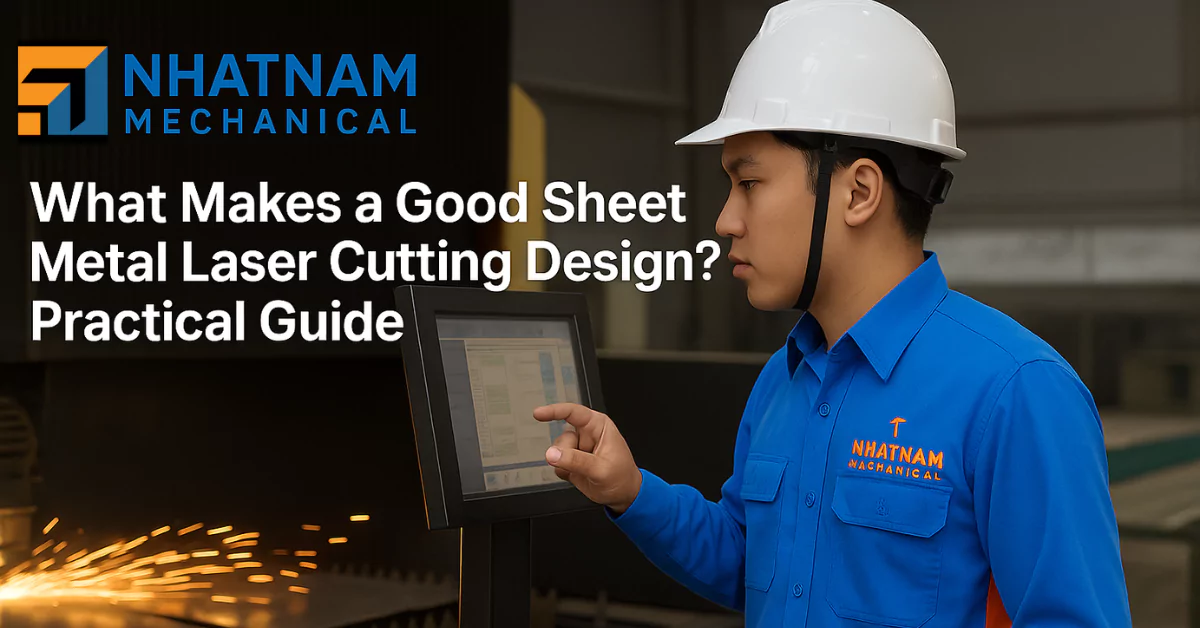
In the world of precision manufacturing, laser cutting has become the gold standard for clean, accurate, and efficient sheet metal fabrication. But even the most advanced laser machines can’t fix a flawed design.
A great sheet metal laser cutting design ensures:
Accurate results
Lower production cost
Smoother post-processing
Minimal material waste
In this practical guide, Nhat Nam’s engineering team shares key principles for designing laser-ready sheet metal parts that are production-ready from the start.
1. Simplify the Geometry
While lasers can cut intricate details, overly complex shapes:
- Slow down production
- Increase the chance of error
- Add unnecessary cost
Pro Tip: Favor clean lines, rounded internal corners, and avoid ultra-small details unless truly necessary.
2. Design Based on the Material
Not all metals behave the same. For example:
- Aluminum dissipates heat quickly
- Stainless steel holds its shape but may require slower speeds
- Thin mild steel may warp without proper spacing
At Nhat Nam, we help you select the right material and thickness for laser cutting efficiency and final use.
3. Account for the Laser’s Kerf
The kerf (laser cut width) can affect how your parts fit together. It’s usually between 0.1 mm – 0.5 mm depending on the laser and material.
Always adjust your design for kerf, especially in slot-tab assemblies, interlocking parts, or high-tolerance applications.
4. Optimize Cutting Paths
Efficient cut paths = faster jobs and lower costs.
Smart design includes:
- Nesting multiple parts together
- Using shared edges where possible
- Avoiding redundant paths
Our engineers use advanced nesting software to maximize material yield and minimize waste.
5. Manage Heat-Affected Zones (HAZ)
Laser cutting generates heat. Poor designs may suffer:
Warping or distortion
Burn marks on edges
Dimensional inaccuracies
Keep adequate spacing between close cuts, avoid dense hole patterns, and let us simulate HAZ before production.
6. Think Ahead to Bending & Assembly
Laser cutting is often followed by:
- CNC bending or forming
- Welding
- Surface finishing (e.g., powder coating)
Good laser design supports these steps, with appropriate bend reliefs, joint gaps, and finishing clearance built into the model.
Nhat Nam Mechanical is a leading manufacturer and processor of steel components in Vietnam. With many years of experience in the industry, we specialize in providing high-quality mechanical solutions for industries such as automotive, electronics, construction, and interiors. Nhat Nam Mechanical focuses on applying modern technology and precise production processes, ensuring that we meet all of our customers’ strict requirements for quality and delivery time. We are committed to delivering sheet metal products and mechanical components that are machined with precision, helping to optimize the production process and improve work efficiency.
NHAT NAM MECHANICAL CO., LTD contact information: House No. 36, Garland – Phuoc Dien, 72 Duong Dinh Hoi, Phuoc Long B Ward, District 9, Ho Chi Minh City, Vietnam.
Contact Japan
Email: tranquy@cokhinhatnam.vn
Tel: +84 938 771 508
Contact English
Email: marketing@cokhinhatnam.vn
Tel: +84 964 092 079
Contact Vietnam
Email: vinhnt@cokhinhatnam.vn
Tel: +84 964 084 479