Ensuring the quality of welds in sheet metal processing not only helps maintain structural strength but also directly affects the...
Read More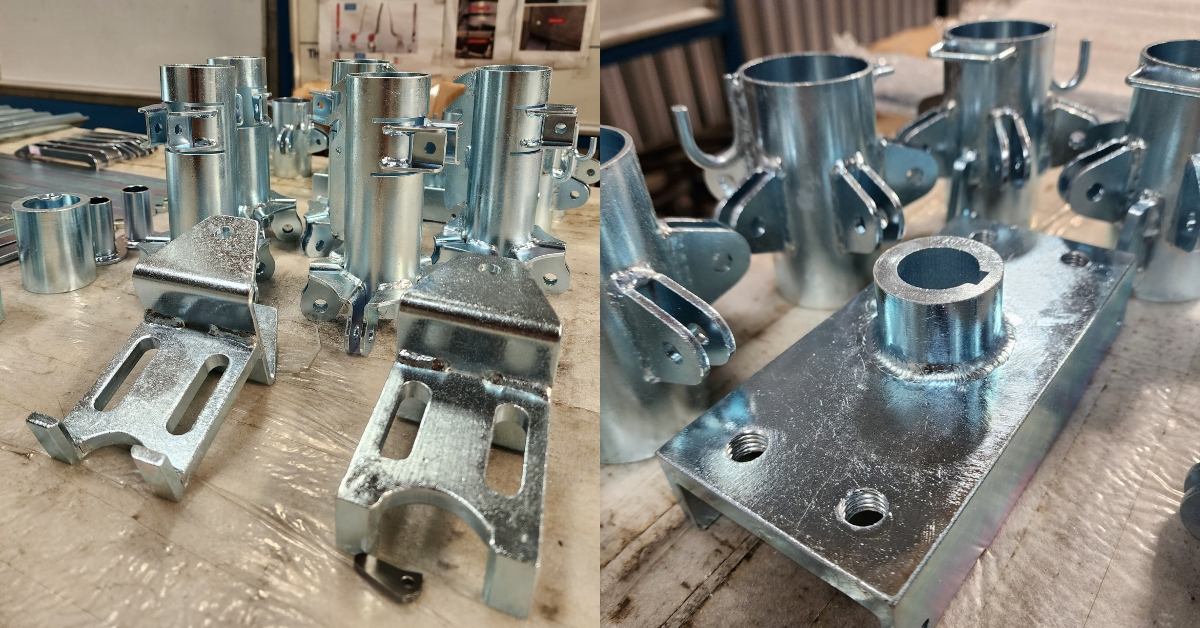
1. The history of galvanized steel
The history of galvanized steel dates back to the early 19th century.
Early Zinc Coatings: The use of zinc coatings to protect iron and steel from corrosion can be traced back to ancient times. The ancient Egyptians, for example, coated ironware with a thin layer of zinc to prevent rusting.
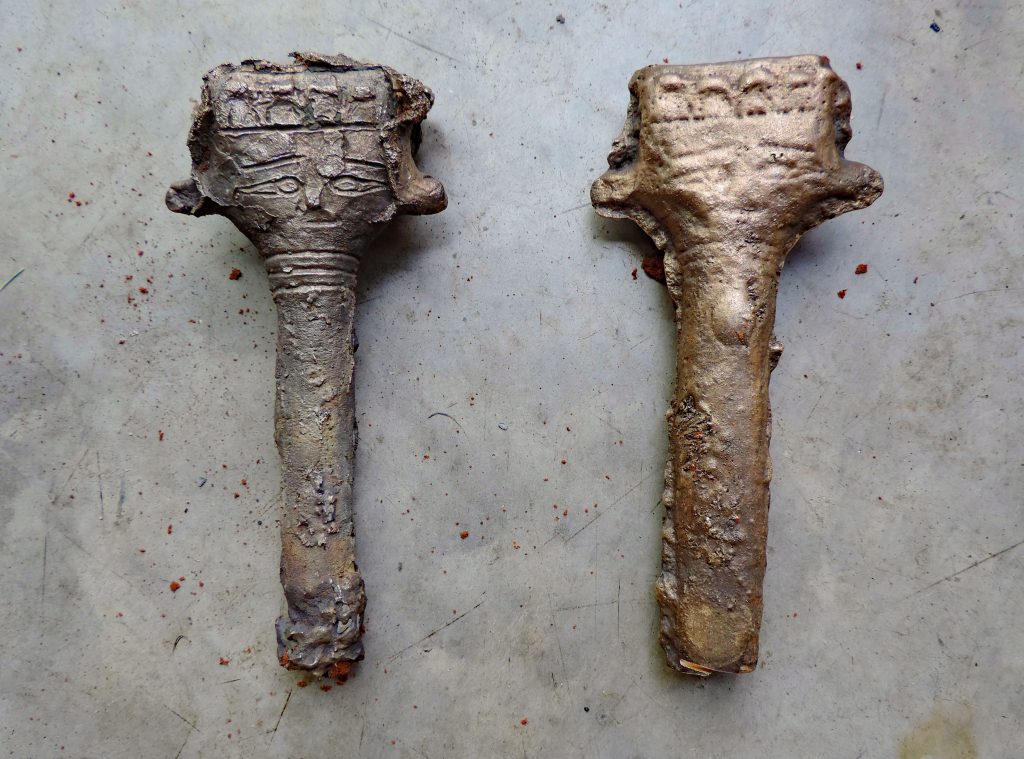
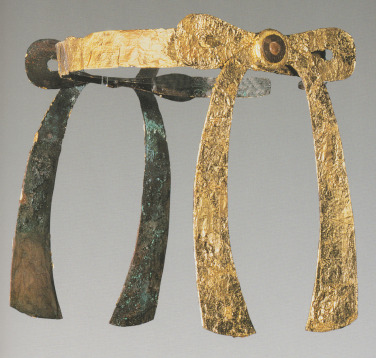
The Discovery of Galvanization: The process of galvanization, which involves the application of a thicker layer of zinc to steel, was discovered by Luigi Galvani, an Italian scientist, in the late 18th century. Galvani observed that when two dissimilar metals were connected and immersed in an electrolyte (such as saltwater), a protective layer formed on the metal that was more electronegative. This process was later named after him as “galvanization.”
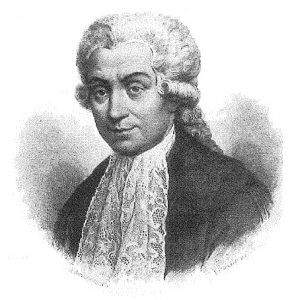
