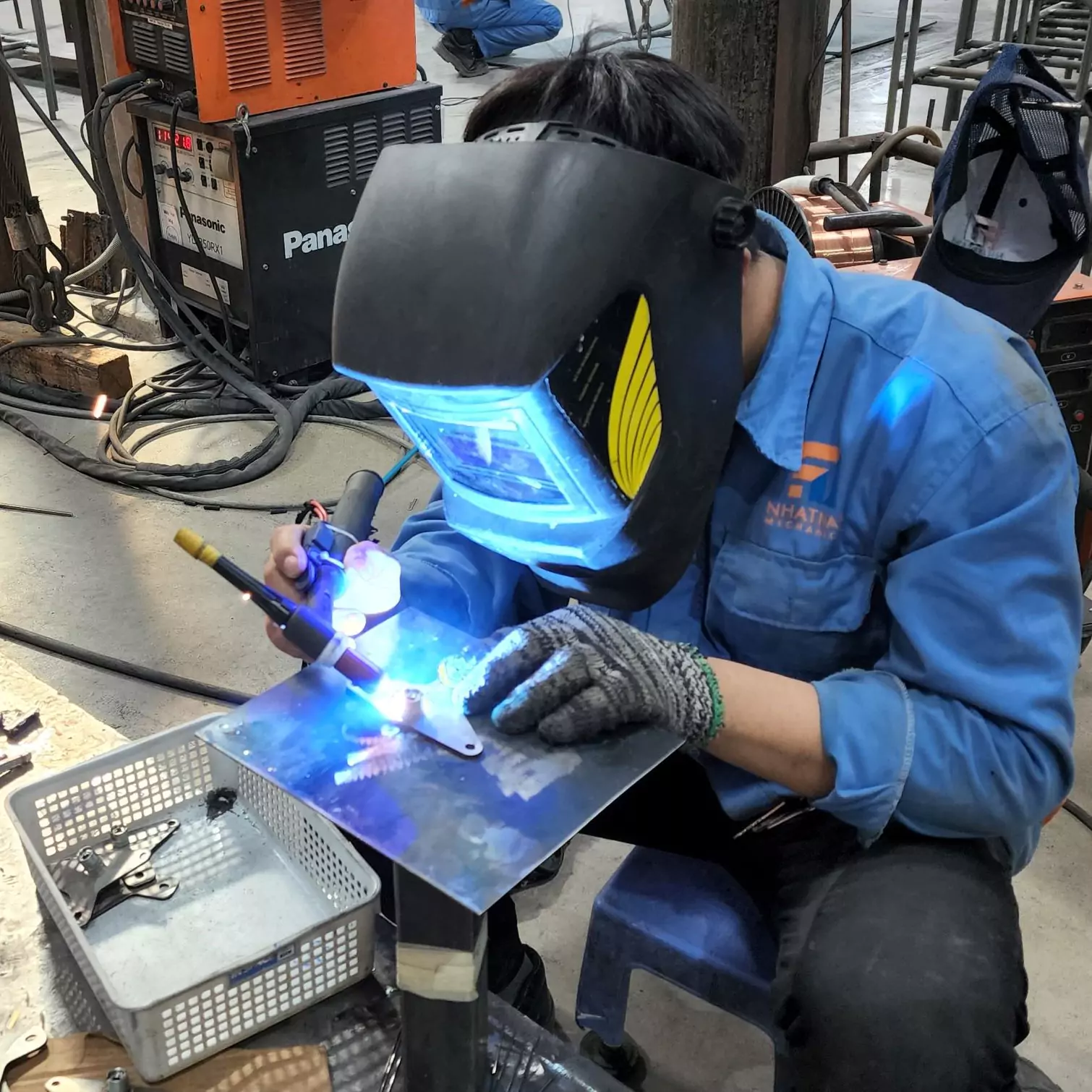
Step 4: Evaluate Strength and Appearance Requirements
Structural applications: Stick or MIG welding for maximum strength.
Aesthetic requirements: TIG welding provides clean, high-quality welds with minimal spatter.
Step 5: Assess Production Speed and Cost
MIG welding: High speed, suitable for mass production.
TIG welding: Slower but offers superior precision.
Stick welding: Affordable and works well in outdoor or harsh conditions.
