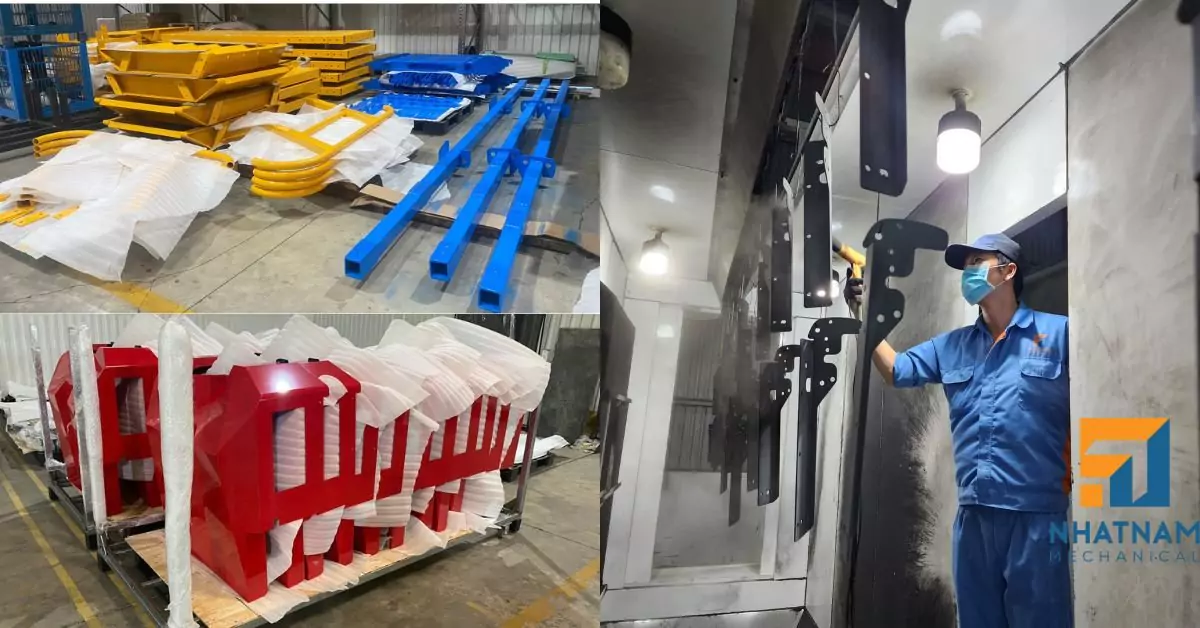
Powder coating is a popular method of applying a protective and decorative finish to a wide range of materials and products. It is known for its durability, high-quality finish, and environmental friendliness. Unlike traditional liquid paints, powder coating is applied as a dry powder, which is then cured under heat to form a hard, protective layer. This process is widely used in industries such as automotive, architecture, appliances, and furniture, among others.
History of Powder Coating
The concept of powder coating dates back to the late 1940s and early 1950s, but it wasn’t until the 1960s that the technology began to gain significant traction. Initially, powder coating was primarily used for coating metal parts, but advancements in technology and materials have expanded its applications to various substrates, including plastics, glass, and wood.
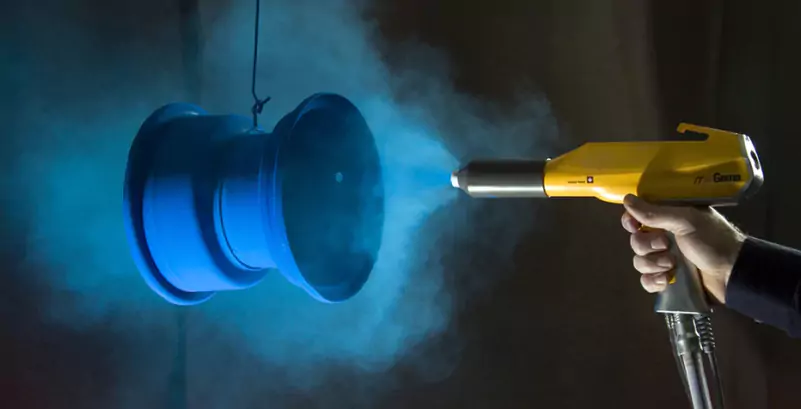
Types of Powder Coating
Powder coatings are broadly categorized into two main types: thermoplastic and thermosetting powders.
- Thermoplastic Powder Coatings: These coatings melt and flow when heated but do not undergo a chemical change during the curing process. This allows them to be re-melted and reformed, making them reusable and recyclable. Common thermoplastic powder coatings include nylon, polyvinyl chloride (PVC), and polyethylene.
- Thermosetting Powder Coatings: These coatings, on the other hand, undergo a chemical reaction during the curing process, forming a stable, durable finish that cannot be re-melted. Once cured, they are resistant to high temperatures and provide excellent mechanical properties. Examples of thermosetting powder coatings include epoxy, polyester, and polyurethane.
The Powder Coating Process
The powder coating process involves several steps, each critical to achieving a high-quality finish.