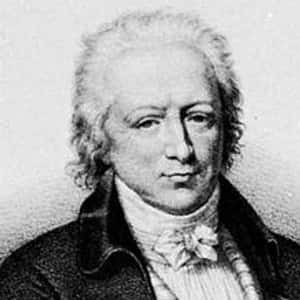
Early Industrial Applications: The industrial application of galvanized coatings began in the early 19th century. In 1837, the French engineer Stanislas Sorel patented a method for galvanizing iron by dipping it into molten zinc. This process, known as hot-dip galvanizing, is still widely used today.
Commercialization and Advancements: Galvanized steel gained popularity in the mid-19th century as a cost-effective and durable material. The development of more efficient galvanizing techniques and equipment further enhanced its production and made it more accessible for various applications.
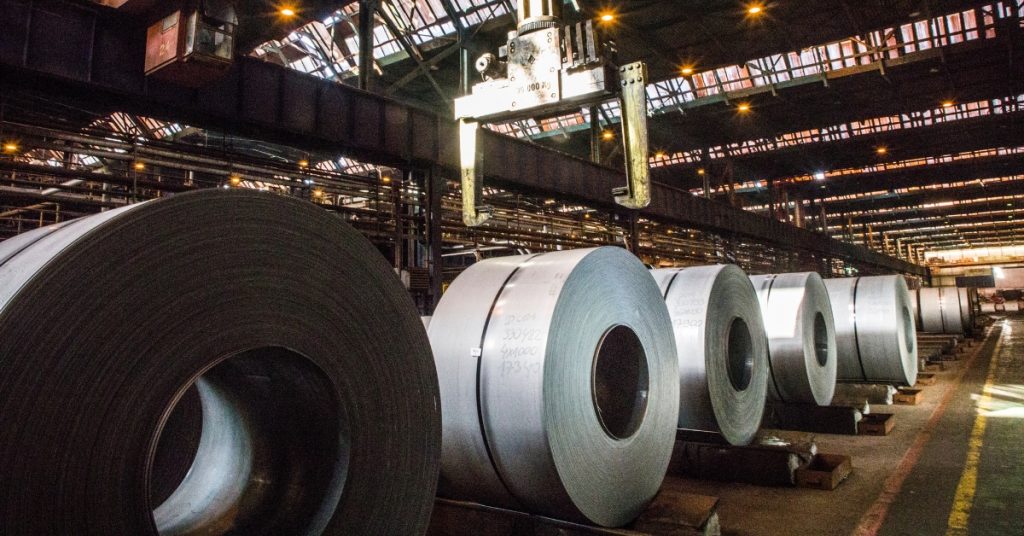
Modern Galvanizing Processes: Over time, different galvanizing processes were developed to suit specific applications. In addition to hot-dip galvanizing, other methods such as electro-galvanizing, mechanical galvanizing, and continuous galvanizing were introduced. Each process has its own advantages and is used depending on factors like the size, shape, and intended use of the steel.
