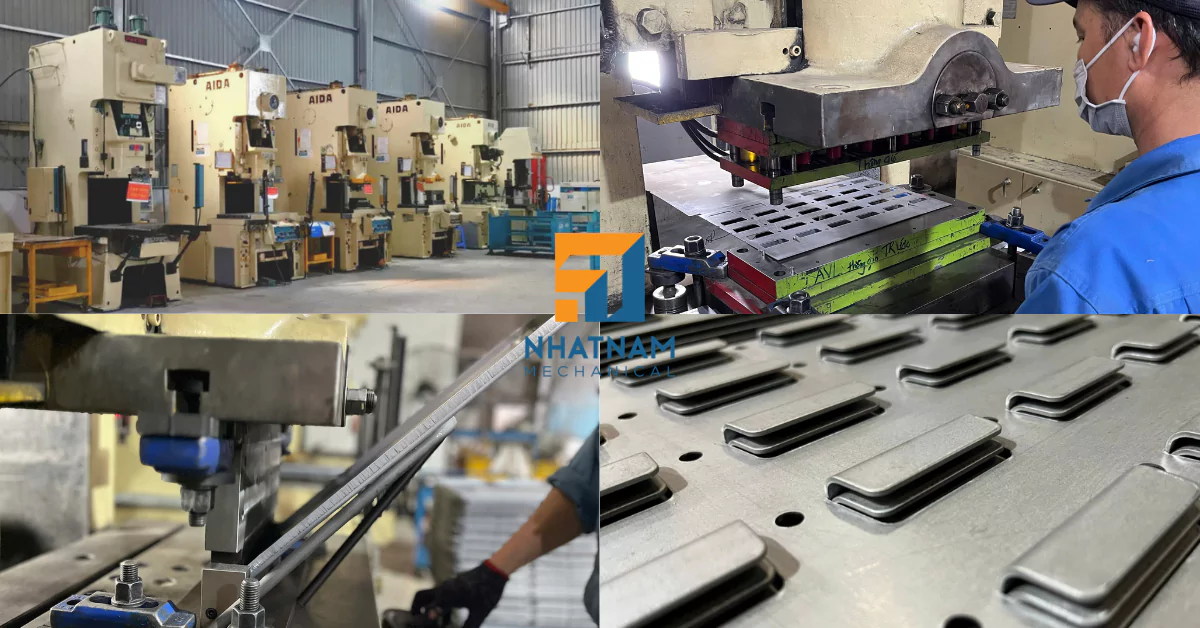
In high-volume sheet metal stamping, consistency is everything. One small deviation in pressure, alignment, or timing can lead to part defects, downtime, and costly rework — especially when working with thin-gauge materials or tight tolerances.
At Nhat Nam, we understand that precision isn’t just a result — it’s a system, built through robust process control at every stage of the stamping operation.
Here are key process control strategies we implement to deliver reliable and repeatable results across stamping jobs.
1. Tooling Condition Monitoring
Consistent output starts with consistent tooling. We monitor the wear of dies and punches in real time or at set batch intervals. Slight dullness or misalignment can lead to:
- Burrs or cracks
- Dimensional deviation
- Scratches or surface deformation
Our approach:
- Regular tool inspection cycles
- Use of high-durability tooling materials
- Backup dies pre-calibrated for fast swap-out
2. Material Feed Accuracy and Alignment
Even with a perfect die, poor feeding can ruin parts. Misaligned or stretched material leads to inconsistent dimensions and improper forming.
What we control:
- Automated decoilers with tension control
- Roller leveling before press entry
- Precision servo feeders with feedback loops
These ensure the sheet enters each stamping cycle in optimal condition, no matter the batch size.
3. Press Force & Stroke Monitoring
Each press cycle is tracked for force, stroke depth, and timing. Irregular stroke force can indicate:
- Material thickness variation
- Die interference
- Machine wear
At Nhat Nam, presses used in sheet metal stamping are equipped with:
- Load sensors to monitor tonnage per stroke
- Programmable logic controllers (PLCs) to detect abnormal force profiles
- Shut-off triggers in case of overload or part misfeed
4. Standardized Work Instructions and Operator Training
Even with automation, human consistency matters. We develop clear work instructions tied to each stamping job, including:
- Machine parameters
- Setup checklist
- Visual defect examples
- Response procedures for off-spec parts
Operators are trained not only to run the press but to understand why the control parameters matter.
Results: Stamping That Performs Under Pressure
Thanks to these process control systems, we deliver:
- Fewer rejected parts
- Repeatability across multiple runs
- Confidence for customers needing reliable stamped components in assemblies, enclosures, or industrial products
Whether you’re producing brackets, panels, or formed parts in stainless steel or aluminum — our system ensures they meet spec, every time.