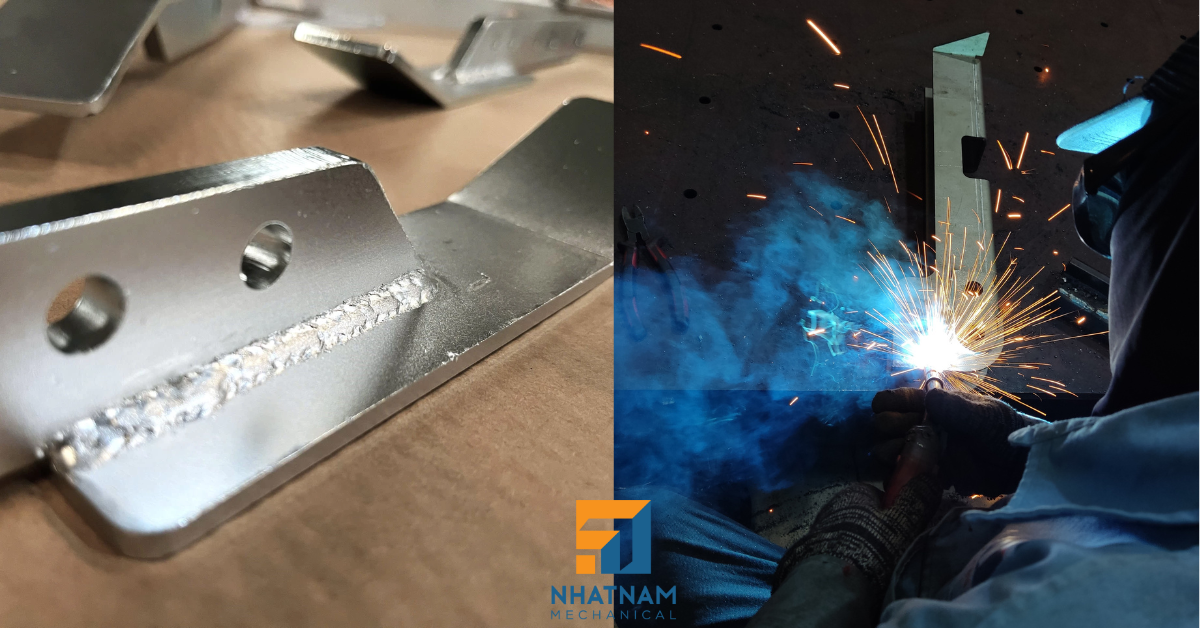
High-quality welds play an important role in ensuring the durability, safety, and performance of metal structures in industries such as construction, automotive, and aerospace. To evaluate the quality of welds, various criteria are used, ranging from visual inspection to advanced testing methods. A professional welding service ensures that every weld meets industry standards, enhancing structural integrity and longevity. This article will analyze the factors that determine qualified welds and the importance of choosing a reliable welding service for high-quality results.
1.Visual Inspection
- Uniformity: A good weld must have an even weld line without cracks or pores.
- Penetration: The weld must have good penetration into the base material to ensure durability.
- Surface defect-free: No cracks, pores, burrs, or edge burns should be present.
2. Mechanical Properties of Welds
- Tensile strength: The weld must withstand tensile force without breaking.
- Toughness: The weld must be able to withstand deformation without breaking.
- Hardness: The weld should not be too brittle, as this could lead to cracking under load.
3. Common Welding Defects and How to Identify Them
- Pores: Occur due to gas trapped in the weld, reducing its strength.
- Weld cracking: Can result from a cooling rate that is too fast or material contamination.
- Edge burn: Happens when the temperature is too high, causing the base material to erode.
- Poor fusion: Occurs when the filler metal does not completely fuse with the base material.
4. Weld Quality Testing Methods
Non-Destructive Testing (NDT):
- Ultrasonic Testing (UT): Detects internal defects.
- X-ray Testing: Identifies defects within the weld.
- Magnetic Particle Testing (MT): Detects surface cracks.
Destructive Testing:
- Tensile and bend tests: Assess the weld’s strength.
- Macro etching: Examines penetration and weld structure.
5. High-Quality Weld Evaluation Standards
- AWS D1.1: Standard for welding steel structures.
- ASME Section IX: Standard for welding pressure vessels and pipelines.
- ISO 5817: Standard for fusion weld quality.
- API 1104: Standard for welding oil and gas pipelines.
Conclusion
Weld quality testing is crucial for ensuring the safety and performance of metal structures. By following industry standards, conducting rigorous testing, and identifying defects early, businesses can ensure that every weld is of optimal quality. Investing in highly skilled personnel and modern testing methods is the best way to ensure the success of welding projects.
Nhat Nam Mechanical is proud to be a professional welding service provider, meeting the needs of sheet metal processing, steel structures, and precision mechanical components. With a team of highly skilled welders and a modern machinery system, we provide MIG, TIG, arc welding, spot welding, and automatic welding solutions, ensuring the highest durability, aesthetics, and quality for each product.
Our services cater to various industries, including mechanical engineering, automotive, aviation, oil and gas, and construction. We are committed to providing welding products that meet international standards and fulfill all stringent technical requirements of our customers. Contact Nhat Nam Mechanical today for expert consultation and detailed project quotations!
NHAT NAM MECHANICAL CO., LTD contact information:
House No. 36, Garland – Phuoc Dien, 72 Duong Dinh Hoi, Phuoc Long B Ward, District 9, Ho Chi Minh City, Vietnam
Contact Japan
Email: tranquy@cokhinhatnam.vn
Tel: +84 938 771 508
Contact English
Email: marketing@cokhinhatnam.vn
Tel: +84 964 092 079
Contact Vietnam
Email: vinhnt@cokhinhatnam.vn
Tel: +84 964 084 479