2. The key features and characteristics of galvanized steel
Galvanized steel, whether hot-dip galvanized or electro-galvanized, possesses several key features and characteristics. Here are the main ones:
- Corrosion Resistance: Galvanized steel provides excellent corrosion resistance. The zinc coating acts as a protective barrier, shielding the underlying steel from rust, moisture, and other corrosive elements. It offers reliable protection even in harsh environments.
- Durability: Galvanized steel is highly durable and long-lasting. The zinc coating provides a tough and abrasion-resistant surface that can withstand impacts, scratches, and exposure to various weather conditions. It helps extend the lifespan of the steel components.
- Cost-Effectiveness: Galvanized steel is a cost-effective choice due to its long lifespan and minimal maintenance requirements. The initial investment in galvanizing is relatively low compared to other corrosion protection methods. It reduces replacement and upkeep costs over time.
- Full Coverage Protection: Galvanizing ensures complete coverage of the steel surface, including hard-to-reach areas such as corners, crevices, and intricate shapes. It creates a uniform layer of zinc that provides consistent protection across the entire steel component.
- Self-Healing Properties: If the zinc coating is damaged or scratched, galvanized steel can exhibit self-healing properties. The zinc sacrificially corrodes to protect the exposed steel, forming a protective layer that helps prevent further corrosion.
- Versatility: Galvanized steel is versatile and finds applications in various industries. It can be formed, fabricated, and welded like regular steel, making it suitable for a wide range of structural and functional purposes.
- Recyclability: Galvanized steel is fully recyclable, making it an environmentally friendly choice. The zinc coating can be easily recovered during the recycling process, reducing waste and conserving resources.
- Ease of Inspection: Galvanized steel allows for easy visual inspection of the coating quality. The appearance of the coating can indicate its thickness and uniformity, providing assurance of its protective capabilities.
Galvanized steel is widely used in construction, infrastructure, automotive, agriculture, and many other industries. It serves as an ideal material for structural components, building materials, outdoor equipment, fencing, electrical conduits, and more.
Overall, the key features and characteristics of galvanized steel include its corrosion resistance, durability, cost-effectiveness, full coverage protection, self-healing properties, versatility, recyclability, and ease of inspection. These qualities make galvanized steel a popular choice for applications where corrosion protection and long-term performance are essential.
3. Galvanized steel category
Galvanized steel is typically categorized based on the manufacturing process, the type of coating, and the intended application. Here are a few common categories of galvanized steel:
3.1. Hot-Dip Galvanized Steel
This is the most common and widely used type of galvanized steel. Hot-dip galvanizing involves immersing the steel in a bath of molten zinc to create a protective coating. It provides excellent corrosion resistance and durability. The hot-dip galvanizing process involves several steps to create a protective coating of zinc on the surface of steel components. Here is an overview of the process:
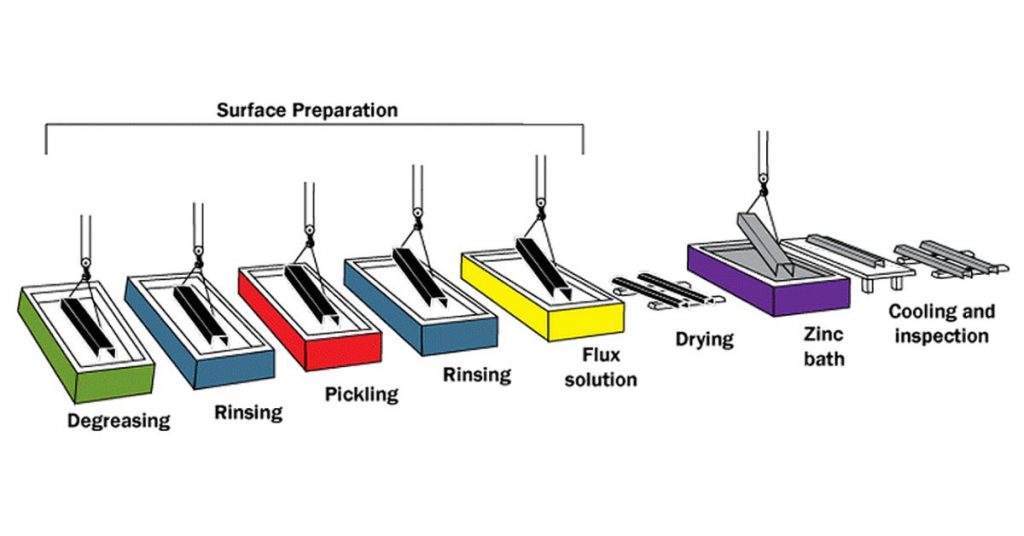
- Surface Preparation: The steel components undergo thorough cleaning to remove any dirt, rust, grease, or other contaminants. This step is crucial to ensure proper adhesion of the zinc coating. Surface preparation methods may include degreasing, acid pickling, and/or abrasive blasting.