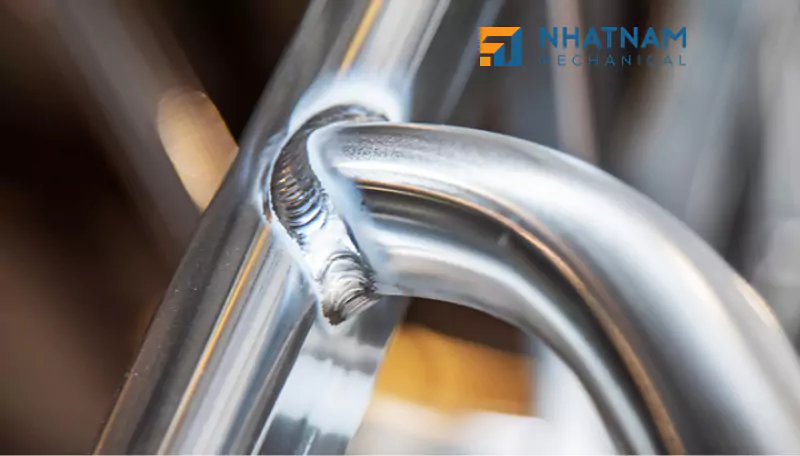
Step 6: Choose the Best Welding Process for Your Needs
Welding Process | Best For | Pros | Cons |
---|---|---|---|
MIG Welding | Medium-thickness metals, fast production | Easy to learn, high deposition rate | Requires shielding gas, not ideal for outdoor work |
TIG Welding | Thin metals, precision work | Clean welds, excellent for aluminum | Slow, requires high skill level |
Stick Welding | Thick metals, outdoor applications | Works in all conditions, low cost | More spatter, requires cleanup |
Flux-Cored Welding (FCAW) | Heavy-duty welding, construction | No need for shielding gas, deep penetration | Produces more fumes, higher equipment cost |
At Nhat Nam Mechanical, we are dedicated to helping you elevate your projects with our expertise and commitment to excellence. If you’re looking to enhance your operations and ensure high-quality results, don’t hesitate to reach out to us. Let’s work together to turn your vision into reality!
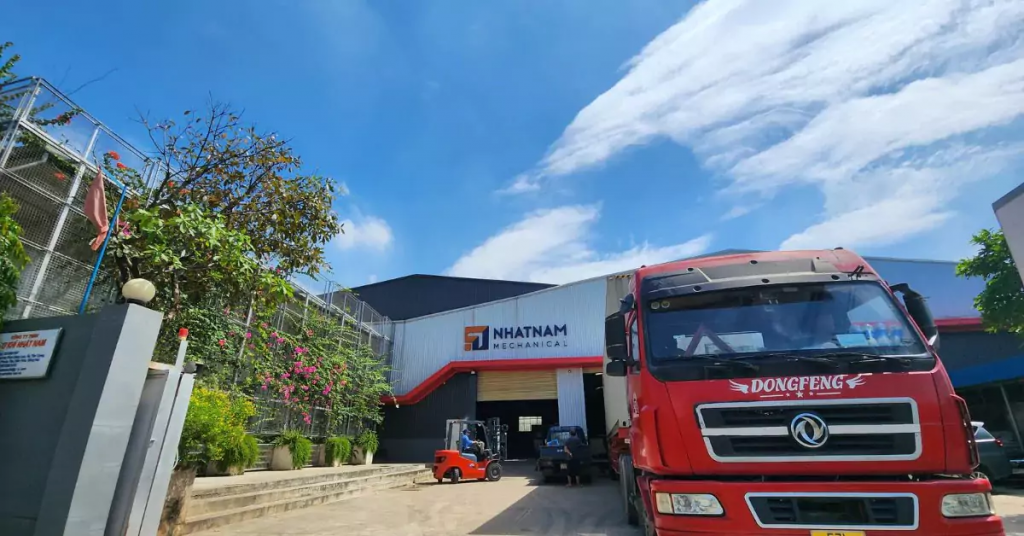
Contact us today to discover how we can support your business needs!
NHAT NAM MECHANICAL CO., LTD contact information:
House No. 36, Garland – Phuoc Dien, 72 Duong Dinh Hoi, Phuoc Long B Ward, District 9, Ho Chi Minh City, Vietnam
Contact Japan
Email: tranquy@cokhinhatnam.vn
Tel: +84 938 771 508
Contact English
Email: marketing@cokhinhatnam.vn
Tel: +84 964 092 079
Contact Vietnam
Email: vinhnt@cokhinhatnam.vn
Tel: +84 964 084 479