Robotic Welding in Mechanical Manufacturing - Applications, Advantages, and Limitations
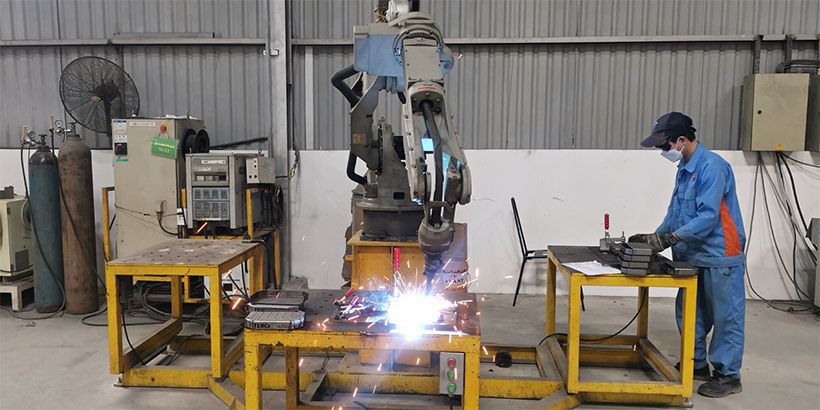
Robotic welding is a type of automation that uses robots to perform welding tasks. Robots are programmed to follow a set of instructions, which allows them to weld accurately and consistently.
Applications of robotic welding
Robotic welding is used in a variety of applications in the mechanical manufacturing industry, including:
- Automotive manufacturing: Robots are used to weld the frames, bodies, and other components of automobiles.
- Aerospace manufacturing: Robots are used to weld the structures and components of aircraft.
- Heavy machinery manufacturing: Robots are used to weld the frames, engines, and other components of heavy machinery.
- Construction: Robots are used to weld the frames, beams, and other components of buildings and other structures.
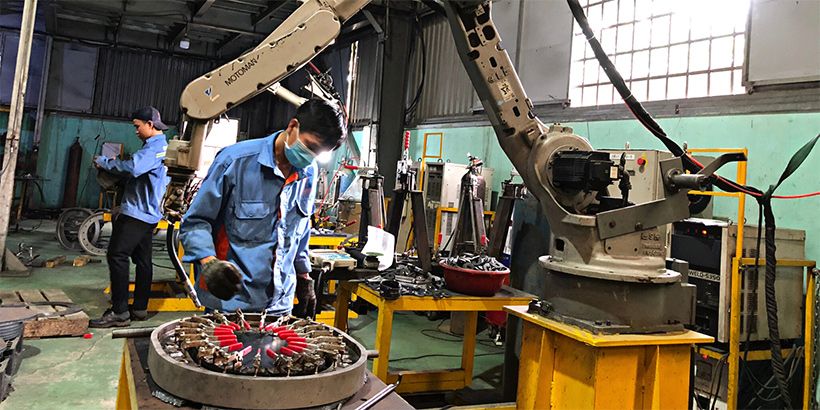
Advantages of robotic welding
Robotic welding offers a number of advantages over manual welding, including:
- Increased productivity: Robots can weld faster and more consistently than human welders. This can lead to significant increases in productivity.
- Improved quality: Robots can weld with greater accuracy and consistency than human welders. This can lead to improved product quality.
- Improved safety: Robots can work in dangerous environments that would be unsafe for humans. This can help to improve safety in the workplace.
- Reduced labor costs: Robots can replace human welders, which can help to reduce labor costs
Limitations of robotic welding
Robotic welding also has some limitations, including:
- High initial cost: Robots can be expensive to purchase and install.
- Limitations on flexibility: Robots are typically programmed to perform a specific task. This can limit their flexibility in manufacturing environments where products vary in size, shape, or material.
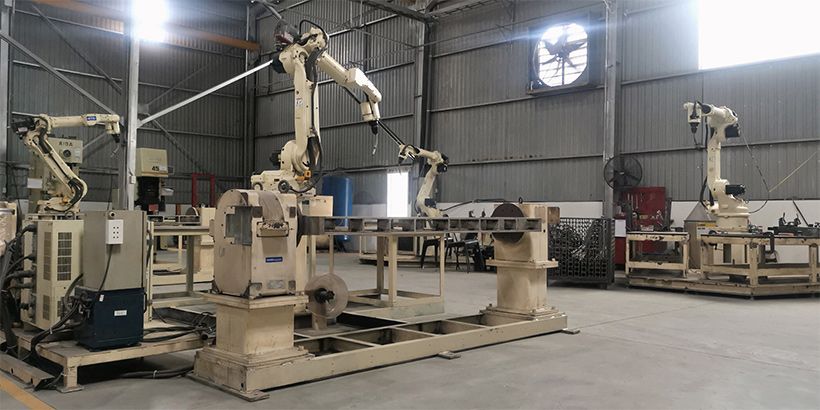
Types of robotic welding
There are a variety of different types of robotic welding, each with its own advantages and disadvantages. Some of the most common types of robotic welding include:
- Point welding: Point welding is a type of welding that uses a series of small, high-intensity welds to join two pieces of metal. It is a fast and efficient method of welding, but it is not as strong as other types of welding.
- MIG welding: MIG welding is a type of welding that uses a wire electrode to melt the metal to be welded. It is a versatile method of welding that can be used to weld a variety of materials.
- TIG welding: TIG welding is a type of welding that uses a tungsten electrode to melt the metal to be welded. It is a precise method of welding that can be used to weld thin materials.
Types of welds
There are also a variety of different types of welds that can be created using robotic welding. Some of the most common types of welds include:
- Butt weld: A butt weld is a type of weld in which the edges of two pieces of metal are joined together.
- Lap weld: A lap weld is a type of weld in which one piece of metal overlaps another piece of metal.
- T-joint weld: A T-joint weld is a type of weld in which one piece of metal is joined to another piece of metal at a right angle.
- Corner weld: A corner weld is a type of weld in which two pieces of metal are joined at a 90-degree angle.