- Fluxing: After cleaning, the steel is immersed in a flux solution. The flux helps to remove any remaining oxides from the surface and promotes the formation of a clean surface for the zinc to bond effectively.
- Galvanizing Bath Preparation: A bath or kettle containing molten zinc is heated to the required temperature, typically around 450-460°C (840-860°F). The bath consists of a mixture of zinc and other additives to control the coating thickness and appearance of the final product.
- Immersion in the Galvanizing Bath: The cleaned and fluxed steel components are carefully immersed in the molten zinc bath. The components are completely submerged to ensure even coverage by the zinc coating. They may be submerged individually or in batches, depending on the size and shape of the items.
- Alloying and Metallurgical Reaction: When the steel components are immersed in the zinc bath, a metallurgical reaction occurs between the iron in the steel and the molten zinc. This reaction forms a series of zinc-iron alloy layers on the surface of the steel. These alloy layers provide the corrosion protection and adhesion of the zinc coating to the steel.
- Removal from the Bath and Quenching: Once the desired coating thickness is achieved, the steel components are lifted out of the galvanizing bath. Excess zinc is allowed to drain off, and the components may be quenched in water or air to cool them rapidly.
- Post-Treatment: After galvanizing, the components may undergo additional processes, such as inspection, passivation, or chromate conversion coating. These processes can enhance the appearance, further improve corrosion resistance, or provide specific surface properties.
The hot-dip galvanizing process creates a durable and uniform zinc coating on the steel surfaces, offering excellent corrosion protection and extending the lifespan of the steel components. The thickness of the zinc coating can vary depending on the specific application and customer requirements.
It's important to note that the hot-dip galvanizing process is conducted in specialized facilities with proper safety measures to handle the high temperatures and molten zinc. The process is regulated by industry standards and quality control procedures to ensure the effectiveness and reliability of the galvanized steel products.
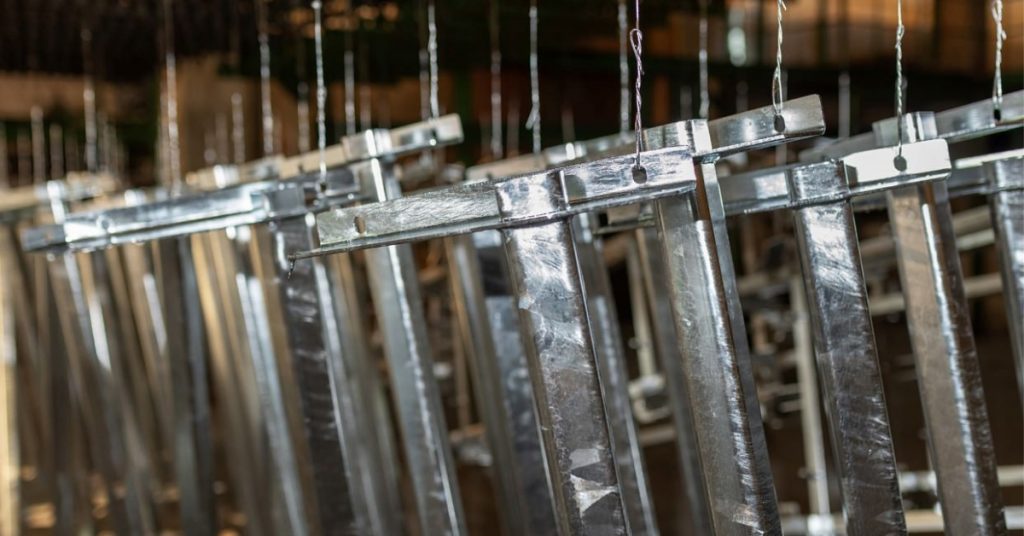
3.2. Electro-Galvanized Steel:
This is the most common and widely used type of galvanized steel. Hot-dip galvanizing involves immersing the steel in a bath of molten zinc to create a protective coating. It provides excellent corrosion resistance and durability. The hot-dip galvanizing process involves several steps to create a protective coating of zinc on the surface of steel components. Here is an overview of the process:
3.2. Electro-Galvanized Steel
Also known as electroplating. In this process, a thin layer of zinc is electroplated onto the steel surface. Electro-galvanized steel is generally smoother and has a thinner coating compared to hot-dip galvanized steel. It is often used for applications that require a more aesthetic finish or where a thinner coating is sufficient.
