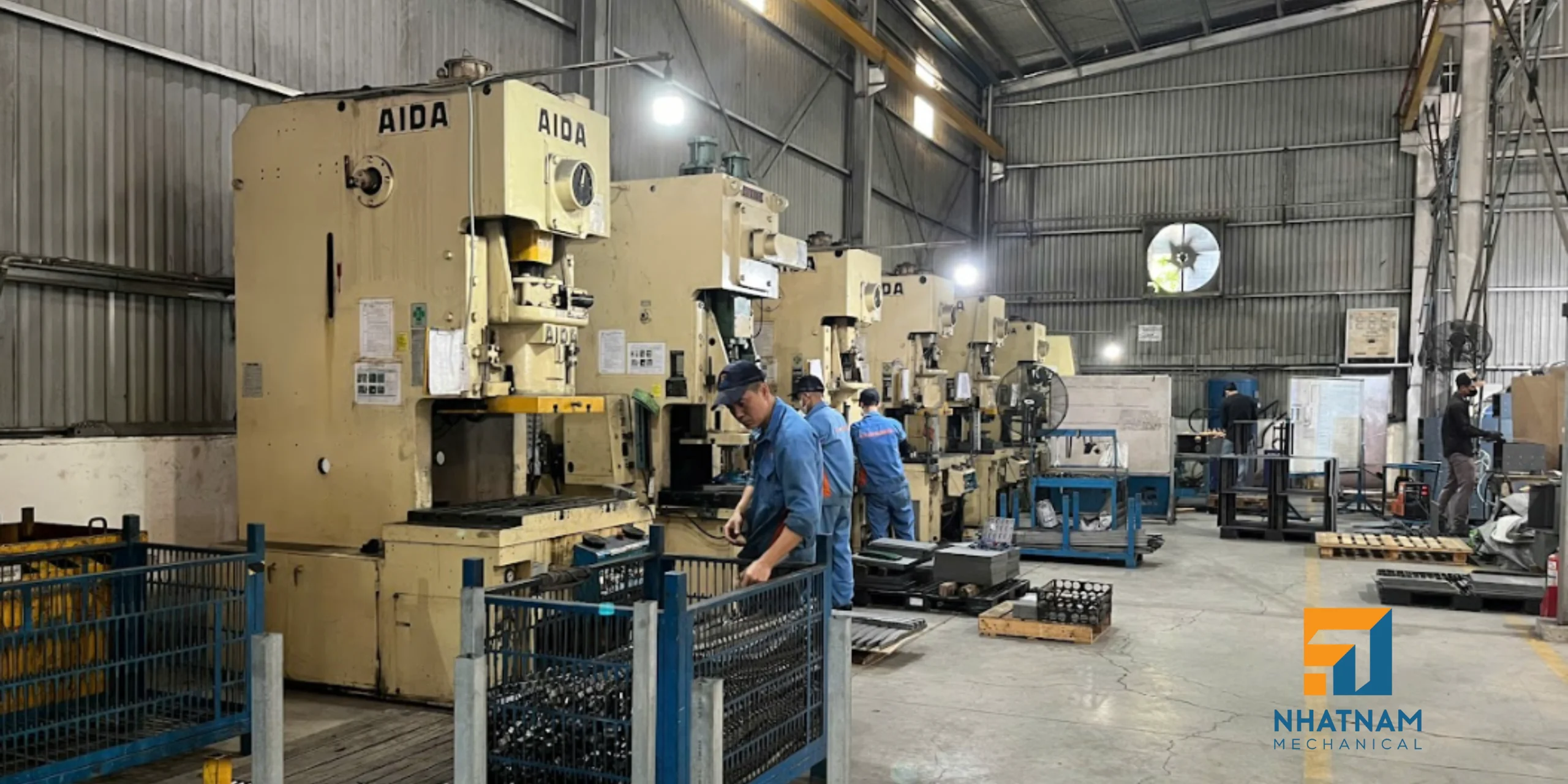
Sheet metal stamping technology plays a crucial role in producing high-quality, cost-effective, and precise products. With the continuous advancement of science and technology, numerous modern technologies have been integrated into sheet metal stamping operations, optimizing the production process, enhancing efficiency, and minimizing errors. This article will explore some of the cutting-edge sheet metal stamping technologies currently in use, highlighting the benefits they offer and the challenges faced during their application in production.