- Surface Preparation: Proper surface preparation is essential for ensuring good adhesion and a smooth finish. This typically involves cleaning the substrate to remove any dirt, grease, or other contaminants. Depending on the material, this may include mechanical abrasion, chemical cleaning, or both.
- Application: The powder is applied to the substrate using an electrostatic spray gun. The gun imparts an electrostatic charge to the powder particles, which are then attracted to the grounded substrate. This creates a uniform coating that adheres well to the surface.
- Curing: After the powder is applied, the coated part is placed in an oven where it is heated to a specific temperature. This causes the powder to melt and flow, forming a continuous film. For thermosetting powders, the heat also initiates a chemical reaction that cross-links the polymer chains, resulting in a hard, durable finish.
- Cooling: Once the curing process is complete, the part is allowed to cool and solidify. This cooling period is crucial for ensuring the coating achieves its final properties, including hardness, adhesion, and appearance.
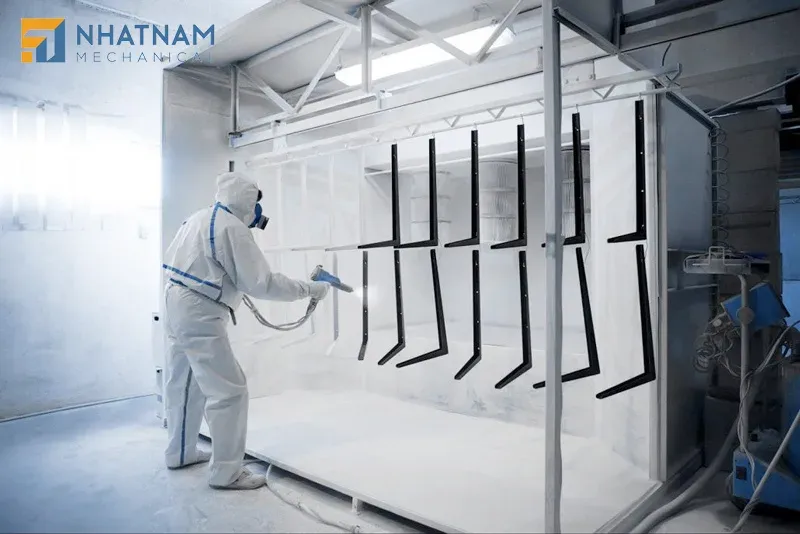
Advantages of Powder Coating
Powder coating offers several advantages over traditional liquid painting methods, making it a preferred choice in many industries.
- Durability: Powder coatings are known for their toughness and resistance to chipping, scratching, and wear. They provide a long-lasting finish that can withstand harsh environmental conditions, making them ideal for outdoor applications.
- Environmental Benefits: Powder coating is an environmentally friendly process. Unlike liquid paints, it does not require solvents, which means there are no volatile organic compounds (VOCs) released into the atmosphere. Additionally, overspray can be collected and reused, minimizing waste.
- Efficiency: The powder coating process is highly efficient. The electrostatic application ensures a high transfer efficiency, meaning more powder reaches the part and less is wasted. This reduces material costs and increases productivity.
- Aesthetic Appeal: Powder coatings can be formulated in a wide range of colors, textures, and finishes, providing excellent aesthetic versatility. They can achieve smooth, glossy finishes or textured, matte appearances, depending on the desired look.
- Cost-Effective: While the initial setup cost for powder coating equipment may be higher than for traditional painting methods, the long-term savings in material costs, waste reduction, and improved efficiency make it a cost-effective solution.
Applications of Powder Coating
Powder coating is used across a diverse range of industries due to its versatility and performance characteristics.
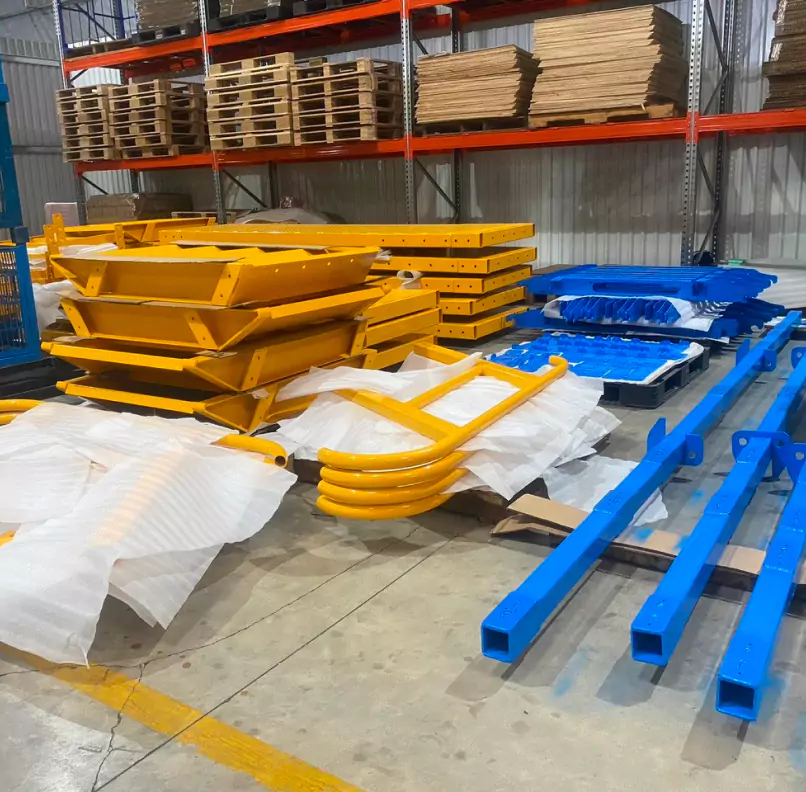
- Automotive Industry: Powder coating is widely used in the automotive industry for coating wheels, engine parts, and other components. Its durability and resistance to chemicals and heat make it ideal for automotive applications.