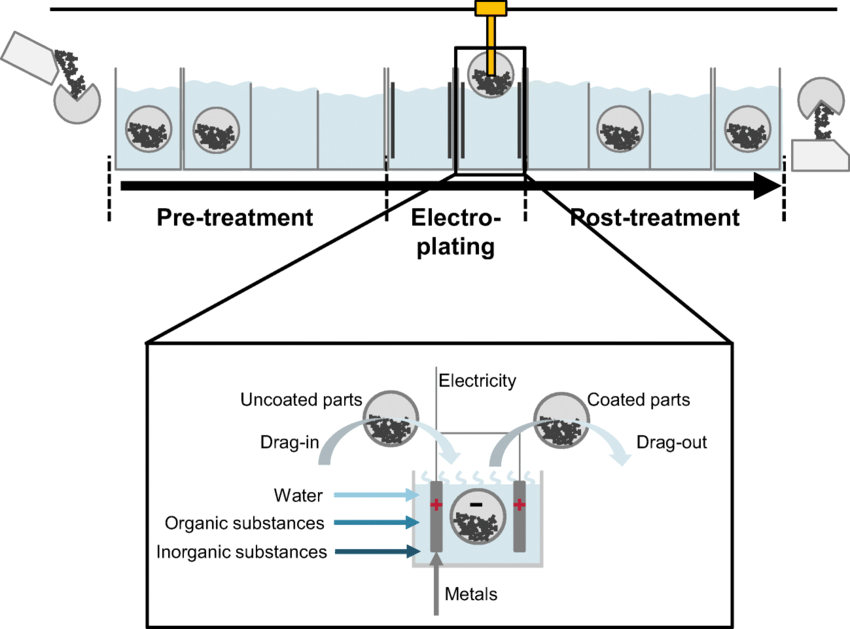
The electro-galvanizing process, also known as electroplating, involves the deposition of a thin layer of zinc onto the surface of steel components. Here is a general overview of the electro-galvanizing process:
- Surface Preparation: Similar to hot-dip galvanizing, the steel components undergo thorough cleaning to remove any dirt, rust, grease, or other contaminants. Surface preparation methods may include degreasing, acid cleaning, or abrasive blasting.
- Acid Activation: After cleaning, the steel is immersed in an acid bath, typically containing sulfuric acid. This bath removes any remaining oxides from the surface and activates it for electroplating.
- Electroplating Bath Preparation: An electrolyte solution is prepared, typically consisting of zinc sulfate or zinc chloride. The solution contains zinc ions that will be deposited onto the steel surface.
- Electroplating: The steel components are submerged in the electroplating bath along with an anode, which is usually made of pure zinc. When an electric current is applied, zinc ions are attracted to the steel surface and form a thin layer of zinc through a process called electrodeposition. The current flow causes a chemical reaction that results in the deposition of zinc onto the steel surface.
- Control of Plating Parameters: The electro-galvanizing process allows for control over various parameters such as current density, bath composition, temperature, and plating time. These parameters are carefully monitored and adjusted to achieve the desired coating thickness and quality.
- Post-Treatment: After electroplating, the components may undergo additional processes, such as rinsing, drying, and passivation. Passivation helps to improve the corrosion resistance and appearance of the electro-galvanized steel by applying a protective chemical layer on the zinc coating.
- Inspection and Quality Control: The electro-galvanized steel components undergo rigorous inspection to ensure that the coating thickness, adhesion, and overall quality meet the specified standards and customer requirements.
