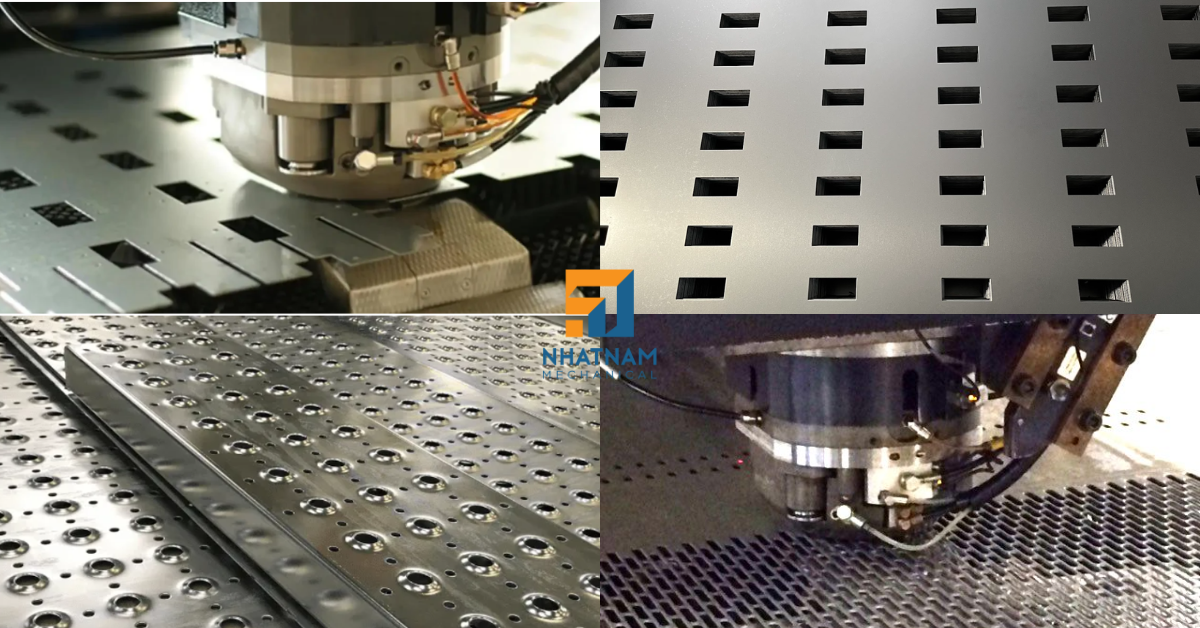
In the sheet metal fabrication industry, punching is often regarded as a simple process – just creating holes, slots, or grooves on the material’s surface. However, the quality of the punching operation can have a profound impact on the accuracy, durability, aesthetics, and assembly of the entire product.
Understanding the relationship between punching and output quality is crucial for professional manufacturers, especially when working with precision mechanical products, industrial equipment, or components with high technical requirements.
1. Accuracy Starts with Every Punch
One of the most significant factors influenced by the punching process is the location and size of the punched holes. If the location is off by even 0.2 – 0.3mm, or the diameter is slightly distorted due to mold wear or machine errors, the entire assembly system can become misaligned, warped, or lose its joints. This not only affects the product’s aesthetics but also complicates the installation process—or even makes it impossible if the parts require a tight fit.
Example: In the manufacture of electrical cabinets, if the screw holes are misaligned, the cabinet face will not close tightly, leading to dust and water leakage, which could damage the electrical equipment inside.
Therefore, every punch must ensure high precision, not just on the first punch, but also maintain consistency over hundreds or thousands of parts.
2. Burrs and Sharp Edges: The Silent Enemies of Durability and Aesthetics
When metal is punched without proper control of force, or the die is worn, burrs (sharp edges or small metal chips) often appear at the edges of the holes. Burrs may not be immediately visible, but they are the cause of scratches, torn wires, or even corrosion of the coating later.
Burrs also prevent the electrostatic paint layer from adhering evenly, leading to peeling after a period of use. This is why poorly processed products often have a short paint life and are prone to rust—even if the base material is stainless steel or galvanized.
A standard punching process must include a finishing stage to address the punched edges, such as light grinding, polishing, or using an automatic burr grinder. This significantly improves product quality, both in terms of appearance and durability in real-world environments.
3. Sheet Deformation: A Consequence of Inappropriate Punching Force
In many cases, after punching, the metal sheet may become warped, wavy, or slightly concave around the punched hole area. This is often the result of applying too much punching force on a sheet of metal that is too thin, or a lack of uniform support under the die.
Slight deformations may not be noticeable during the punching step, but they can cause gaps, warping, or mismatches when the parts are assembled—especially in products that require high precision, such as machine frames, equipment housings, control panels, etc.
To avoid this, the processing unit needs a technician who understands the material properties (thickness, hardness, ductility) and calibrates the punching machine accordingly. Additionally, using high-quality dies and properly arranging the supports helps minimize the feedback force that causes warping.
4. Chain Impact on Subsequent Stages
An often overlooked but critically important issue is that a misplaced punch hole or poor cutting edge can affect all the following stages—from assembly, welding, and coating to packaging and even the safety of the final product.
A mispunched part can cause alignment issues during welding, leading to shape deviations.
Poorly punched holes prevent welding robots from positioning accurately, reducing weld quality.
Warped panels cause uneven paint coatings, which are more likely to peel off in harsh industrial environments.
Therefore, the quality of the punching process should not be treated as a secondary step. It must be regarded as a key factor in the production chain.
Conclusion: Start with Standard Punching for a Quality Product
A correctly performed punching process creates a solid foundation for all subsequent steps. That is why, at Nhat Nam Mechanical, we always consider the punching step as a critical factor in the entire production value chain.
With a modern CNC punching system, European-standard punching dies, and a team of highly trained technicians, we ensure:
Punching holes with an accuracy of ±0.1mm
No burrs, thanks to post-punching processing
Minimal sheet deformation, even with thin materials
Please contact us today if you have sheet metal projects, particularly sheet metal punching, to receive the best advice and processing services at competitive prices.
NHAT NAM MECHANICAL CO., LTD contact information: House No. 36, Garland – Phuoc Dien, 72 Duong Dinh Hoi, Phuoc Long B Ward, District 9, Ho Chi Minh City, Vietnam.
Contact Japan
Email: tranquy@cokhinhatnam.vn
Tel: +84 938 771 508
Contact English
Email: marketing@cokhinhatnam.vn
Tel: +84 964 092 079
Contact Vietnam
Email: vinhnt@cokhinhatnam.vn
Tel: +84 964 084 479