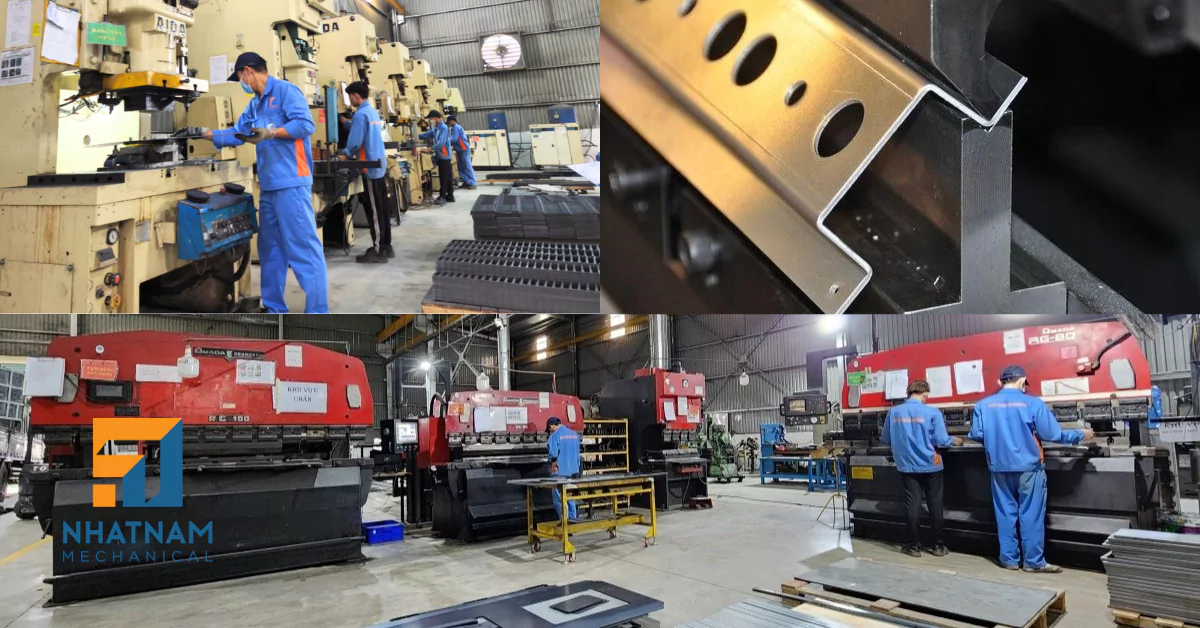
In the mechanical field, sheet metal forming is an indispensable step in the production of components and products for a variety of industries. From cutting, stamping, to bending and surface treatment, each process contributes to shaping and improving product quality. So, how does this process take place and how is it applied in practice? Let’s find out more about it:
1. What is sheet metal forming?
Sheet metal forming is the process of reshaping sheet metal into the desired shape using different machining methods. This process not only requires high precision but also must ensure material optimization and suitability to the application requirements of each product.
Sheet metal forming is extremely popular in manufacturing, and sheet metal parts can be found in many applications, such as the automotive industry, aerospace industry, consumer goods, and home appliances.
2. Some current sheet metal forming methods
Cutting
The cutting process is the first step to form sheet metal into the desired size and shape:
- Laser cutting: Using a laser to cut sheet metal with high precision, suitable for complex details.
- Plasma cutting: Effective with thick metals, using heat from plasma to cut.
- Mechanical cutting: Using scissors, guillotine cutting machines, or hydraulic presses to cut sheet metal.
Punching and Stamping
Punching uses a punching machine and mold to shape or punch holes in sheet metal.
- Punching: Creating holes of different sizes and shapes.
- Stamping: Creating 3D shapes such as logos, ribs, or embossed details.
- Often applied in mass production at high speed.
Bending: this method is used to create specific angles, curves, or shapes:
- Bending with CNC press brake: For high precision, suitable for complex designs.