It's worth noting that the electro-galvanizing process requires specialized equipment and expertise to control the plating parameters accurately. The process is conducted in controlled environments to ensure the quality and consistency of the electro-galvanized steel products.
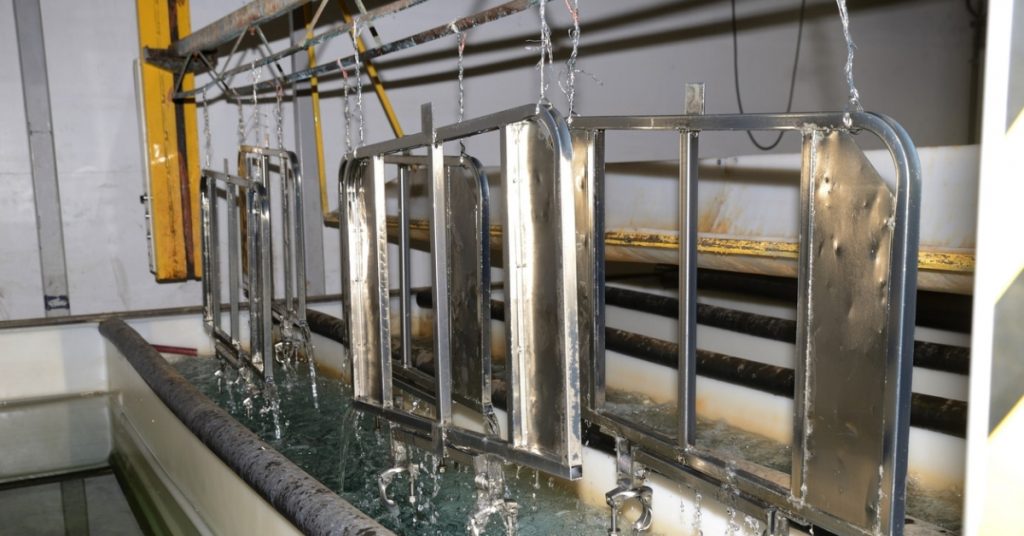
3.3. Galvanized Steel Sheet and Coil
Galvanized steel is often produced in the form of sheets or coils. These flat or rolled products are used in various industries, including construction, automotive, and appliances. Galvanized steel sheets and coils are available in different thicknesses and sizes to suit specific applications.
3.4. Galvanized Structural Steel
This category includes galvanized steel used in structural applications, such as beams, columns, and trusses. Galvanized structural steel provides strength, durability, and corrosion resistance, making it suitable for construction projects.
3.5. Galvanized Wire and Mesh
Galvanized steel wire and mesh are commonly used in fencing, agriculture, construction, and industrial applications. The galvanized coating enhances the wire's resistance to rust and corrosion, increasing its lifespan and structural integrity.
3.6. Galvanized Pipes and Tubes
Galvanized steel pipes and tubes are widely used in plumbing, gas supply, and various industrial applications. The galvanized coating protects the pipes from corrosion and extends their service life.
These are just a few examples of the different categories of galvanized steel. The specific category or grade of galvanized steel can vary based on the manufacturing standards, coating thickness, and the specific requirements of the application.
4. Applications of galvanized steel
Galvanized steel finds a wide range of applications across various industries due to its excellent corrosion resistance and durability. Here are some common applications of galvanized steel:
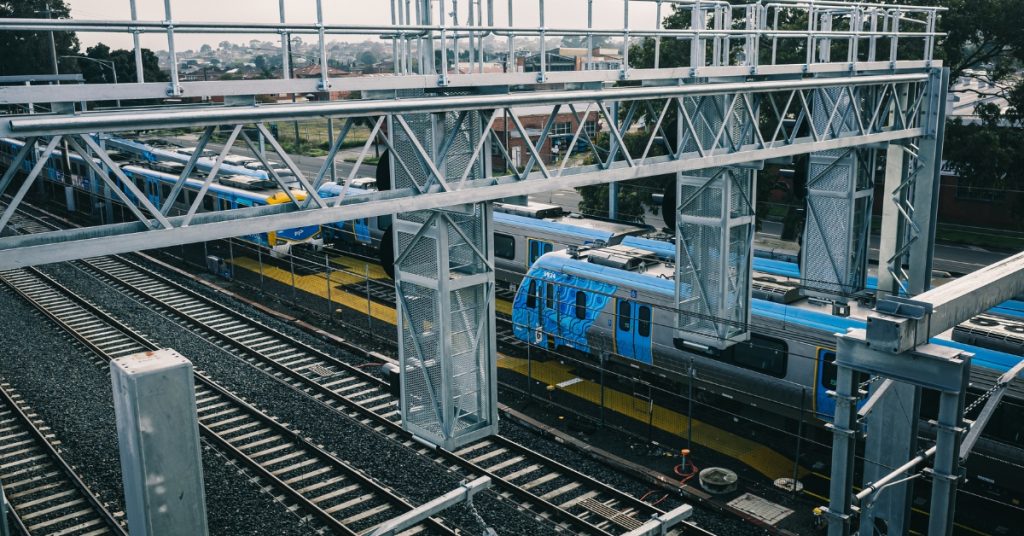
- Construction and Infrastructure: Galvanized steel is extensively used in construction and infrastructure projects. It is used for structural components such as beams, columns, and trusses, as well as roofing, wall cladding, fences, guardrails, and gratings. Galvanized steel provides long-term protection against corrosion in buildings, bridges, highways, stadiums, and other infrastructure projects.
