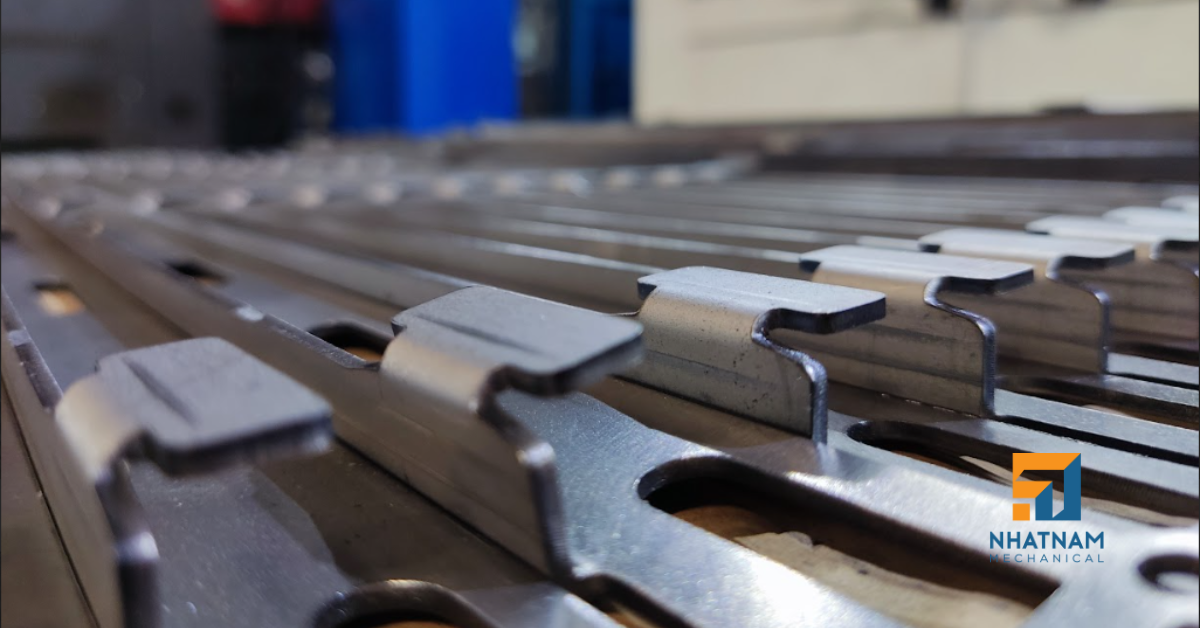
As the manufacturing industry enters a period of significant transformation, automation has become an indispensable factor in improving productivity, reducing costs, and ensuring quality. Sheet metal fabrication – a field that requires high precision and complex processes – is also part of this trend. However, in addition to its many benefits, automation also presents significant challenges for businesses.
Benefits of Automation in Sheet Metal Fabrication
1. High Accuracy and Consistency:
Automation eliminates the subjective factor in manual operations. Devices such as CNC laser cutting machines, automatic punching machines, and welding robots are pre-programmed with near-absolute accuracy. This results in:
- Products achieving high uniformity.
- Minimizing defective products due to technical errors.
- Meeting stringent tolerance requirements in manufacturing.
2. Increased Productivity and Production Speed:
Compared to manual labor, automated systems can operate continuously, stably, and at high speeds. This provides clear benefits in the production process:
- Product completion time is significantly shortened, from several days to just a few hours, depending on the complexity of the parts.
- Multiple stages, such as cutting, bending, and welding, can be performed simultaneously on the same production line, optimizing the process.
- Standardized and automated processes significantly shorten time to market, enhancing competitiveness.