- Manual bending: Suitable for simple products or small quantity production.
3. What are the steps in the sheet metal forming process?
Step 1: Preparing materials
- Select the appropriate metal type: stainless steel, aluminum, copper, or other alloys.
- The metal sheet is cut to the required size from coils or large sizes.
Step 2: Cutting
- Laser cutting: High precision, suitable for complex details.
- Plasma cutting: Suitable for thicker metals.
- Mechanical cutting: Using scissors, guillotine cutting machine.
Step 3: Punching and Stamping
For details that need to be punched to create flanges, a metal punching process is required.
- Create holes or shapes on the surface of the metal sheet through a stamping die.
- This method is often used in mass production at high speed.
Step 4: Forming and bending
The parts have been processed according to the drawing, the edges are bent to increase hardness, and the parts can be assembled together. The bending machine needs to adjust to the right angle. The bending cutter also needs to be selected to be compatible with the part that needs to be bent.
Step 5: Welding the parts
For some accessories that have additional parts, the help of welding machines, welding robots, etc., is needed to create a complete product. After welding, the welds will be smoothed, and the welding slag scraped off before being sent to the next stage.
Step 6: Material surface treatment
This step is quite important, as it determines the quality of the output product. With steel materials, after processing, they will be galvanized, chrome-plated, or powder-coated. With stainless steel, the welds need to be smoothed and polished so that the welds are shiny and not exposed.
4. Applications of sheet metal forming in production
- Automotive Industry: Sheet metal forming plays a key role in the production of automotive parts. Details such as car frames, car bodies, engine parts, and interiors, etc.
- Electronics Manufacturing Industry: Sheet metal forming is used to produce electronic device casings, helping to protect internal components from impact and dirt. For example: computer casings, laptops, phones, and household appliances such as refrigerators, microwaves, washing machines, etc.
- Construction and Architecture Industry: In the construction industry, sheet metal is used to create construction details with high durability and good aesthetics. These details can be wall or ceiling panels and decorations, doors and windows, roof panels, stair treads, etc.
- Medical Equipment Manufacturing Industry: Sheet metal is used to produce medical equipment with high precision, good durability, and good bearing capacity. For example: surgical instruments, hospital beds, trolleys, etc.
- Aerospace Industry: Sheet metal forming also plays an important role in the aerospace industry. For example: aircraft frames, wings, and other engine parts, etc.
- Electricity and Energy Industry: Sheet metal is also used in the production of electrical and energy equipment such as shields, generator parts, etc.
- Food and Beverage Industry: In the food and beverage industry, sheet metal forming helps produce food processing and preservation equipment, including: food and beverage containers and boxes, some machinery components in food processing such as mixers, packaging machines, etc.
Conclusion
Sheet metal forming not only plays an important role in the mechanical industry but is also widely applied in many different fields, from automotive, electronics, and construction to medicine, energy, and more. These applications not only help produce durable, precise products but also open up many opportunities for the development of modern industries.
At Nhat Nam Mechanical, we provide high-quality sheet metal forming services that meet all strict technical requirements from various industries. With a team of experienced technicians and modern equipment, we specialize in processing sheet metal products through methods such as cutting, stamping, bending, and punching. Our products are guaranteed to offer precision, durability, and aesthetics, serving a variety of sectors, including automotive, electronics, construction, and energy. Come to Nhat Nam Mechanical to experience top-notch, reputable sheet metal forming services!
Contact Us.
NHAT NAM MECHANICAL CO., LTD contact information: House No. 36, Garland – Phuoc Dien, 72 Duong Dinh Hoi, Phuoc Long B Ward, District 9, Ho Chi Minh City, Vietnam
Contact Japan
Email: tranquy@cokhinhatnam.vn
Tel: +84 938 771 508
Contact English
Email: marketing@cokhinhatnam.vn
Tel: +84 964 092 079
Contact Vietnam
Email: vinhnt@cokhinhatnam.vn
Tel: +84 964 084 479