Introduction
Finishing is the process of refining and enhancing the surface of sheet metal components after fabrication. This essential step involves techniques like polishing, coating, or anodizing to boost both the appearance and performance of the metal. Each method is chosen and applied with specialized tools to achieve the desired result—be it a sleek, glossy surface or a tough, protective shield. Through careful treatment, we ensure every piece meets high standards of quality and consistency.
At Nhat Nam, we deliver outstanding finishing services adjusted to a wide range of customer needs. With cutting-edge technology and a dedicated team, we provide surface treatment solutions for industries spanning manufacturing, consumer goods, and more.
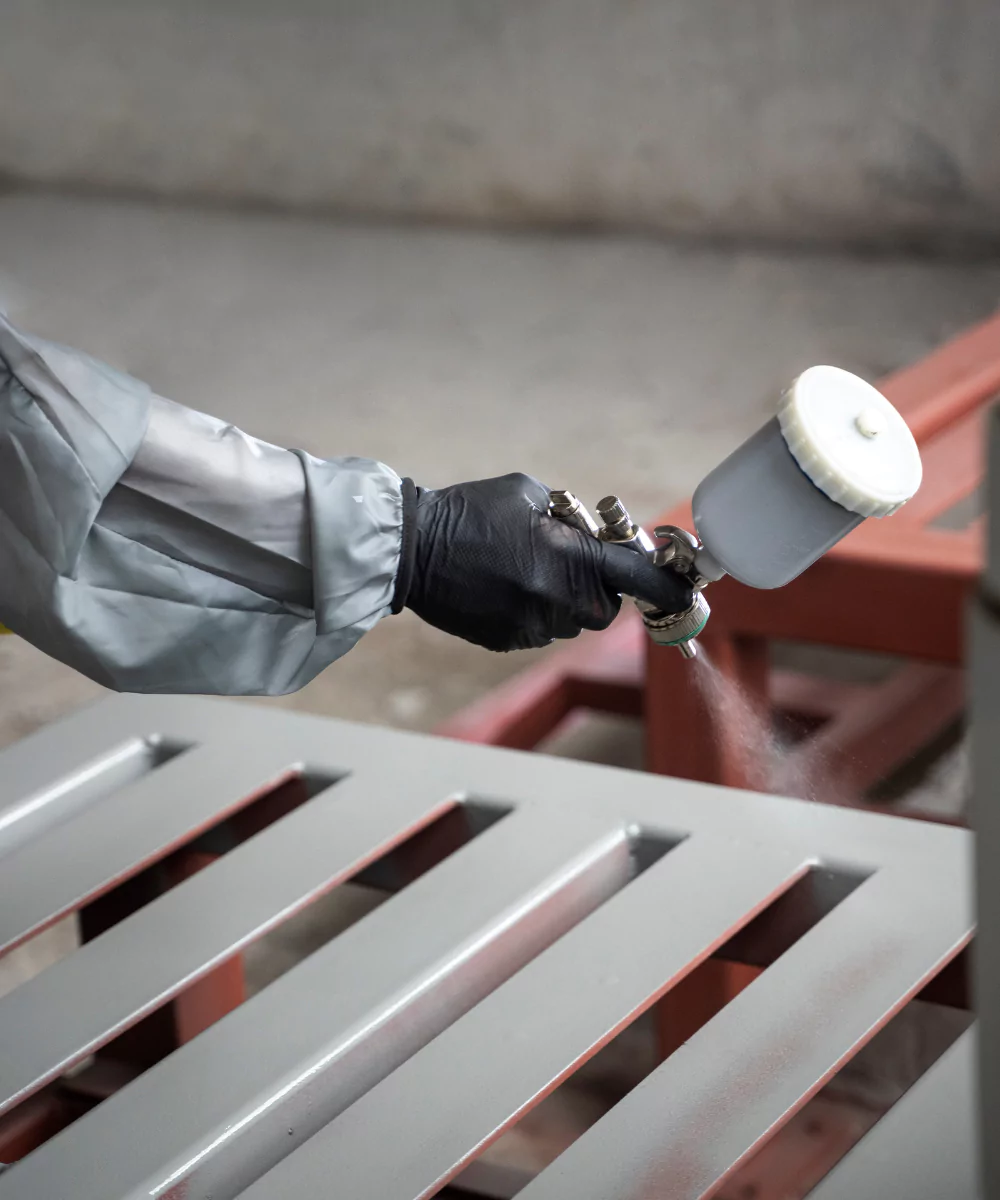
CAPABILITIES
Our team of experienced technicians brings skill and attention to detail to every job, ensuring finishes that are both precise and reliable. We use modern, high-quality equipment to handle a variety of surface treatment techniques—like polishing, powder coating, and anodizing— delivering consistent results every time. Whether you’re after a polished shine or a rugged protective layer, we customize our process to fit your specific goals, creating finishes that look great and last long.