1. What is sheet metal stamping technology?
Sheet metal stamping is a manufacturing process that uses pressure to shape metal into sheets or steel plates. This process can be performed in either a hot or cold state, although it is typically done in the form of cold stamping. This technology is ideal for processing metal sheets with large thicknesses and sizes.
Common types of metals include stainless steel, carbon steel, aluminum, copper, titanium, and other alloys.
Sheet metal thickness typically ranges from 0.5 mm to 6 mm, depending on the application.
2. Modern technologies in sheet metal stamping operations:
CNC punching technology:
CNC punching (Computer Numerical Control) uses computer-controlled machines to process metal sheets according to pre-programmed designs. This process includes cutting, bending, punching, and shaping, allowing for the creation of products with high precision and complex details.
Laser stamping technology:
This method uses lasers to cut, engrave, and shape metal with high precision and smooth surfaces.
Cold stamping technology:
Cold stamping is a pressure processing method used to manufacture products from sheet material, steel plates, or coils in a cold state. This method is widely used in industries such as automotive, aerospace, shipbuilding, electrical equipment, and household appliances.
Hot stamping technology:
Hot stamping is performed by heating metal sheets, making it suitable for materials that are difficult to shape. This method improves the ductility of the material, reduces the required stamping force, and allows the creation of products with complex shapes.
Hydraulic stamping technology:
This technology uses pressure from liquids to shape metal sheets, enabling the production of parts with complex shapes and high precision. Hydraulic stamping also helps reduce stress and deformation on the material.
Deep stamping:
Deep stamping is used to create products with great depth, such as pots, tanks, or machine housings. This is one of the methods for processing plates using molds under high pressure. It requires high precision stamping dies and force to avoid cracking or breaking the material.
3. Benefits of modern technologies:
- High precision: Metal stamping enables the production of parts with high precision, meeting strict technical requirements across many industries.
- Increased productivity: The use of modern machinery and technology boosts production speed, reduces processing time, and enhances work efficiency.
- Cost savings: Compared to other processing methods, metal stamping typically has lower production costs, especially in mass production.
- Flexibility: Metal stamping technology can be applied to various materials and shapes, catering to diverse production needs.
- Smooth product surface: The stamping process helps create smooth product surfaces, minimizing the need for additional finishing.
- Minimized material waste: The metal stamping process optimizes raw material usage, reduces waste, and saves material costs.
- Increased product durability: Metal stamping products are often durable, can withstand heavy loads, and have long service lives.
4. Challenges when applying modern technology:
- High initial investment costs: Modern metal stamping machinery and equipment require significant investment, which can make it challenging for small and medium-sized enterprises to adopt new technology.
- Technical requirements and workforce training: The operation and maintenance of modern metal stamping equipment require highly skilled professionals. Therefore, comprehensive training programs are necessary to ensure production efficiency.
- Ensuring quality and accuracy: The metal stamping process demands high accuracy. Even small mistakes in mold design or the stamping process can lead to defective products, waste, and reduced production efficiency.
- Optimizing the production process: Stamping mold processing is a complex task that involves the coordination of many different stages. Optimizing the production process helps improve efficiency and minimize costs.
- Material management and raw material costs: Selecting and using the right materials is critical. Using the wrong material can lead to issues such as poor durability, wear, or breakage.
- Equipment maintenance and repair: Modern metal stamping machinery requires regular maintenance to ensure stable operation. A lack of spare parts or specialized technicians can negatively impact production efficiency.
Nhat Nam Mechanical specializes in providing sheet metal stamping services using advanced technology to meet a wide range of customer needs. With a stamping force of up to 110 tons and a stamping stroke of 180mm, the company is capable of forming complex sheet metal parts.
Advantages of choosing metal stamping services at Nhat Nam Mechanical:
- Advanced technology: Applying Japanese technology in processing to ensure high quality and precision.
- Professional team: A team with many years of experience to ensure products meet quality standards.
- Fast delivery: Committed to on-time delivery to meet customers’ production requirements.
NHAT NAM MECHANICAL CO., LTD contact information: House No. 36, Garland – Phuoc Dien, 72 Duong Dinh Hoi, Phuoc Long B Ward, District 9, Ho Chi Minh City, Vietnam
Contact Japan
Email: tranquy@cokhinhatnam.vn
Tel: +84 938 771 508
Contact English
Email: marketing@cokhinhatnam.vn
Tel: +84 964 092 079
Contact Viet Nam
Email: vinhnt@cokhinhatnam.vn
Tel: +84 964 084 479