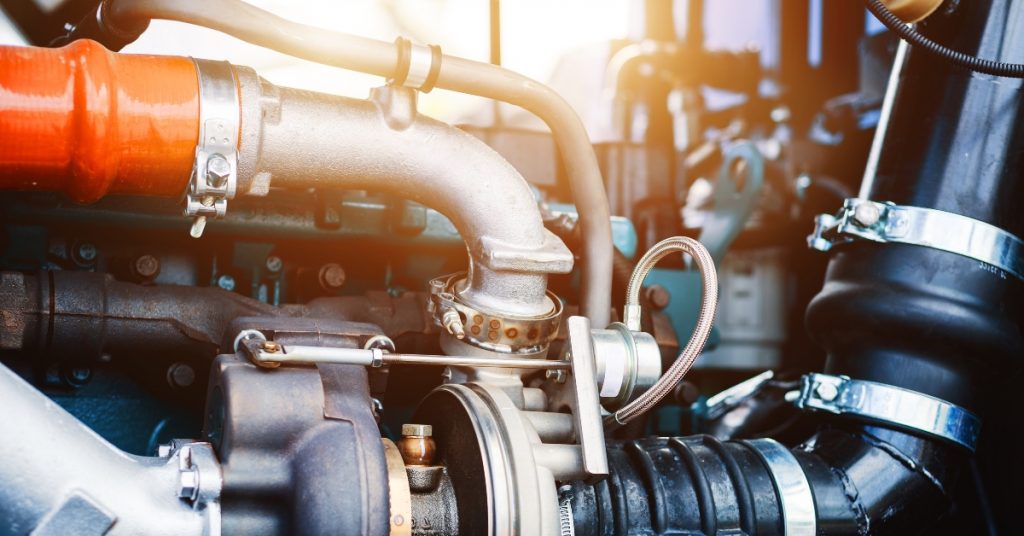
- Automotive Industry: Galvanized steel is employed in the automotive industry for manufacturing various components. It is used in the production of car frames, body panels, chassis parts, exhaust systems, and reinforcements. The corrosion resistance of galvanized steel helps enhances the longevity and durability of vehicles, particularly in regions with harsh weather conditions and exposure to road salt.
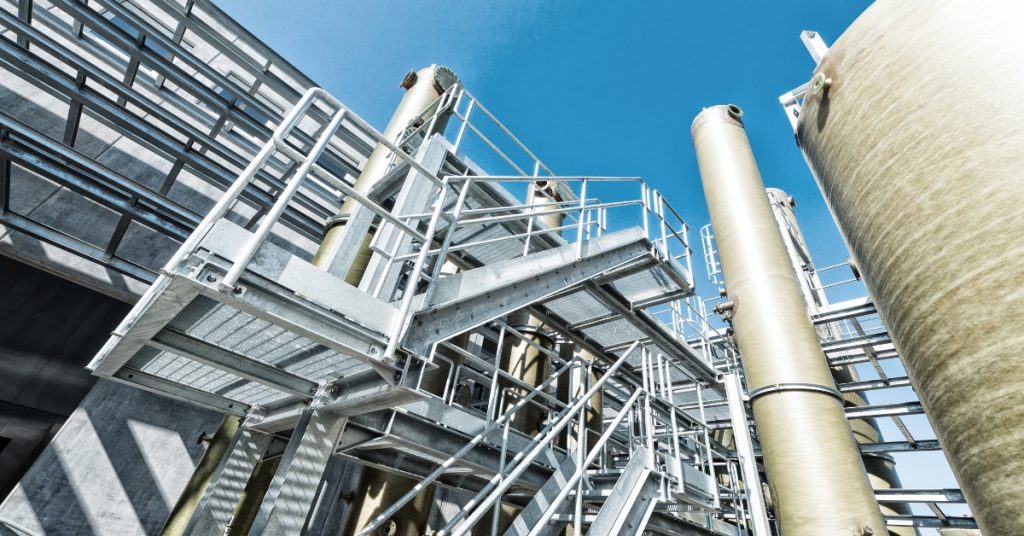
- Industrial Equipment and Machinery: Galvanized steel is used in various industrial applications. It is employed for manufacturing equipment and machinery components that require corrosion resistance, durability, and structural integrity. Examples include storage tanks, industrial piping, HVAC systems, material handling equipment, and industrial shelving.