- Architectural Applications: In architecture, powder coatings are used for coating aluminum extrusions, doors, windows, and facades. They provide excellent weather resistance and can be formulated to meet specific aesthetic and performance requirements.
- Appliances: Many household appliances, such as refrigerators, washing machines, and ovens, feature powder-coated finishes. The coatings provide a durable, attractive finish that is easy to clean and maintain.
- Furniture: Powder coating is also popular in the furniture industry, particularly for metal furniture. It offers a wide range of color and finish options and provides a robust, scratch-resistant surface.
- General Industrial Applications: Beyond these specific industries, powder coating is used for a variety of general industrial applications, including coating tools, equipment, and machinery parts.
Innovations in Powder Coating
As technology advances, so too does the field of powder coating. Recent innovations have focused on improving the performance and versatility of powder coatings, as well as enhancing their environmental benefits.
- Low-Temperature Curing: Traditionally, powder coatings require high curing temperatures, which can limit their use on heat-sensitive substrates. However, recent developments in low-temperature curing powders have expanded the range of materials that can be powder coated, including plastics and composites.
- Advanced Formulations: New powder coating formulations have been developed to provide enhanced properties, such as improved UV resistance, antimicrobial capabilities, and increased flexibility. These advancements open up new possibilities for powder coating applications.
- Automation and Robotics: The use of automation and robotics in the powder coating process has improved efficiency, consistency, and precision. Automated systems can apply coatings with greater accuracy and uniformity, reducing waste and increasing productivity.
- Eco-Friendly Powders: Research and development efforts are continually focused on creating more eco-friendly powder coatings. This includes developing powders with higher transfer efficiencies, lower VOC emissions, and enhanced recyclability.
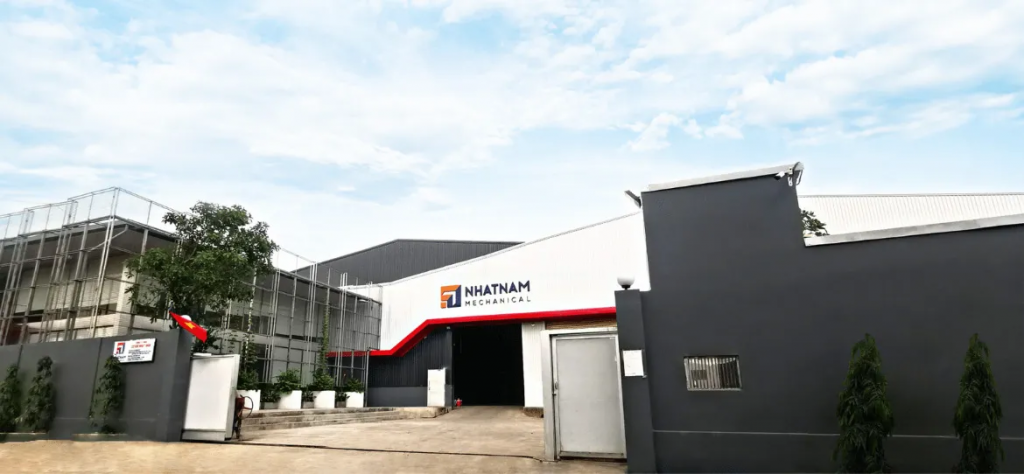
If you are looking for a partner for reputable and quality powder coating products in Vietnam, Nhat Nam Mechanical is a company worth considering. With a team of experienced staff and advanced, modern machinery and equipment… ensuring products are made with high precision, on schedule, and reliably.
NHAT NAM MECHANICAL CO., LTD contact information: House No. 36, Garland – Phuoc Dien, 72 Duong Dinh Hoi, Phuoc Long B Ward, District 9, Ho Chi Minh City, Vietnam
Contact Japan
Email: tranquy@cokhinhatnam.vn
Tel: +84 938 771 508
Contact English
Email: sale03@cokhinhatnam.vn
Tel: +84 964 092 079
Contact Vietnam
Email: vinhnt@cokhinhatnam.vn
Tel: +84 964 084 479