With a wide range of options, we’re ready to tackle all kinds of finishing needs with practical know-how and dependable tools:
- Coatings and Paints
- Anodizing
- Plating
- Chemical Treatments
- Heat Treatments
- Surface Finishing
TYPES OF SERVICES
Drawing from our expertise and advanced capabilities, Nhat Nam offer a wide range of finishing services, thoughtfully grouped to meet your project needs:
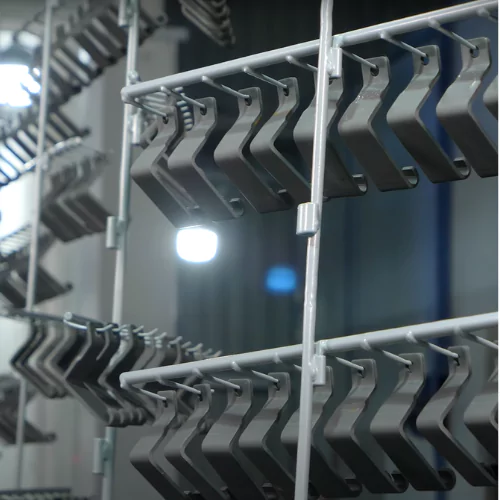
Coatings and Paints
- Powder Coating: A durable, colorful layer cured under heat for corrosion resistance.
- Wet Paint: Smooth, customizable liquid paint for vibrant finishes and protection.
- Dry Film Lubricants: Reduces friction and wear for high-performance parts.
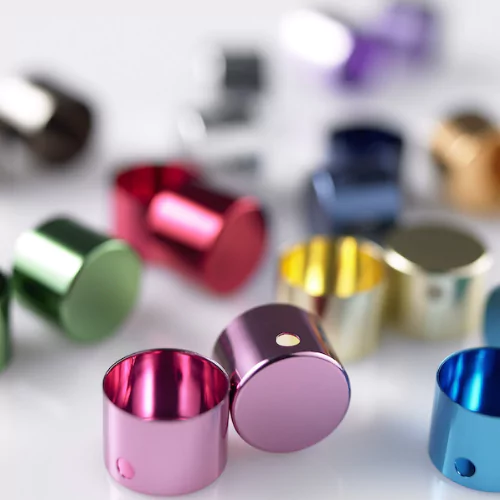
Anodizing
- Type II Anodize: Moderate oxide layer on aluminum for corrosion resistance and dye options
- Type III Hard Coat: Thicker, tougher finish for superior durability.
- Type III with PTFE: Adds low-friction properties to hard anodizing.
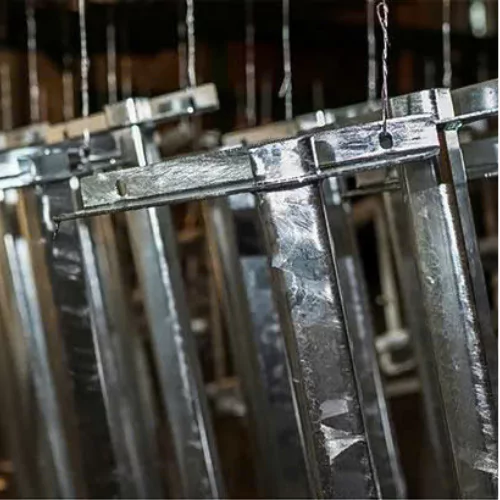
Plating
- Electroless Nickel: Uniform nickel layer for hardness and corrosion resistance.
- Electro Zinc: Cost-effective rust protection for steel.
- Chrome: Withstand regular wear, and tear, distinctive, shiny look.
- Hot-Dip Galvanizing: Protects steel from corrosion, extremely abrasion resistant.
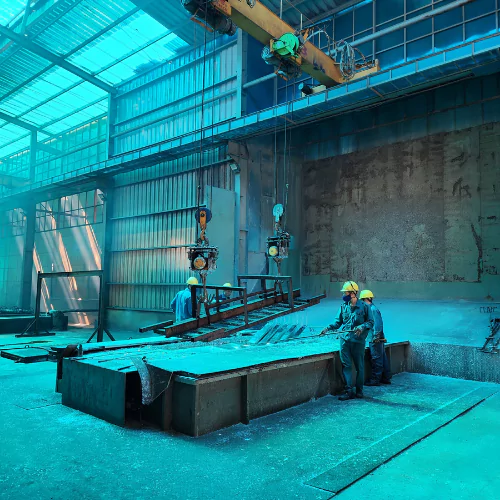
Chemical Treatments
- Black Oxide: Dark, anti-reflective finish with corrosion resistance.
- Chem Film (Chemical Conversion Coating): Light protective layer for paint adhesion.
- Chromate: Thin film for added durability on zinc or aluminum.
- Conversion Coating: Enhances corrosion protection as a base layer.
- Passivation: Cleans stainless steel to maximize corrosion resistance.
- Pickle and Oil: Removes impurities and prevents rust.