These are just a few examples of the diverse applications of galvanized steel. Its corrosion resistance, durability, and cost-effectiveness make it a preferred choice in industries where protection against corrosion is crucial for long-term performance and reliability.
Regarding how Nhat Nam Mechanical’s sheet metal fabrication services can help your project involving galvanized steel, here are some ways:
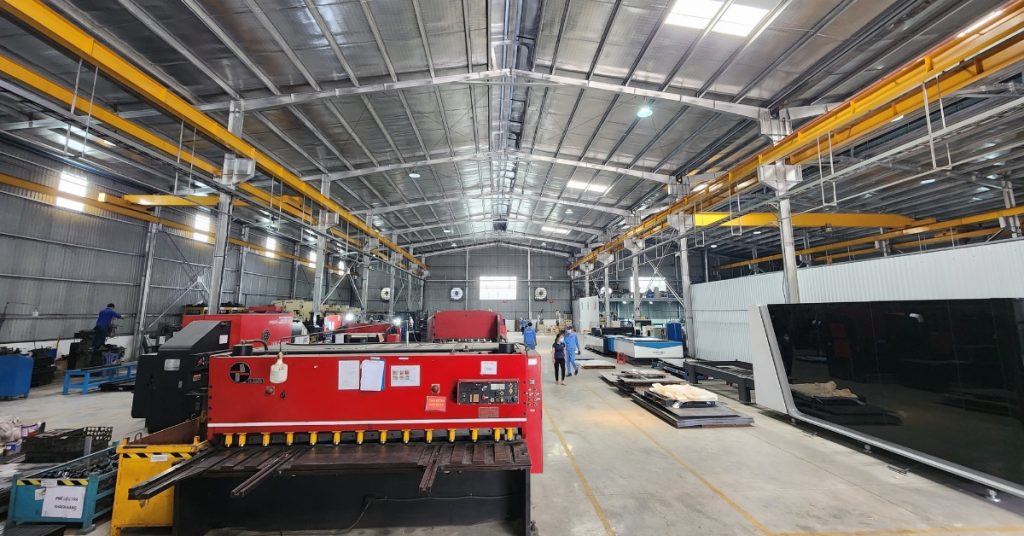
- Custom Fabrication: We can work with galvanized steel sheets to fabricate custom components or structures based on your project requirements. We can cut, bend, and shape the galvanized steel to create the desired shapes and sizes.
- Welding and Joining: If your project requires the joining of galvanized steel pieces, Nhat Nam Mechanical can provide welding services to securely bond the components together. We have expertise in various welding techniques suitable for galvanized steel.
- Finishing and Surface Treatment: We can provide surface treatments for galvanized steel products, such as painting or powder coating. This can enhance the appearance, provide additional protection, or meet specific project requirements.
- Prototyping and Production: Whether you need a one-off prototype or a large production run, Nhat Nam Mechanical can assist with both. We can fabricate galvanized steel components or assemblies in the desired quantities to support your project.
It’s important to discuss your specific project requirements with Nhat Nam Mechanical to determine the extent of our capabilities and how we can best assist you with your galvanized steel fabrication needs.
Related Post
What Defines the Best Sheet Metal Fabrication Services in Vietnam?
Finding the best sheet metal fabrication services isn’t just about choosing a vendor — it’s about partnering with a team...
Read MoreApplications of Aluminium Sheet Metal Fabrication in the Aerospace Industry
Aluminum sheet metal processing is one of the key technologies in the modern aerospace industry. With its lightweight, durable, highly...
Read More