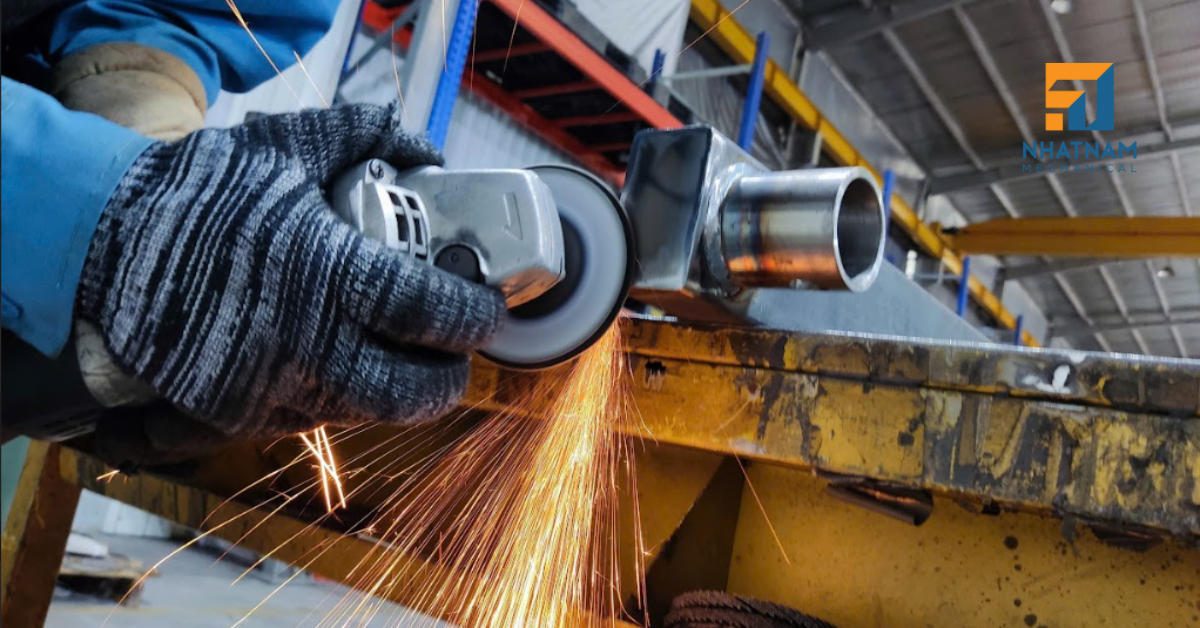
3. Long-Term Cost Savings:
Although initial investment costs may be high, in the long term:
- Automation reduces the number of operating workers.
- Fewer errors occur, saving material costs and reducing the need for error correction.
- Increases machine lifespan due to stable and proper operation.
4. Enhanced Occupational Safety:
Many stages in sheet metal fabrication pose a risk of accidents (cutting, stamping, welding, etc.). When replaced by robots or remote-control systems:
- Workers are less exposed to hazardous environments.
- Reduces workplace injuries and insurance costs.
5. Optimized Production Processes:
Automation is not just about using robots but also integrating control systems, data management, and remote monitoring. This allows for:
- Accurate real-time order management.
- Easy tracking of progress, performance, and material inventory.
- Quick response to customer changes.
Challenges of Implementing Automation
1. High Initial Investment Costs:
Purchasing automated machinery, control software, and redesigning factory layouts requires a significant budget. This is a major barrier, especially for small and medium-sized enterprises (SMEs).
2. Shortage of Highly Skilled Technical Personnel:
Automated machinery requires technicians with knowledge of:
- CNC and PLC programming.
- Automated equipment maintenance and repair.
- Operating design and production control software.
Therefore, businesses must invest more in recruitment or internal training, which can be both time-consuming and costly.
3. Difficulty Integrating into Existing Systems:
Automation is not always easy to implement. Legacy systems, traditional management processes, or a lack of standardized data can cause difficulties in:
- Synchronizing production data.
- Linking stages (from design to finished product).
- Connecting with enterprise management software (ERP, MES).
4. Maintenance and Update Costs:
Modern machinery may require:
- Regular scheduled maintenance.
- Replacement of hard-to-find specialized components.
- Frequent software updates to avoid security or operational errors.
Without a well-planned maintenance strategy, the system can break down and cause significant damage.
5. Dependence on Technology:
When the entire production line relies on automated systems:
- Any failure (breakdown, programming error, power outage, etc.) can cause a complete shutdown.
- Backup systems and rapid response plans are essential in case of risks.
Conclusion
Automation is gradually transforming the sheet metal fabrication industry – from traditional workshops to “smart factories.” If invested in and implemented correctly, it can provide a significant competitive advantage, helping businesses achieve sustainable development in the Industry 4.0 era.
However, businesses also need to recognize the challenges and develop appropriate strategies: starting from a small scale, training technical staff, and gradually transforming production processes in a reasonable manner.
At Nhat Nam Mechanical, we provide precise and efficient machining solutions using modern technology and a team of professional technicians. We are committed to delivering high-quality products on schedule and at reasonable prices, meeting the diverse needs of our customers in the industry.
NHAT NAM MECHANICAL CO., LTD contact information: House No. 36, Garland – Phuoc Dien, 72 Duong Dinh Hoi, Phuoc Long B Ward, District 9, Ho Chi Minh City, Vietnam.
Contact Japan
Email: tranquy@cokhinhatnam.vn
Tel: +84 938 771 508
Contact English
Email: marketing@cokhinhatnam.vn
Tel: +84 964 092 079
Contact Vietnam
Email: vinhnt@cokhinhatnam.vn
Tel: +84 964 084 479