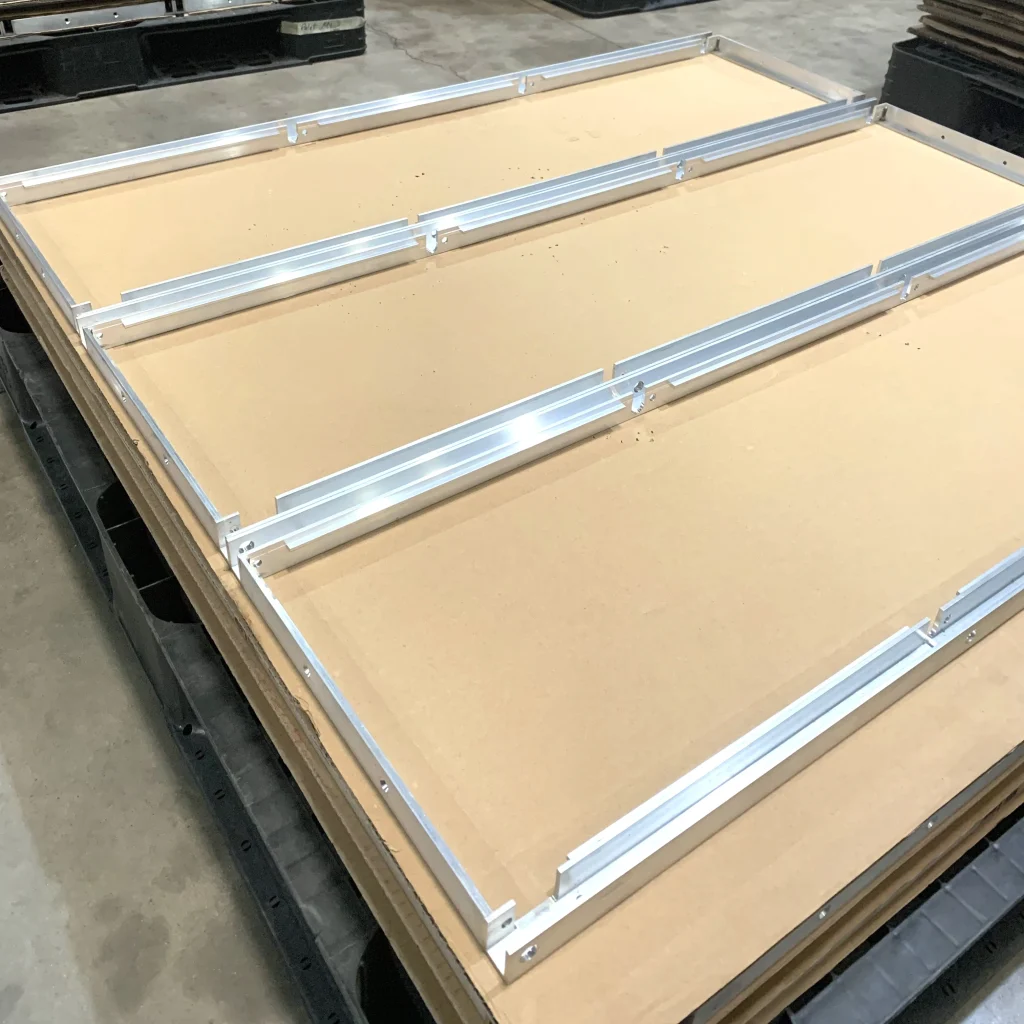
Surface Finishing
- Polishing: Creates a glossy, reflective finish for looks and durability.
- Brushing: Delivers a subtle satin finish with linear patterns
- Sandblasting (Bead Blasting): Textures or cleans surfaces with abrasives.
- Electropolishing: Smooths and brightens metal for a clean, shiny look.
- Etching: Adds precise patterns or markings for design or function.
FAQs
What materials can you finish?
We handle a variety of metals, including steel, aluminum, and stainless steel.
How long does the finishing process take?
It depends on the project’s complexity, but we prioritize speed without sacrificing quality.
Can you handle custom finishing requests?
Yes! We adapt our services to your unique needs—just share your ideas with us.
What industries do you serve?
We support sectors like OEM, construction, electronics, furniture production, and beyond.
Why Chose Us?
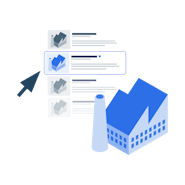
Our dedicated experts work closely with you every step of the way to design, develop, and deliver the precision-crafted part and customized product.
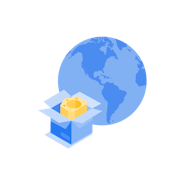
With ISO 9001 Certification and ANSI Certification, only the top shops that apply to become network suppliers make it through our qualification process.
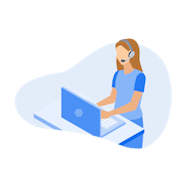
Our team of Application Engineers and Process Specialists are available to support you and provide answers to all of your fabrication and manufacturability questions.